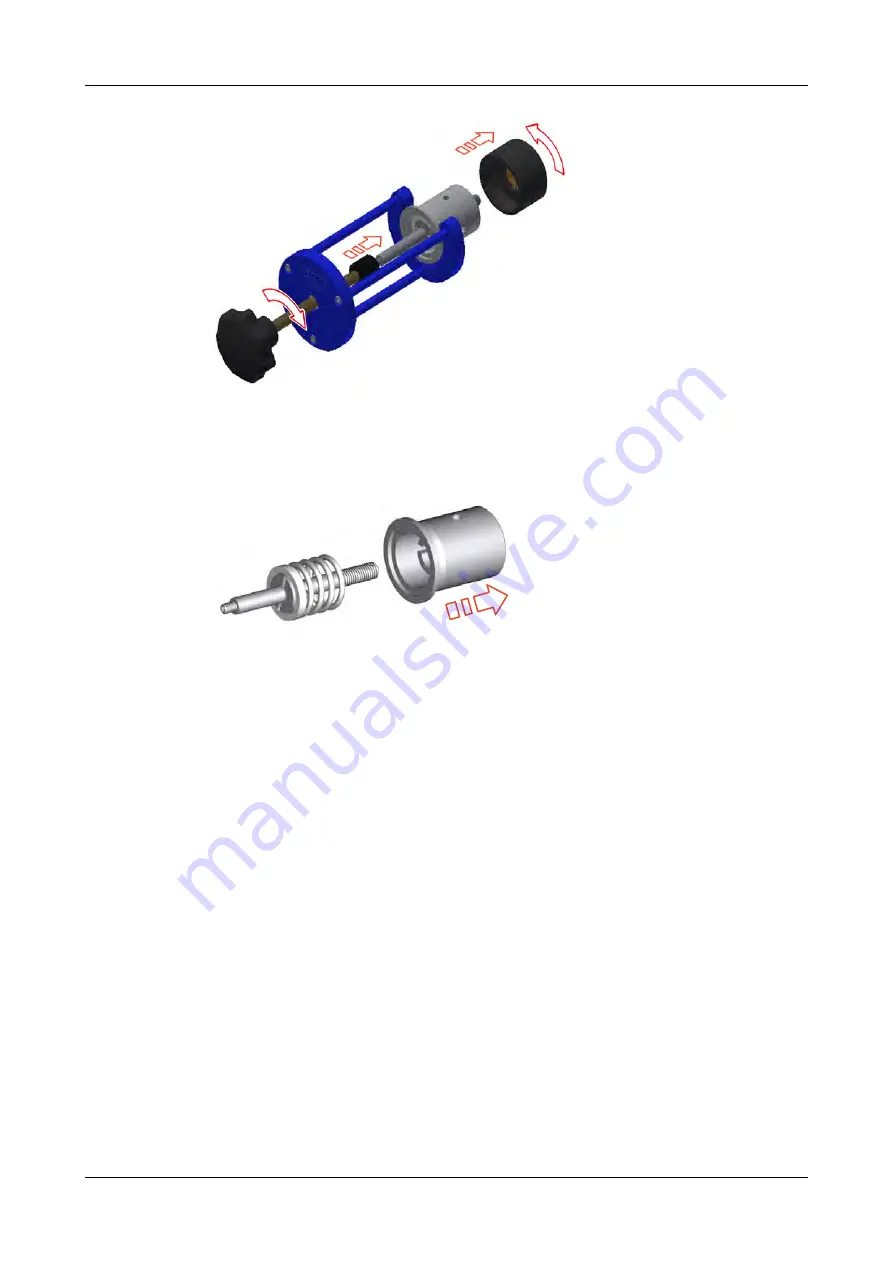
Fig.39:
Remove the hand wheel
4.
Slowly release the pressure on the actuator spring and remove the drive from
the assembly tool.
5.
Carefully pull the actuator cylinder off the actuator components.
Fig.40:
Pulling off the actuator cylinder
6.
Carefully pull the actuator components off the piston rod.
Maintenance
Disassembling and assembling actuator PA35 PV H
430BAL013317EN_1
50
11.03.2019
Summary of Contents for Aseptomag AMV
Page 60: ......