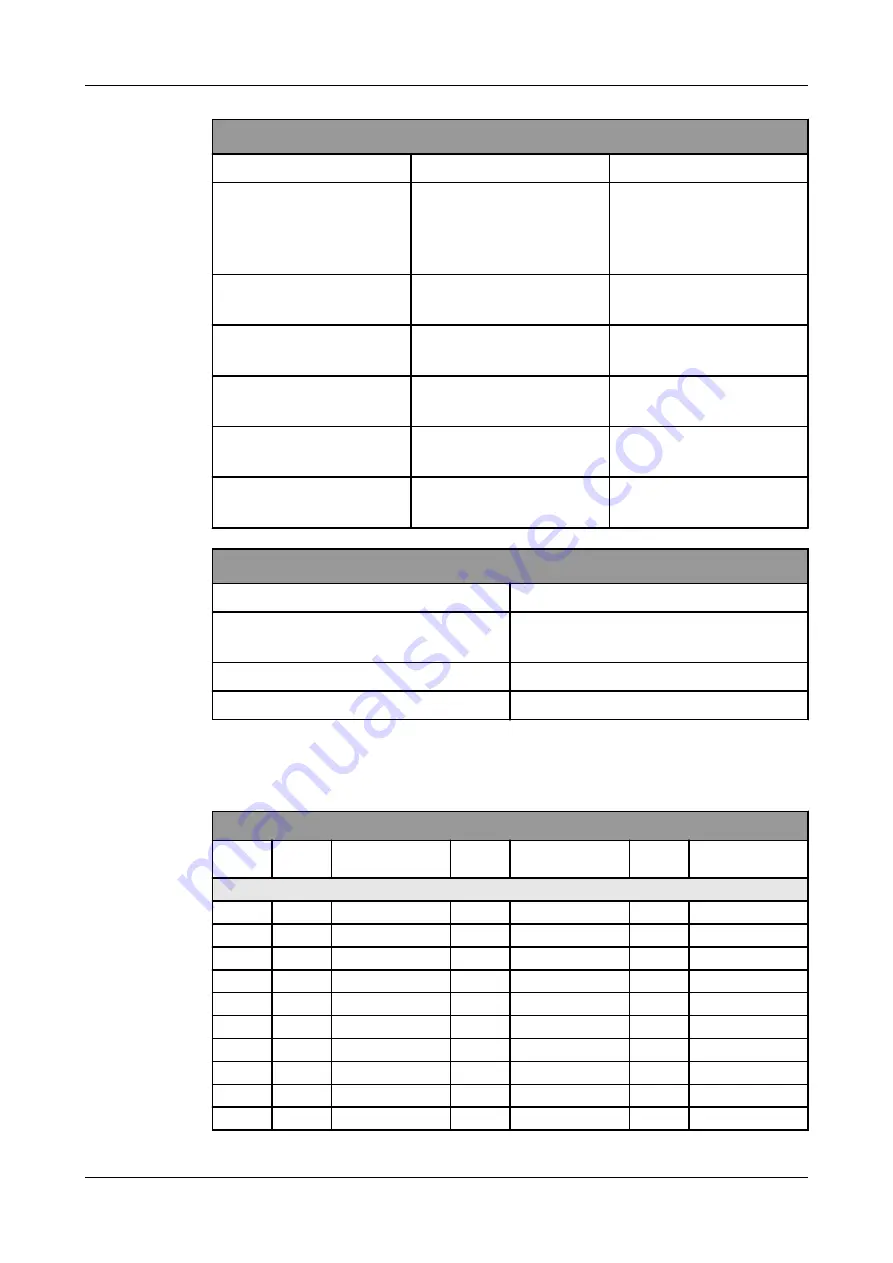
Technical data: outputs as seen from the IO-Link
Bit
Function
Signal
DO2
PV Y3
Activation of solenoid
valve Y3
1 = solenoid valve
activated
0 = solenoid valve not
activated
DO3
X4
not assigned
DO4
X5
not assigned
DO5
X6
not assigned
DO6
X7
not assigned
DO7
HAS
Activation of setup
1= activate setup
Technical data: electrical specifications
Designation
Description
IO-Link version
V1.1
Port class A / COM2
Reverse voltage protection
yes
SIO mode
not supported
You can download the IODD from the following link:
https://ioddfinder.io-link.com/productvariants/search?vendorName=%22GEA
%20Tuchenhagen%20GmbH%22
Technical data: non-cyclical data exchange
Sub-
index
Offset
Function
Access
rights
Range
Default
Signal
Index 0x00 - Identification
0x01
0x00
Master Command
M
0x00 - 0xFF
0x00
0x02
0x01
Master Cycle Time
R/W
0x00 - 0xFF
0x1E
0x03
0x02
Min Cycle Time
M
0x00 - 0xFF
0x1E
0x04
0x03
M-Sequence
M
0x00 - 0xFF
0x08
0x05
0x04
Revision ID
R/W
0x00 - 0xFF
0x11
0x06
0x05
Process Data In
M
0x00 - 0xFF
0x83
0x07
0x06
Process Data Out
M
0x00 - 0xFF
0x08
0x08
0x07
Vendor ID 1
M
0x00 - 0xFF
0x05
0x09
0x08
Vendor ID 2
M
0x00 - 0xFF
0x2C
0x0A
0x09
Device ID 1
R/W
0x00 - 0xFF
0x12
Technical data
IO-Link specifications
430BAL010699EN_6
17.03.2022
31
Summary of Contents for T.VIS A-15
Page 6: ...430BAL010699EN_6 6 17 03 2022...
Page 116: ......