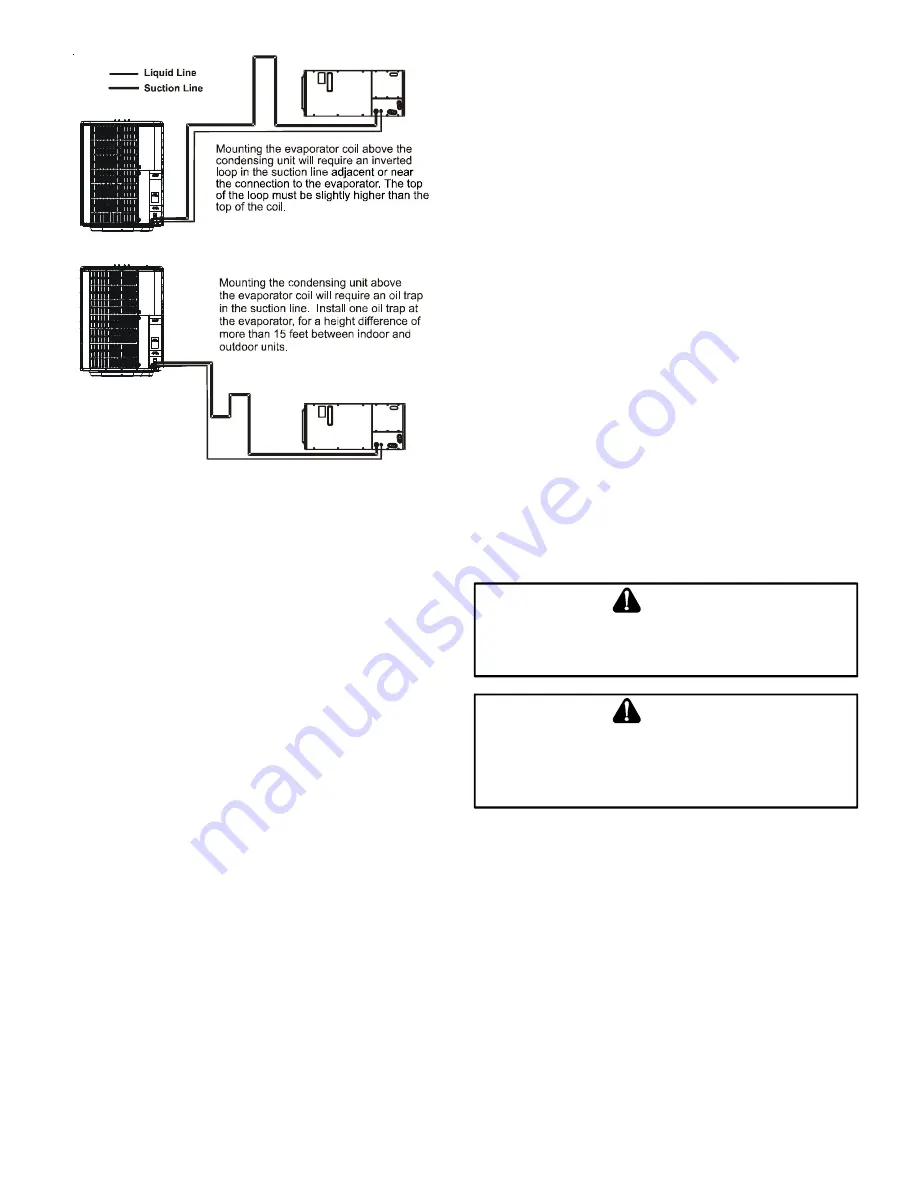
4
B
URYING
R
EFRIGERANT
L
INES
If burying refrigerant lines can not be avoided, use the following
checklist.
1. Insulate liquid and suction lines separately.
2. Enclose all underground portions of the refrigerant lines
in waterproof material (conduit or pipe) sealing the ends
where tubing enters/exits the enclosure.
3. If the lines must pass under or through a concrete slab,
ensure lines are adequately protected and sealed.
R
EFRIGERANT
L
INE
C
ONNECTIONS
IMPORTANT
To avoid overheating the service valve, TXV valve,
or filter drier while brazing, wrap the component with
a wet rag, or use a thermal heat trap compound. Be
sure to follow the manufacturer’s instruction when
using the heat trap compound. Note: Remove
Schrader valves from service valves before brazing
tubes to the valves. Use a brazing alloy of 2%
minimum silver content. Do not use flux.
Torch heat required to braze tubes of various sizes
is proportional to the size of the tube. Tubes of
smaller size require less heat to bring the tube to
brazing temperature before adding brazing alloy.
Applying too much heat to any tube can melt the
tube. Service personnel must use the appropriate
heat level for the size of the tube being brazed. NOTE:
The use of a heat shield when brazing is
recommended to avoid burning the serial plate or
the finish on the unit.
1. The ends of the refrigerant lines must be cut square,
deburred, cleaned, and be round and free from nicks or
dents. Any other condition increases the chance of a
refrigerant leak.
2. “Sweep” the refrigerant line with nitrogen or inert gas
during brazing to prevent the formation of copper-oxide
inside the refrigerant lines. The POE oils used in R-
410A applications will clean any copper-oxide present
from the inside of the refrigerant lines and spread it
throughout the system. This may cause a blockage or
failure of the metering device.
3. After brazing, quench the joints with water or a wet cloth
to prevent overheating of the service valve.
4. Ensure the filter drier paint finish is intact after brazing.
If the paint of the steel filter drier has been burned or
chipped, repaint or treat with a rust preventative. This is
especially important on suction line filter driers which
are continually wet when the unit is operating.
NOTE:
Be careful not to kink or dent refrigerant lines. Kinked
or dented lines will cause poor performance or compressor
damage.
Do NOT make final refrigerant line connection until plugs
are removed from refrigerant tubing.
NOTE:
Before brazing, verify indoor TXV is correct for R410A
and proper size.
L
EAK
T
ESTING
(N
ITROGEN
OR
N
ITROGEN
-T
RACED
)
T
O
AVOID
THE
RISK
OF
FIRE
OR
EXPLOSION
,
NEVER
USE
OXYGEN
,
HIGH
PRESSURE
AIR
OR
FLAMMABLE
GASES
FOR
LEAK
TESTING
OF
A
REFRIGERATION
SYSTEM
.
WARNING
T
O
AVOID
POSSIBLE
EXPLOSION
,
THE
LINE
FROM
THE
NITROGEN
CYLINDER
MUST
INCLUDE
A
PRESSURE
REGULATOR
AND
A
PRESSURE
RELIEF
VALVE
.
T
HE
PRESSURE
RELIEF
VALVE
MUST
BE
SET
TO
OPEN
AT
NO
MORE
THAN
150
PSIG
.
WARNING
Pressure test the system using dry nitrogen and soapy water
to locate leaks. If you wish to use a leak detector, charge the
system to 10 psi using the appropriate refrigerant then use
nitrogen to finish charging the system to working pressure
then apply the detector to suspect areas. If leaks are found,
repair them. After repair, repeat the pressure test. If no leaks
exist, proceed to system evacuation.
S
YSTEM
E
VACUATION
Condensing unit liquid and suction valves are closed to con-
tain the charge within the unit. The unit is shipped with the
valve stems closed and caps installed.
Do not open valves
until the system is evacuated.