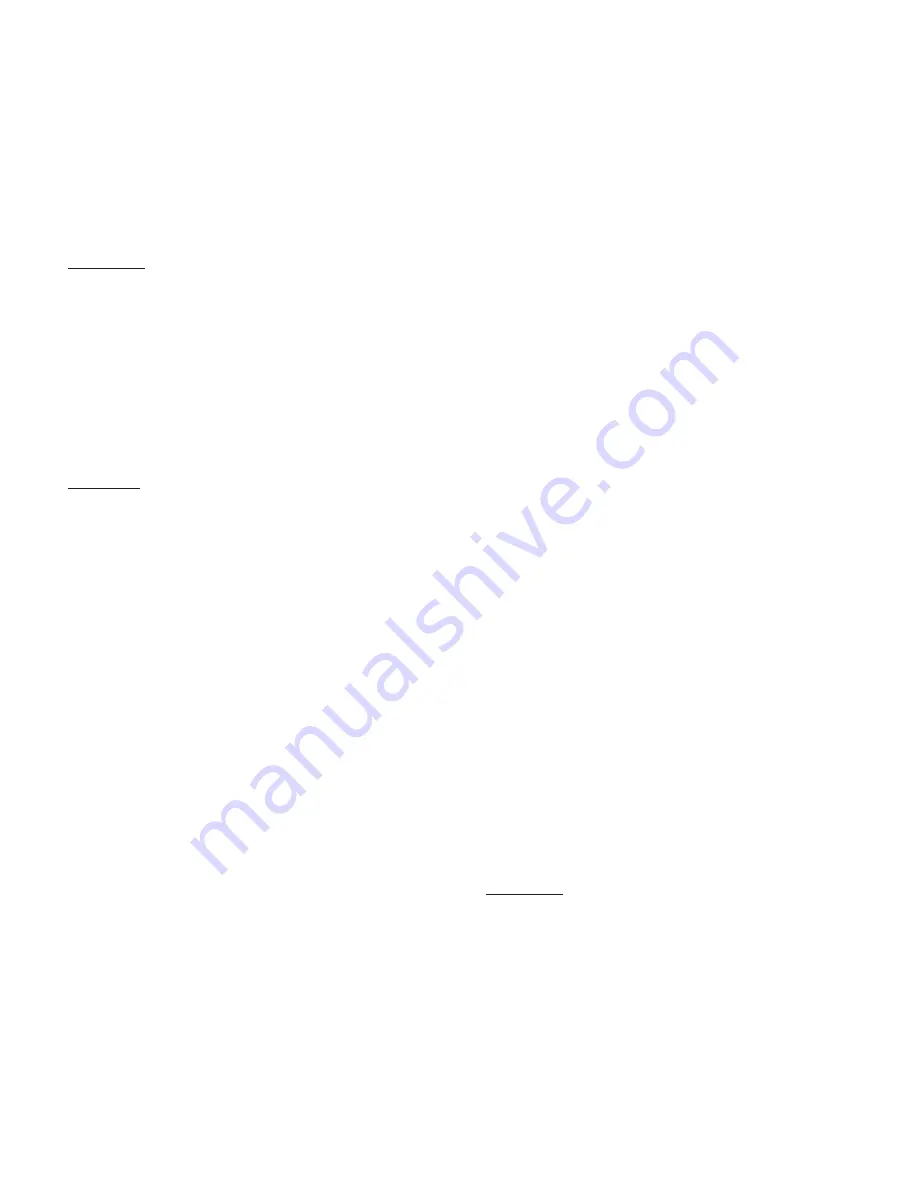
Installation
2 - 5
CAUTION: Do not make any additional wiring connections
to terminals H, N, or GND on the POWER INPUT.
