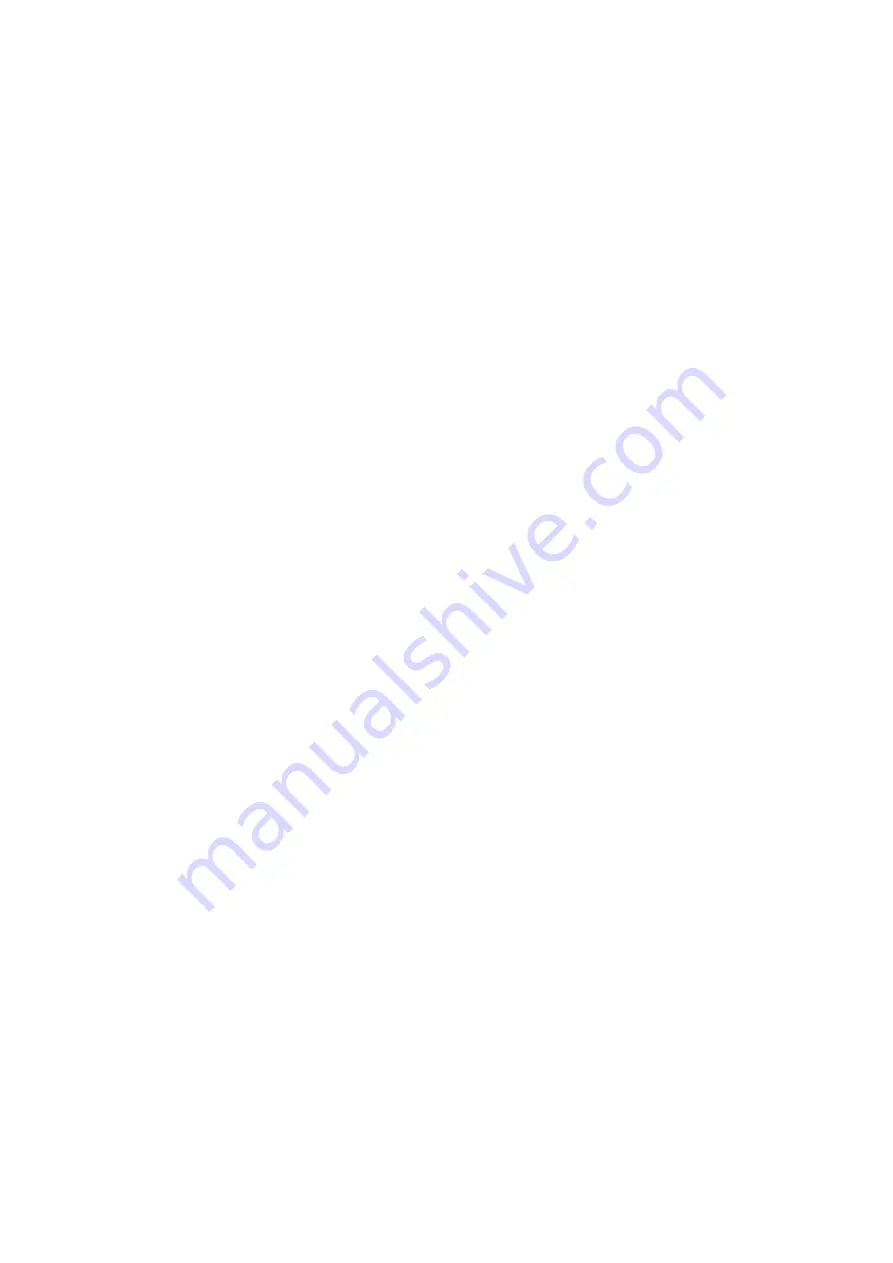
Page 3
Maintenance
Modifications should not be made to this
product. Replacement parts, including
immersion heaters, should be purchased from
Gledhill Building Products Limited, or agents
approved by them. Unvented hot water storage
vessels need regular routine checks, and these
are detailed below. It is for this reason that this
manual must always be left with the Platinum.
