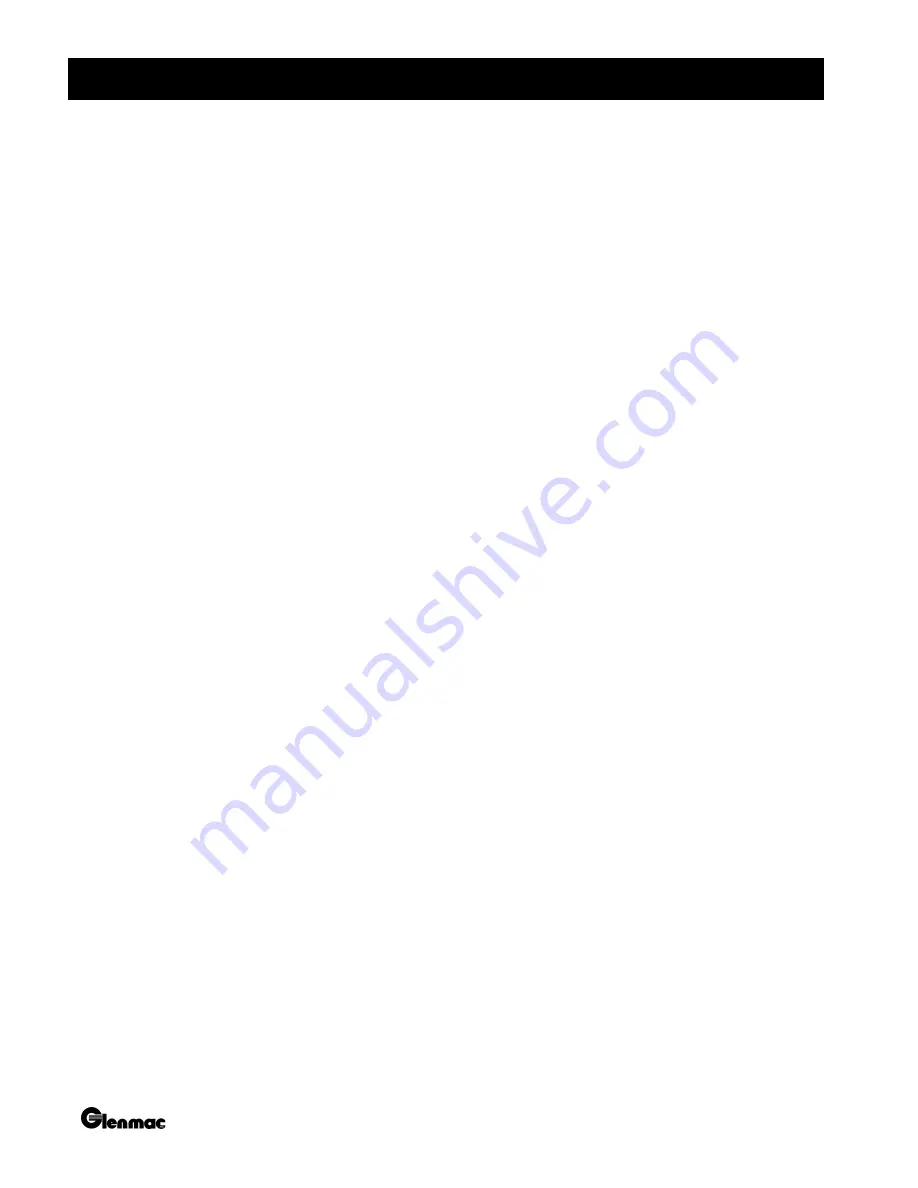
38
PN-P970612 (06/2005)
LIMITED WARRANTY
Glenmac Inc warrants
its line of Harley equipment to be free from defects in material and factory workmanship
for a period of twelve (12) months. Exception to this warranty period will be Harley Rock Pickers, which will
carry a six- (6) month warranty.