CAUTION: Do not remove the factory programmed micro-
computer chip or any I.C. chip from the logic control circuit
board. Improper removal will cause irreparable damage to
these highly static-sensitive components. Damage to
these components will render the dryer control system in-
operative until replacement is accomplished by a General
Pneumatics Field Service Engineer. Do not remove the
program identification sticker from the microcomputer chip.
WARNING!
DIP switches within the control box have been preset
at the factory to conform to customer operating condi-
tions. Any tampering with DIP switches will void war-
ranty and may reduce the quality of the product gas.
Any adjustments of DIP switches should only be made
by a qualified General Pneumatics Field Service Engi-
neer.
2.8
Remote Alarm Connection
WARNING!
Most standard air and gas dryers are furnished with
contacts for remote alarms. These contacts should be
wired to an audible alarm and/or to an area where they
are continuously monitored. When these contacts are
not used, the dryer must be visually checked every
two (2) hours for existence of any possible malfunc-
tion. Failure to do so may result in an upset condition
that could damage the equipment. Failure to protect
the dryer from aerosols and liquid condensate will
void warranties.
1.
Remote alarm terminals (A1, A2, A3) located on the
Remote Alarm Terminal Block are provided for con-
nection of a customer-supplied remote alarm circuit
(if desired). Should an alarm situation or loss of the
dryer’s power supply occur, the remote alarm relay
will de-energize to transfer contact from A3 to A2 for
remote alarm actuation.
Note: A customer supplied separate power source of
sufficient voltage, (not to exceed 120 VAC) must be
connected to terminal A1 for remote alarm actuation.
CAUTION: The total current rating of all customer
supplied remote alarm equipment MUST NOT ex-
ceed 6 amperes inductive, and 10 amperes resistive.
Do not make any additional wiring connections to ter-
minals A1, A2, and A3.
2.9
Equipment Check
1.
Vibration during shipment can cause loosening of fit-
tings and fasteners. Therefore, inspect the dryer for
alignment, connection and tightness of all subassem-
blies, etc.
2.
Remove shipping plugs from desiccant chamber fill
ports (2). Apply TFE tape to threads and install relief
valves (2).
Note: Pressure relief valves are offered as accesso-
ries and are shipped separately.
3.
On Models OP15 through OP300 desiccant is nor-
mally installed prior to shipment unless otherwise
specified by the customer. On Models OP400 and
OP500 desiccant is shipped loose.
Tapping on each chamber with a soft-face mallet will
yield a deadened sound if desiccant has been in-
stalled. If a hollow sound is noted, the chambers are
empty and require installation of desiccant prior to
operation. Refer to the Desiccant Charging Proce-
dure in the Maintenance and Repair section of this
manual, if charging is necessary.
CAUTION: Dryer models covered within the scope of
this manual are designed to use a specific desiccant.
Use of any other size or type may reduce efficiency or
damage the dryer.
CAUTION: Do not hydrostatically test the dryer
with desiccant installed. All pressure vessels are
factory tested at one and one-half (1-1/2) times the
design pressure. Hydrostatic testing will damage the
dryer's desiccant charge.
4.
While exercising caution for Static Sensitive Devices,
open the Dryer Control System Enclosure Cover and
inspect as follows:
a) Check all terminal block wiring connections. Do
not over tighten terminal block lug screws.
b) Close the dryer control system enclosure cover
and tighten all cover latches.
CAUTION: Do not remove the factory programmed micro-
computer chip or any I.C. chip from the logic control circuit
board. Improper removal will cause irreparable damage to
these highly static-sensitive components. Damage to
these components will render the dryer control system in-
operative until replacement is accomplished by a General
Pneumatics Field Service Engineer. Do not remove the
program identification sticker from the microcomputer chip.
WARNING!
DIP switches within the control box have been preset
at the factory to conform to customer operating condi-
tions. Any tampering with DIP switches will void war-
ranty and may reduce the quality of the product gas.
Any adjustments of DIP switches should only be made
by a qualified General Pneumatics Field Service Engi-
neer.