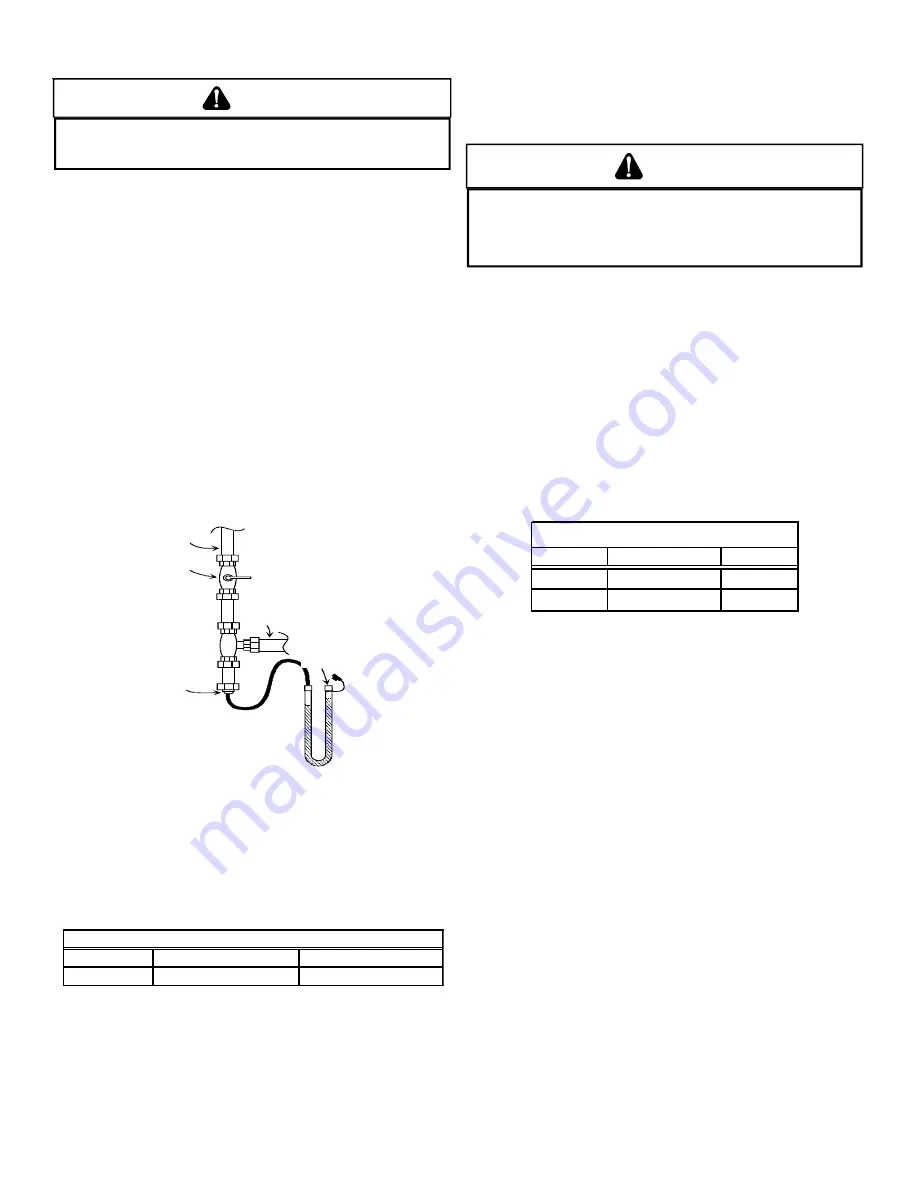
22
IO-242
5/04
6. Turn OFF any unnecessary gas appliances started in step
3.
G
AS
M
ANIFOLD
P
RESSURE
M
EASUREMENT
AND
A
DJUSTMENT
CAUTION
T
O PREVENT UNRELIABLE OPERATION OR EQUIPMENT DAMAGE, THE GAS
MANIFOLD PRESSURE MUST BE AS SPECIFIED ON THE UNIT RATING PLATE.
O
NLY MINOR ADJUSTMENTS SHOULD BE MADE BY ADJUSTING THE GAS VALVE
PRESSURE REGULATOR.
