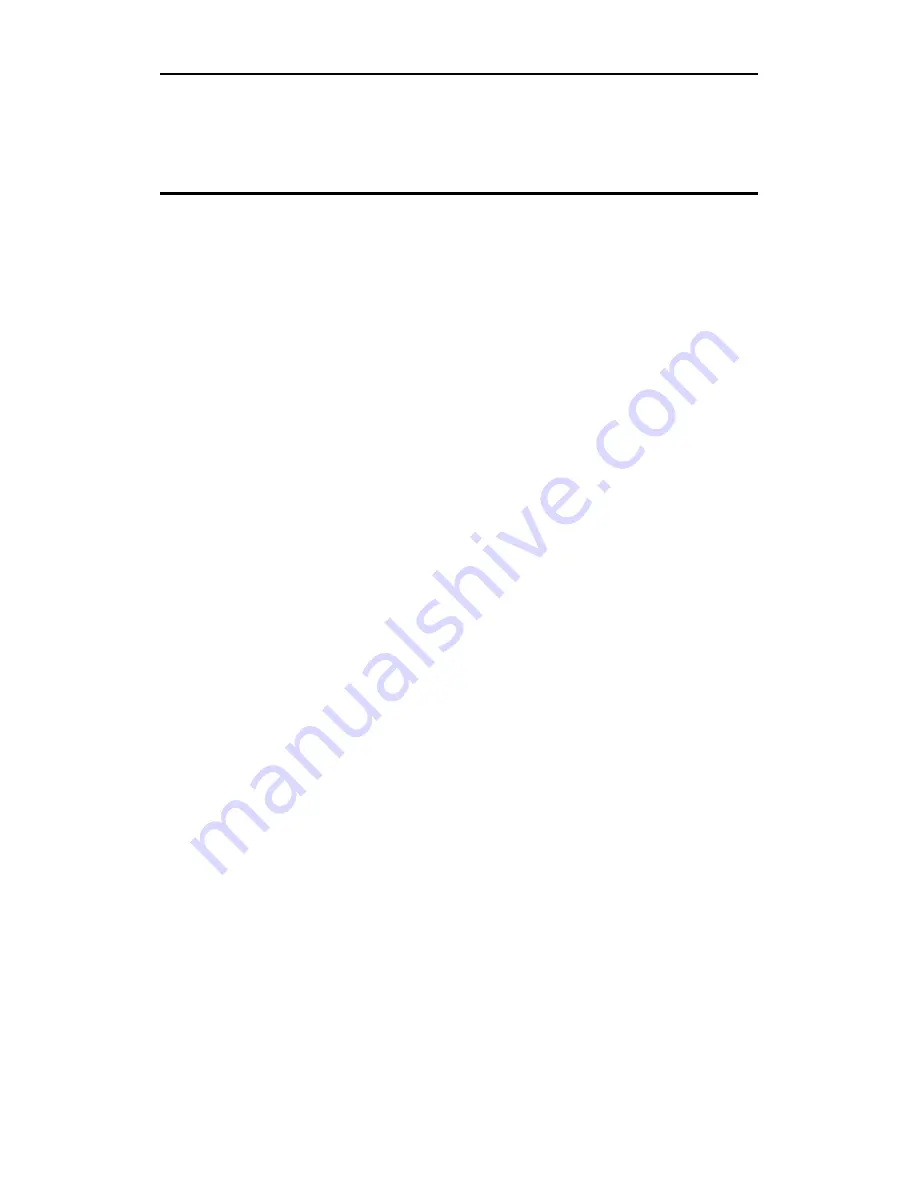
8
Engraver Option
Engraving Basics
This section presents information about materials, cutting tools, and types of
engraving operations.
Materials and cutting tools
Engraving materials have the following general properties:
hardness
surface layer thickness
finish
Cutting tools have the following properties:
sharpness
width
purpose of the engraving type
The following paragraphs describe the relationships among the material and tool
properties, as well as other factors such as speed and feed rates.
Hardness, sharpness, cutter rpm, and feed rate
It is important to match the proper cutter to the material you are engraving. If
you use a cutter sharpened for soft plastics, it will quickly dull when used on a
hard material. Likewise, cutters sharpened for metal usually do not produce as
clean a cut in a softer material.
A general rule is the harder the material, the slower the rpm for the best results.
The factory setting for the Engraver Option is medium (9,000 rpm with 60 Hz
power, 7,500 rpm with 50 Hz power). The setting is suitable for engraving softer
metals such as brass and aluminum, as well as plastics and wood. If you increase
the rpm to the fast setting (11,000 rpm with 60 Hz power, 9,000 rpm with 50 Hz
power) when cutting plastics and wood, you will increase cutting tool life while
still producing good results. Decrease the rpm to the slow setting (7,000 rpm
with 60 Hz power, 5,800 rpm with 50 Hz power) for engraving harder metals
such as steel or stainless steel.
Note: To change the rpm, refer to "Changing the cutter rpm" on page 19.
Summary of Contents for Sabre Engraver Option
Page 1: ...Sabre Engraver Option...
Page 4: ......
Page 5: ......
Page 28: ...Maintaining the Engraver Option 23...
Page 29: ...151 Batson Drive Manchester CT 06040 U S A P63724A Rev A...