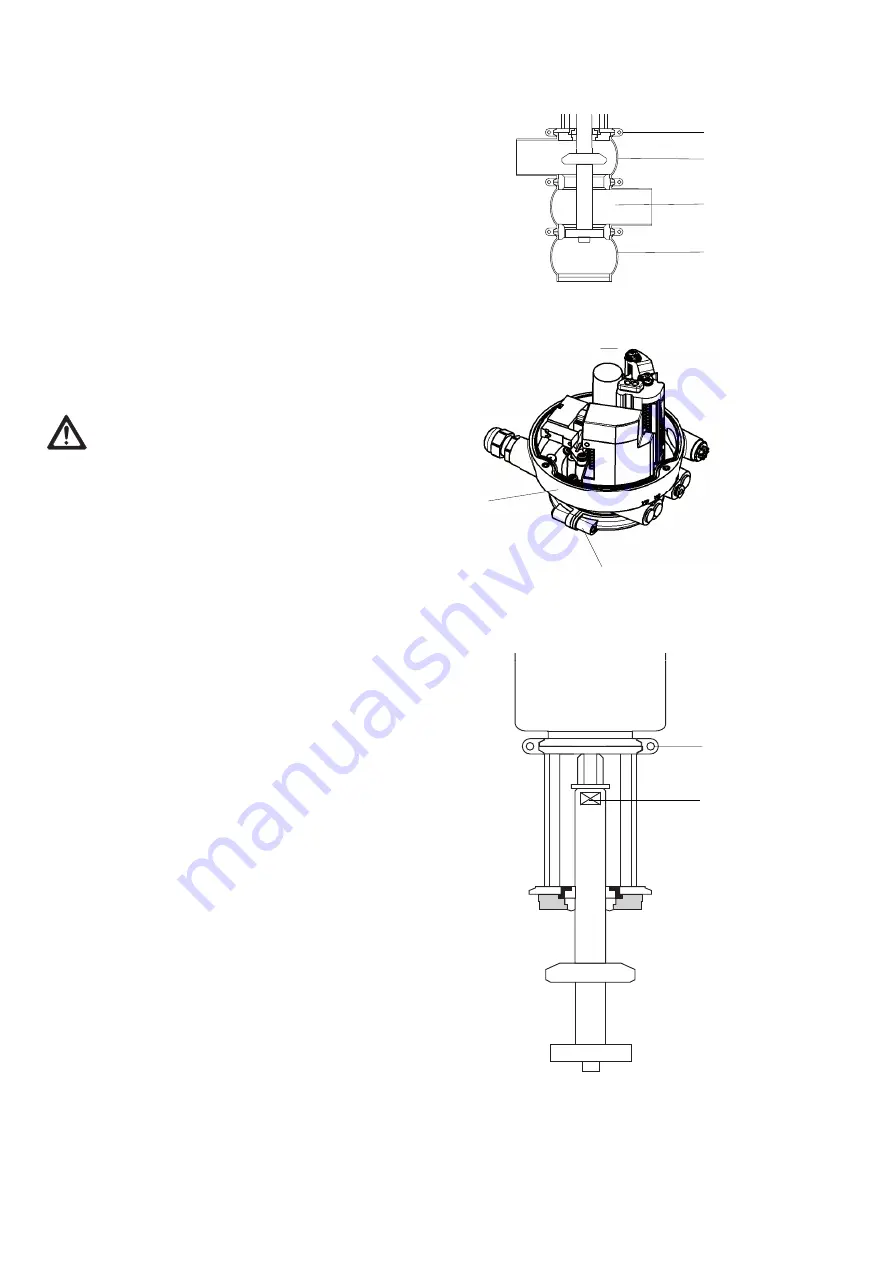
14
2014-10 · Flow Diversion Device with Proximity switch
Disassembly the control module
• Remove the hinged clamps (1).
Lower the valve disk :
• Depressurize the actuator.
✗
The pneumatic and electrical connections can remain
connected to the control module.
• Remove the hinged clamps (5) between the control
module and the actuator.
• Lift the control module (6) upwards.
Disassembly the valve insert
CAUTION
When pulling out the valve do not damage the valve
seat.
Do not set the valve insert down on the valve disk, as
this can damage the valve disk, but lay it down
carefully.
•Pull the valve out of the housing (2, 3, 4).
Loosen the valve disk
• Slacken the hinged clamps (7) between the actuator
and the lantern.
• Grip the valve disk at the key face (8) with an open-
end spanner, turn the actuator 3 turns using a strap
wrench. The valve disk will come loose.
1
2
3
4
8
7
5
6