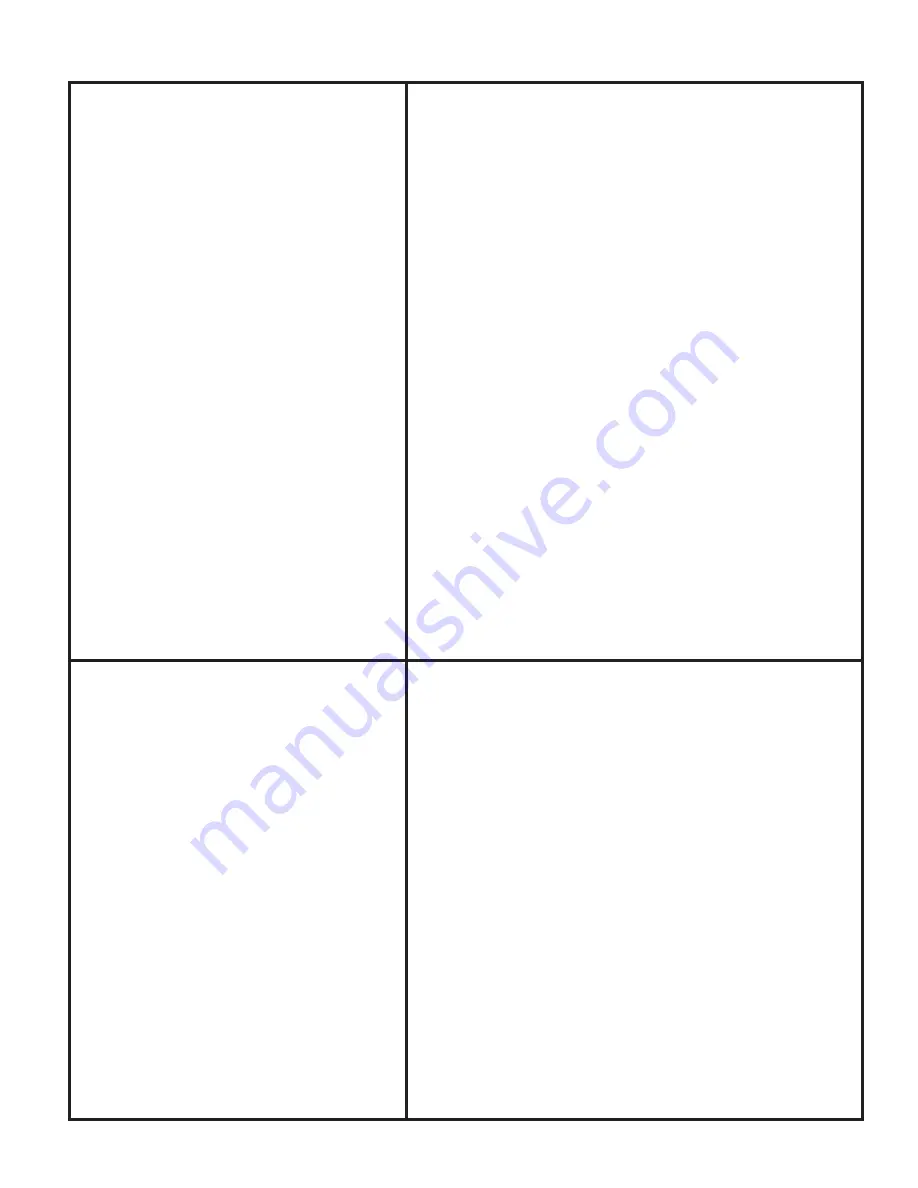
Troubleshooting Guide
5 - 3
Back pressure on a desiccant chamber during
the regeneration cycle. (Chamber’s pressure
gauge indicates above zero (0) PSIG.
Note: The presence of back pressure will result
in insufficient regeneration followed by dew point
degradation. An off-stream chamber’s pressure
gauge MUST indicate zero (0) PSIG throughout
all regeneration cycles.
1.
Purge Adjusting Valve is supplying exces-
sive purge gas to regenerating chamber as
indicated by the Purge Pressure Indicator
(gauge).
Note: If correct setting is unknown, refer to
the Calculation of Purge Pressure Setting
instructions in Appendix A.
2.
Purge or Outlet Check Valve seat is worn,
damaged, or fouled (allowing slight pressure
leakage to enter regenerating chamber).
3.
Off-stream chamber’s Inlet Switching Valve
or on-stream chamber’s Purge Exhaust
Switching Valve seat is worn, damaged or
fouled (allowing slight pressure leakage to
enter regenerating chamber).
Loss of power to Operating Status and Alarm In-
dicators (no illumination). (Both chambers are
at line pressure, as indicated by the left and right
chamber pressure gauges.)
1.
Loss of power supply to (or at) dryer’s elec-
trical disconnect switch, or breaker (cus-
tomer supplied).
2.
Loose connections at customer power con-
nections (H, N, GND).
3.
Control system’s power fuse (F1) is blown.
4.
Damaged components.
1.
SLOWLY rotate Purge Adjusting Valve until correct purge pres-
sure setting is noted on the Purge Pressure Indicator.
Note: The purge pressure setting can only be read and ad-
justed when the off-stream chamber has depressurized for re-
generation. When the off-stream chamber is pressurized the
Purge Pressure Indicator will read system pressure.
2.
Shutdown and Depressurize Dryer. Refer to the Purge and
Outlet Check Valve Maintenance procedure which is applicable
to your specific dryer model. Disassemble, clean and inspect
the Purge and Outlet Check Valves. Replace all worn or dam-
aged components as noted.
3.
Shutdown and Depressurize Dryer. Refer to the Inlet
Switching Valve and Purge Exhaust Switching Valve Mainte-
nance procedures which are applicable to your specific dryer
model. Disassemble, clean and inspect the Inlet Switching
Valves and Purge Exhaust Switching Valves. Replace all worn
or damaged components as noted.
1.
Check power disconnect switch (or breaker) CLOSED. If
tripped breaker or blown fuse is noted, investigate and remedy
cause.
2.
De-energize Dryer Power Supply. Check power supply input
wiring connections (H, N, GND).
3.
De-energize Dryer Power Supply. Replace fuse if blown, in-
vestigate and remedy cause.
4.
For damaged solid state components and/or circuit boards of
microprocessor units, contact your local General Pneumatics
Sales Representative for assistance.
PROBLEM/POSSIBLE CAUSE
CHECKS AND REMEDY