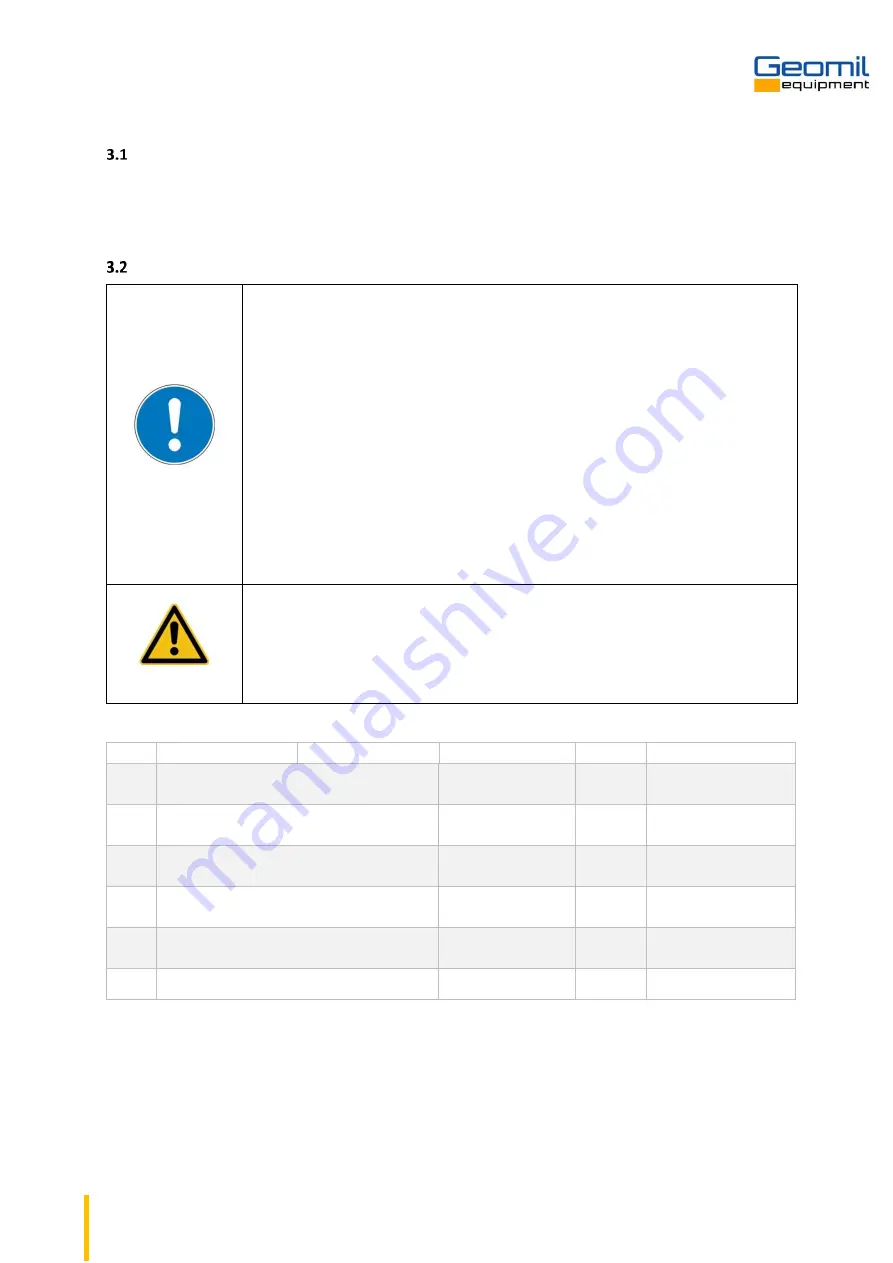
S53-053 Panther
8 of 53
3
Transport
Transport on flatbed truck
It is advised to transport the crawler on a flatbed truck. Make sure to properly secure the crawler during
transport with appropriate lashing means. Only use the 4 lashing points on the far edges of the crawler (SWL =
8 mT)!
Unloading the crawler
Always use the remote control to drive the crawler.
Make sure to keep a safe distance while driving the crawler (at least
1m).
While driving the crawler it is prohibited for any person(s) to be present
in the work cabin.
While unloading the crawler from the transport truck, keep a safe
distance from the truck.
While unloading the crawler from the transport truck, it is prohibited to
be present on the loading deck of the transport truck.
Always place the transport vehicle on an even and steady horizontal surface
before
Loading/unloading the crawler to/from the transport truck.
Step Action
Information
Remark(s)
Fig.
Switch/item
1.
Place the transport on an even and
steady horizontal surface
-
-
2.
Lock the wheels of the transport truck
and lower the ramps
-
-
3.
Prepare the crawler for driving
Refer to chapter
10
-
-
4.
Choose low speed on the remote
control
Refer to chapter
5
-
-
5.
Gently drive the crawler off the
transport truck
Refer to chapter
10
-
-
6.
Clear the transport truck completely
-
-