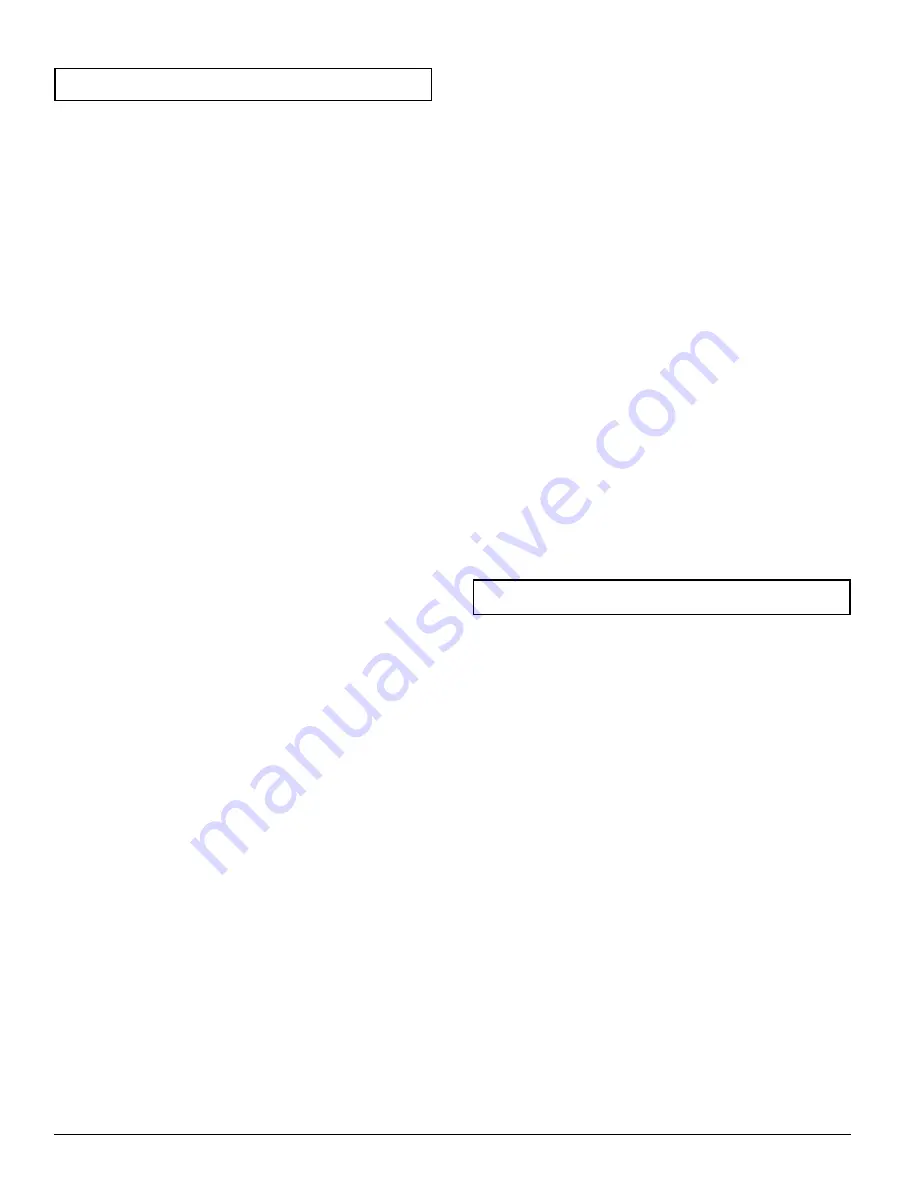
PRINTED IN U.S.A.
2-2
90
8147
/0999
•
When driving on or across roads, the machine must be
equipped according to the road/traffic laws, and these
laws must be observed.
•
Adapt working speed to local visibility.
•
The driving speed must be adapted to the road and
ground conditions.
•
Particular attention is required when working on slopes.
