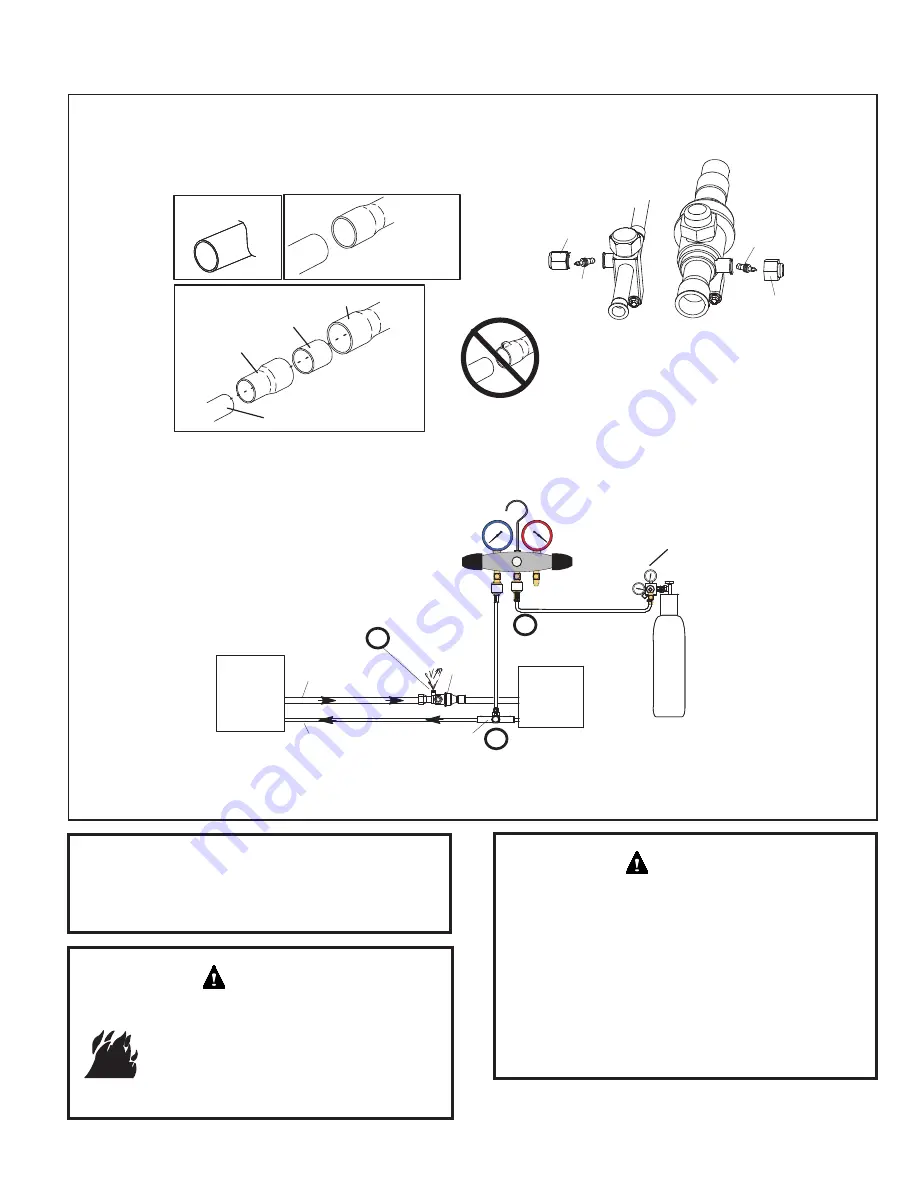
508133G01 / 31-5000715
Page 9 of 25
Issue 2140
ATTACH THE MANIFOLD GAUGE SET FOR BRAZING LIQUID AND VAPOR LINE SERVICE VALVES
OUTDOOR
UNIT
LIQUID LINE
VAPOR LINE
LIQUID LINE SERVICE
VALVE
VAPOR LINE
SERVICE
VALVE
ATTACH
GAUGES
INDOOR
UNIT
VAPOR SERVICE PORT MUST BE OPEN
TO ALLOW EXIT POINT FOR NITROGEN
A -
Connect gauge set low pressure side to
liquid line service valve (service port).
B -
Connect gauge set center port to bottle of
nitrogen with regulator.
C -
Remove core from valve in vapor line
service port to allow nitrogen to escape.
NITROGEN
HIGH
LOW
USE REGULATOR TO FLOW
NITROGEN AT 1 TO 2 PSIG.
B
A
C
WHEN BRAZING LINE SET TO
SERVICE VALVES, POINT FLAME
AWAY FROM SERVICE VALVE.
Flow regulated nitrogen (at 1 to 2 psig) through the low-side refrigeration gauge set into the liquid line service port valve, and out of the
vapor line service port valve.
CUT AND DEBUR
CAP AND CORE REMOVAL
Cut ends of the refrigerant lines square (free from nicks or dents)
and debur the ends. The pipe must remain round. Do not crimp end
of the line.
Remove service cap and core from
both the vapor and liquid line service
ports.
1
2
LIQUID LINE SERVICE
VALVE
SERVICE
PORT
CORE
SERVICE PORT
CAP
SERVICE
PORT
CORE
SERVICE
PORT CAP
CUT AND DEBUR
LINE SET SIZE MATCHES
SERVICE VALVE CONNECTION
DO NOT CRIMP SERVICE VALVE
CONNECTOR WHEN PIPE IS
SMALLER THAN CONNECTION
3
VAPOR LINE SERVICE
VALVE
COPPER TUBE
STUB
REFRIGERANT LINE
REDUCER
SERVICE VALVE
CONNECTION
LINE SET SIZE IS SMALLER
THAN CONNECTION
Refrigerant Piping - Brazing Procedures
Before brazing, ensure the system is fully
recovered of all refrigerant. Application of a
brazing torch to a pressurized system may
result in ignition of the refrigerant and oil
mixture. Check the high and low pressures
before applying heat.
WARNING
Brazing alloys and flux contain materials which are
hazardous to your health.
Avoid breathing vapors or fumes from brazing
operations. Perform operations only in well-ventilated
areas.
Wear gloves and protective goggles or face shield to
protect against burns.
Wash hands with soap and water after handling brazing
alloys and flux.
WARNING
Use a manifold gauge set designed for use on R-410A
refrigerant systems.
NOTE