Only small variations in gas pressure should be made by adjusting
the gas valve pressure regulator. The manifold pressure must be
measured with the burners operating. To measure and adjust the
manifold pressure, use the following procedure.
1. Turn OFF gas to furnace at the manual gas shutoff valve
external to the furnace.
2. Connect a calibrated water manometer (or appropriate gas
pressure gauge) at the gas valve outlet pressure tap (refer
to gas valve figure in previous section).
3. Turn ON the gas supply and operate the furnace.
4. Measure gas manifold pressure with burners firing. Adjust
manifold pressure according to the
Manifold Gas Pressure
table:
Gas
Range
Nominal
Natural
3.0 - 3.6" w.c.
3.5" w.c.
Propane
9.7 - 10.3" w.c.
10.0" w.c.
Manifold Gas Pressure
The final manifold pressure must not vary more than ± 0.3 “ w.c.
from the above specified pressures. Any necessary major changes
in gas flow rate should be made by changing the size of the burner
orifice.
5. To adjust the gas valve pressure regulator, remove the
regulator cap.
6. Turn the adjustment screw clockwise to increase the
pressure, or counterclockwise to decrease the pressure.
7. Securely replace the regulator cap.
8. Turn OFF gas to furnace at the manual shutoff valve and
disconnect manometer.
9. Reinstall gas valve outlet pressure tap plug before turning
on gas to furnace.
G
AS
I
NPUT
R
ATE
M
EASUREMENT
(N
ATURAL
G
AS
O
NLY
)
The gas input rate to the furnace must never be greater than that
specified on the unit rating plate. To measure natural gas input
using the gas meter, use the following procedure.
1. Turn OFF the gas supply to all other gas-burning appliances
except the furnace.
2. While the furnace is operating, time and record one complete
revolution of the smallest gas meter dial.
3. Calculate the number of seconds per cubic foot (sec/ ft
3
) of
gas being delivered to the furnace. If the dial is a one cubic
foot dial, divide the number of seconds recorded in step 2
by one. If the dial is a two cubic foot dial, divide the number
of seconds recorded in step 2 by two.
G
AS
S
UPPLY
P
RESSURE
M
EASUREMENT
oper
at
ing.
CAUTION
T
O PREVENT UNRELIABLE OPERATION OR EQUIPMENT DAMAGE, THE INLET
GAS SUPPLY PRESSURE MUST BE AS SPECIFIED ON THE UNIT RATING PLATE
WITH ALL OTHER HOUSEHOLD GAS FIRED APPLIANCES OPERATING.
The line pressure supplied to the gas valve must be within the
range specified below. The supply pressure can be measured at
the gas valve inlet pressure tap or at a hose fitting installed in the
gas piping drip leg. The supply pressure must be measured with
the burners operating. To measure the gas supply pressure, use
the following procedure.
With Power and Gas Off:
1. Connect a water manometer or adequate gauge to the “inlet
pressure tap” of the gas valve.
As an alternative method, inlet gas pressure can also be
measured by removing the cap from the drip leg and
installing a predrilled cap with a hose fitting (Figure 26).
With Power and Gas On:
2. Put furnace into heating cycle and turn on all other gas
consuming appliances.
If operating pressures differ from the
Inlet Gas Supply Pressure
table below, make necessary pressure regulator adjustments, check
piping size, etc., and/or consult with local utility.
G a s L in e
G a s
S h u t o f f
V a l v e
G a s L in e
T o F u r n a c e
D r ip L e g C a p
W it h F it ti n g
M a n o m e te r H o s e
M a n o m e t e r
O p e n T o
A tm o s p h e r e
Measuring Inlet Gas Pressure (Alternate Method)
3. Turn ON the gas supply and operate the furnace and all
other gas consuming appliances on the same gas supply
line.
4. Measure furnace gas supply pressure with burners firing.
Supply pressure must be within the range specified in the
table below.
Natural Gas
Minimum: 5.0" w.c.
Maximum:10.0" w.c.
Propane Gas Minimum: 11.0" w.c.
Maximum:13.0" w.c.
Inlet Gas Supply Pressure
If supply pressure differs from table, make the necessary
adjustments to pressure regulator, gas piping size, etc., and/or
consult with local gas utility.
5. Turn OFF gas to furnace at the manual shutoff valve and
disconnect manometer. Reinstall plug before turning on
gas to furnace.