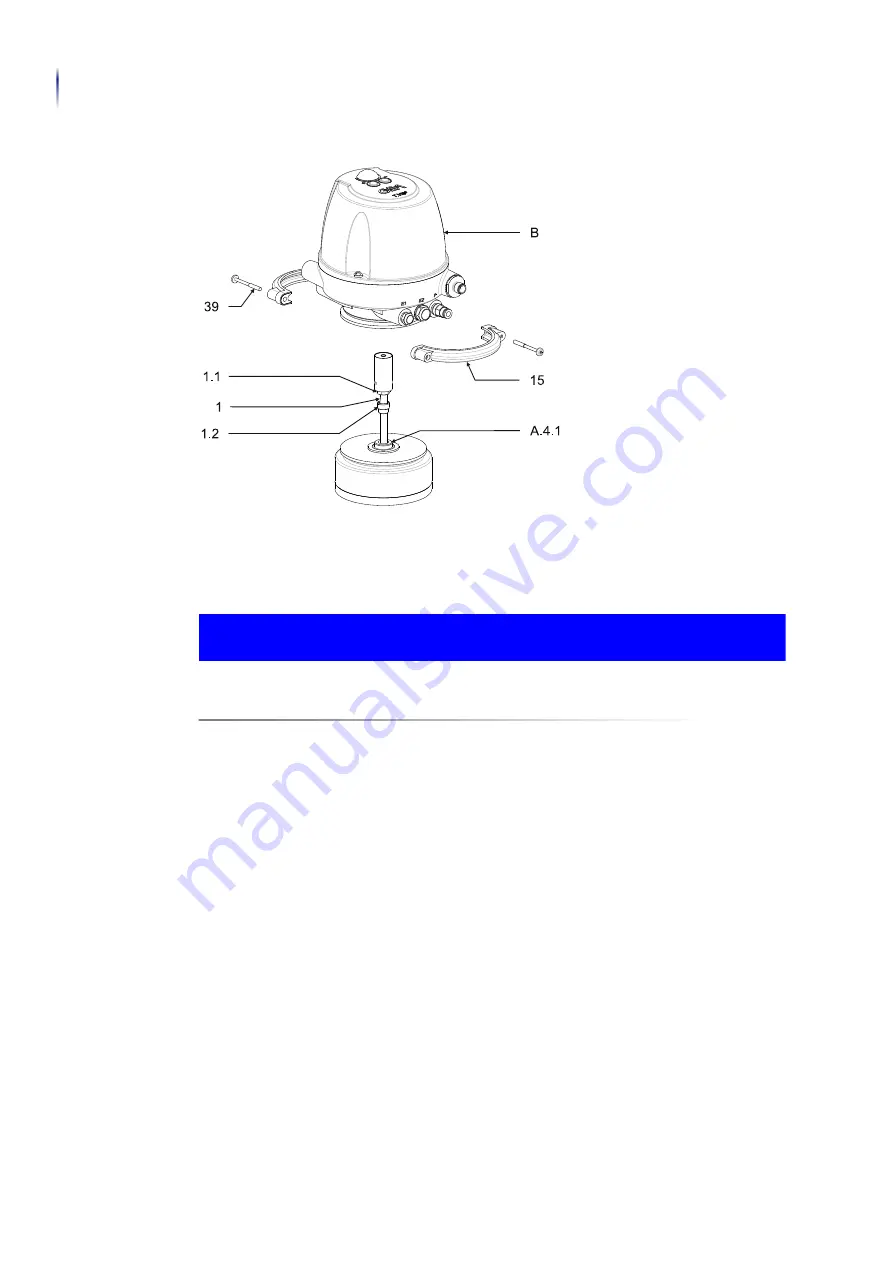
Maintenance
Disassembling
5
6
Removing the Control Top and the Switch Bar
Requirement
No solenoid valve must be actuated electrically or manually.
The pneumatic and electrical connections on the plant side can remain on the
control top.
IMPORTANT NOTE
The permanent magnet on the switch bar (1) is fragile.
Damage to the permanent magnet.
Protect the permanent magnet against impact stress.
Carry out the following steps:
1.
Undo the screws (39).
2.
Remove the semi-annular clamps (15) at the control top (B).
3.
Remove the pneumatic connections at the lifting actuator.
4.
Pull the control top (B) upwards to remove.
The feedback signal to the higher-level control system is interrupted.
The green LED goes out and the red LED lights up.
5.
Unscrew the switch bar (1) by using an open spanner, size 13 at (1.1).
6.
Pull out the switch bar (1) from the piston rod.
7.
Only if you use the screwed-in eye bolt for transportation, see “Installation“
(Page 14):
Unscrew the sliding piece (1.2) from the piston rod (A 4.1) of the actuator (A.4).
Done
Operating Instructions · VARIVENT
®
Mixproof Valve M-C/2.0
Edition 2018-10-04