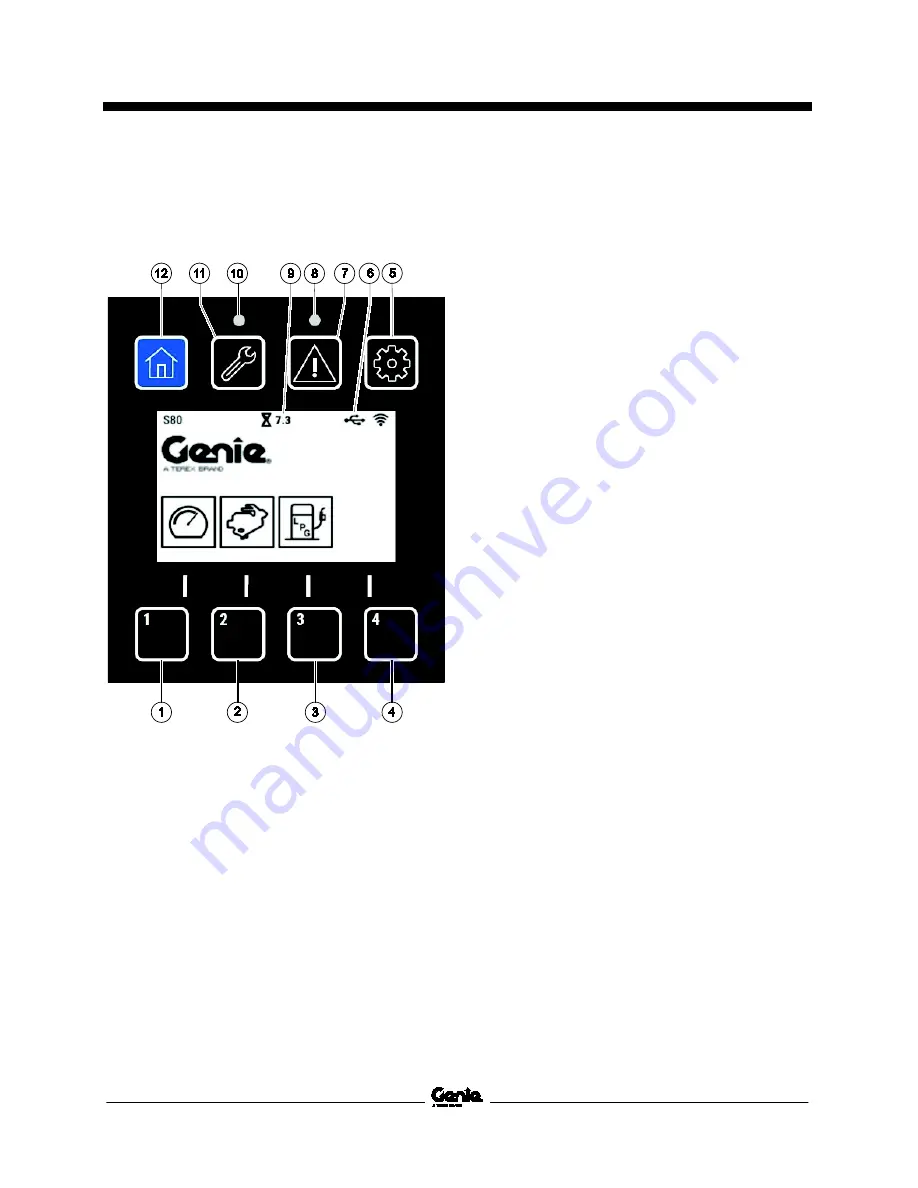
September 2018
Service and Repair Manual
Control System
Part No. 1288652GT
S
®
-60 XC
™
• S
®
-65 XC
™
19
1-2
How to Enter ALC-600 Service
Mode
ALC-600 Control System Display
1 Number 1 or Escape
2 Number 2 or UP arrow
3 Number 3 or DOWN arrow
4 Number 4 or OK
5 Settings menu
6 (not implemented)
7 Faults menu
8 Fault LED Indicator
9 Engine hours
10 Maintenance LED indicator
11 Maintenance menu
12 Home menu
The Control System on this machine allows access
to calibrations through the Service Mode. The
procedures that follow may require the operator to
already be in the Service Mode. The Service Mode
can only be entered at machine start up and
requires a special code.
1
At the ground controls, select the ground
control mode using the key switch.
2
Push and hold buttons numbered
2
and
3
underneath the display screen.
3
Pull out the red Emergency Stop button.
4
You will be prompted for a password. Enter
3 -
3 - 2 - 4
.
5
Press the Gear button to access the settings
menu.
Note: There will be a delay while the menu is being
loaded on the display screen.
6
The machine will now operate normally and
allow the viewing and modification of
calibrations and parameters.
Note: When a parameter is changed in Service
Mode, the change is effective immediately when
button 4 (OK) is pushed. Machine restart is not
required. A confirmation beep accompanies every
save (button 4).
Note: Pushing in the red Emergency Stop button
will exit the Service Mode.
Note: If there has been no input for 10 minutes
while in Service Mode, the ALC-600 will power
down and the Service Mode will be exited, unless
the engine is running.
Summary of Contents for S-65 XC CE
Page 87: ...September 2018 Service and Repair Manual Manifolds Part No 1288652GT S 60 XC S 65 XC 77 ...
Page 89: ...September 2018 Service and Repair Manual Manifolds Part No 1288652GT S 60 XC S 65 XC 79 ...
Page 97: ...September 2018 Service and Repair Manual Manifolds Part No 1288652GT S 60 XC S 65 XC 87 ...
Page 151: ...September 2018 Service and Repair Manual 141 Electrical Schematic TCON ...
Page 154: ...Service and Repair Manual September 2018 144 Electrical Schematic PCON ...
Page 155: ...September 2018 Service and Repair Manual 145 Electrical Schematic Deutz 2 9L Models ...
Page 158: ...Service and Repair Manual September 2018 148 Electrical Schematic Deutz D2011 Models ...
Page 159: ...September 2018 Service and Repair Manual 149 Electrical Schematic Perkins 404F Models ...
Page 162: ...Service and Repair Manual September 2018 152 Electrical Schematic Perkins 404D Models ...
Page 163: ...September 2018 Service and Repair Manual 153 Electrical Schematic Ford MSG425 Models ...
Page 166: ...Service and Repair Manual September 2018 156 Electrical Schematic Generators ...
Page 169: ......