Warranty registration
form must be filled out, signed by the customer and returned to Glenmac within thirty (30)
days from the date of purchase before any warranty claim will be considered. Dealer rental units are considered
sold units and the same warranty policy applies.
This warranty is limited
exclusively to equipment manufactured by Glenmac Inc and is subject to inspection by
Glenmac Inc to identify the nature and cause of failure. This company in no way warrants belts, bearings, hydrau-
lics, chains, sprockets, tires or any other trade accessory not manufactured by Glenmac Inc since these items are
warranted separately by their respective manufactures.
This warranty shall become void
if in the best judgement of Glenmac Inc the equipment has been subject to
misuse, negligence, alterations, and damage by accident or lack of required maintenance or if the product has been
used for a purpose for which it was not intended. Wear items such as, but not limited to, rollers and drive chains
will not be covered under warranty. Normal wear depreciation is not covered by warranty. Claims for equipment
damaged in transit should be referred to the freight carrier. Glenmac will not be responsible for damages incurred
in transit.
Glenmac Inc obligations
under this warranty shall be limited to repair or replacement at its option of the equip-
ment or trade accessories as they conform to this policy. Trade accessories such as but not limited to bearings,
tires and wheels etc will be sent to the respective manufacturer for warranty consideration. Any warranty reim-
bursement as related to these items will rely solely on the decision of each separate manufacture including
Glenmac Inc. Reimbursement on parts will be at dealer net and labor allowances are calculated according to
Glenmac’s predetermined flat time and rate. Freight charges and misc. shop supplies are not covered under
warranty.
Dealer’s responsibility
is to fully explain the warranty policy to the customer before starting any repairs. Return
the defective parts (prepaid) along with a completed Glenmac Inc warranty form. All replacement parts used in
warranty must be furnished by Glenmac Inc. (Please refer to warranty procedures). The selling dealer has no
authority to make any representation or promise on behalf of Glenmac/Harley Enterprises or to modify the terms
or conditions of this warranty in any way.
Owner’s responsibility
is to complete and return the warranty registration within thirty (30) days from the date
of purchase. Operate and maintain the equipment according to the recommendations in the owner’s manual. The
owner is responsible for freight and transportation to and from the dealership or any service calls made by the
dealer.
This warranty is subject to any conditions of supply, which may directly affect our ability to obtain materials or
manufacture replacement parts.
Glenmac Inc reserves the right to make improvements in design or change in specifications of its products without
notice and is not obligated to make the same improvements to equipment previously
manufactured.
THERE IS NO OTHER EXPRESSED OR IMPLIED WARRANTY ON THIS PRODUCT OR ON ITS
MERCHANTABILITY OR ON ITS FITNESS. TO THE EXTENT ALLOWED BY LAW NIETHER
GLENMAC INC NOR THE SELLING HARLEY DEALER SHALL HAVE ANY RESPONSIBILITY FOR
LOSS OF USE OF THE PRODUCT, LOSS OF TIME, INCONVENIENCE, COMERCIAL LOSS OR CON-
SEQUENTIAL DAMAGES.
Summary of Contents for Harley T6
Page 1: ......
Page 13: ...11 PN P970612 06 2005 ATTENTION BECOMEALERT YOUR SAFETYIS INVOLVED SAFETY DECALS Figure 1...
Page 19: ...17 PN P970612 06 2005 OPERATION Figure 2...
Page 22: ...20 PN P970612 06 2005 Figure 3 MAINTENANCE...
Page 29: ...27 PN P970612 06 2005 NOTES...
Page 30: ...28 PN P970612 06 2005 Figure 6 FRAME ASSEMBLY...
Page 32: ...30 PN P970612 06 2005 Figure 7 ROLLER ASSEMBLY...
Page 34: ...32 PN P970612 06 2005 CLUTCH ASSEMBLY Figure 8...
Page 36: ...34 PN P970612 06 2005 CLUTCH PTO DRIVE LINES Figure 9...