Angle of inclination of machine for all directions of trav-
el: for brief operation (2-3 minutes)–maximum of 30°;
for continuous operation–maximum of 25°.
•
Unauthorized personnel must not start-up the machine.
•
No one but the operator must be on the machine when in
use. PASSENGERS PROHIBITED!
•
Use the towing bracket provided for towing the machine.
•
The operating area, steps, and grips must be free of oil,
dirt, ice and unsecured objects.
•
The proper working condition of the lighting system
must be checked before and while working in darkness.
•
Always keep the windshield and windows clean. Poor
visibility can cause accidents.
•
Operate the machine from the operator’s seat only. Wear
seatbelt which is provided.
•
Control the machine cautiously and gradually until you
are fully familiar with all the controls and handling.
•
Pay attention to all movements of machines and
machines in the working area.
•
Personnel must not be in the working area. Never oper-
ate equipment above people.
•
Always wear appropriate protective clothing: hard hat,
work gloves, strong work shoes, reflective clothing.
•
Make sure you have sufficient knowledge of the working
area; location of utility lines (water, gas, electric, etc.)
and load bearing capacity of the ground.
•
Before working in the area of utility lines, contact the
proper authority to determine the measures required for
safety.
•
Never dig underneath the machine. Support walls prop-
erly when excavating or working in, or close to, trench-
es.
•
Never drive long distances with the working equipment
fully raised. Lowering the working equipment produces
improved visibility and improved weight distribution.
Safety Reminders (continued)
•
Never drive across the incline on sloping ground.
Extreme caution is required when working across an
incline or changing direction.
•
Never use the weight of the machine to obtain more
force when excavating. There is a risk overturning.
•
Before starting up the machine or setting it in motion,
warn any personnel in the area.
•
Attach a clearly visible, legible OUT OF SERVICE sign
when repair and adjustments are being performed on the
machine.
•
Unless necessary for servicing the engine, the engine
hood must not be opened while the engine is running.
•
Be familiar with the machine safety devices.
•
The machine is not to be used to lift equipment or trans-
port personnel.
•
The excavator arm is not a ramming tool. Never attempt
to use the working equipment to drive piles or similar
items into the ground, or to flatten the ground.
•
Never excavate while the machine is travelling. Never
move the machine to dig. Never slew with lowered
working equipment and never move the machine when
the working equipment is resting on the ground.
The machine has several components that operate at high
temperature under normal operating conditions, primarily the
engine and exhaust systems. Also, the electrical system, if
not properly maintained or is damaged, can arc or produce
sparks. These conditions make it extremely important to
avoid conditions where explosive dust or gasses can be ignit-
ed by arcs, sparks or heat.
The machine must be cleaned on a regular basis to avoid the
buildup of flammable debris such as leaves, straw, etc.
Accumulated debris, particularly in the engine compartment,
poses a fire hazard.
The spark arrestor muffler is designed to control the emission
of hot particles from the engine and exhaust system, but the
muffler system still gets hot during operation. For this rea-
son, it is extremely important not to operate the machine in
an area where explosive dust or gasses can contact the hot
exhaust.
•
Do not use the machine where explosive gasses or dust
can be ignited by arcs, sparks, hot components or
exhaust gasses.
•
The operator cab, engine compartment and engine cool-
ing system must be inspected every day and cleaned if
necessary to remove any flammable debris.
Fire Prevention
Summary of Contents for GE 802
Page 1: ...GE 802 Crawler Excavator OPERATOR S MANUAL Form No 908147 English...
Page 12: ...PRINTED IN U S A 1 8 908147 0999 This Page Intentionally Blank...
Page 45: ...PRINTED IN U S A 4 15 908147 0999 MAINTENANCE LOG DATE HOURS SERVICE PROCEDURE...
Page 46: ...PRINTED IN U S A 4 16 908147 0999 MAINTENANCE LOG DATE HOURS SERVICE PROCEDURE...
Page 50: ...PRINTED IN U S A 5 4 908147 0999 NOTES...
Page 51: ......