It is essential that these checks be carried out
at the time of boiler maintenance by a qualified
installer:
1. Manually open the relief valves in turn, and
check that water is discharged from the
valves and runs freely through the tundish
and out at the discharge point. Ensure that
the valves re-seat satisfactorily. (Note - the
water may be very hot).
2. It is important to check that the discharge
pipework is carrying the water away
adequately. Check for blockages etc. if it is
not.
3. Turn the mains water off and remove and
clean the strainer element in the Pressure
Reducing Valve.
4. Re-fill the system and ensure that all relief
valves have re-seated.
5. The Benchmark Service Record should be
updated at each service.
6. Check the water pressure downstream of the
combination valve is 3 bar in static condition.
7. Check and if necessary, descale the heat
exchanger in hard water areas ie. above
200ppm (mg/l).
Note:
The cylinder is factory fitted with a temperature
& pressure relief valve that must not be used for
any other purpose or removed.
The cylinder is factory fitted with immersion
heaters with thermal cut outs. Immersions
without thermal cut outs must not be fitted.
The cylinder may be examined internally by
removing an immersion heater and inserting
an endoscope inspection camera through the
immersion boss connection.
Manufacturer: Gledhill Building Products Ltd
Maximum inlet pressure to
Pressure
reducing
valve
12
bar
Operating pressure (PRV setting)
3 bar
Additional expansion vessel charge for secondary circulation
3 bar
Expansion relief valve setting
8 bar
Opening pressure of P & T Relief Valve
10 bar
Opening temperature of P & T Relief Valve
95°C
Energy cut-out thermostat setting
85°C
Max. working pressure - Primary heat exchanger (Indirect models) 3 bar
Immersion heater rating
3kW, 240V AC
All cylinders are manufactured in accordance with the requirements of BS EN 12897:2016.
The tundish must be positioned so that it is visible to the occupant and is away from
electrical devices.
The primary heat exchanger normal/test operation temperature is 80+/- 2°C.
It is also tested to 110+/-2°C to prove the function of the safety devices.
Components supplied with Platinum:
• Cold water inlet PRV combination valve/expansion relief
• Pressure and temperature relief valve
• Control thermostat
• Energy cut-out thermostat
• Energy cut-out motorised valve (indirects only)
• Tundish
• Drain valve
• 3kW Immersion heater including control and cut out thermostats
• Technical/user product literature
(
Note:
Please refer to tables on pages 6-9 to confirm the quantity of immersion heaters
supplied with the unit)
In any situation where the volume of heated pipework (eg. secondary circulation
pipes or manifold pipework for multiple units) exceeds 10 litres, then an
expansion vessel must be fitted to accommodate the extra expansion volume.
Handling Before Installation
Platinum must be handled with care and stored the correct way up in a dry place.
Any manual handling/lifting operations will need to comply with the requirements
of the Manual Handling Operations Regulations issued by the H.S.E. The appliance
can be moved using a sack truck on the rear face although care should be taken and
the route should be even. In apartment buildings containing a number of storeys we
would recommend that the appliances are moved vertically in a mechanical lift. If it is
proposed to use a crane, expert advice should be obtained regarding the need for
slings, lifting beams etc.
All factory fitted components are tightened during manufacture, however all should
be checked before installation.
A specific manual handling assessment is shown in Appendix B at the rear of this
manual.
The Environment
This product has been manufactured using many recyclable materials, including the
approved HCFC/CFC free polyurethane foam insulation. At the end of its useful life, it
should be disposed of at a Local Authority Recycling Centre, to maximise the products
full environmental benefits.
DESIGN
DESCRIPTION
Summary of Contents for PLATINUM D120
Page 45: ...Page 45 NOTES ...
Page 46: ...Page 46 NOTES ...