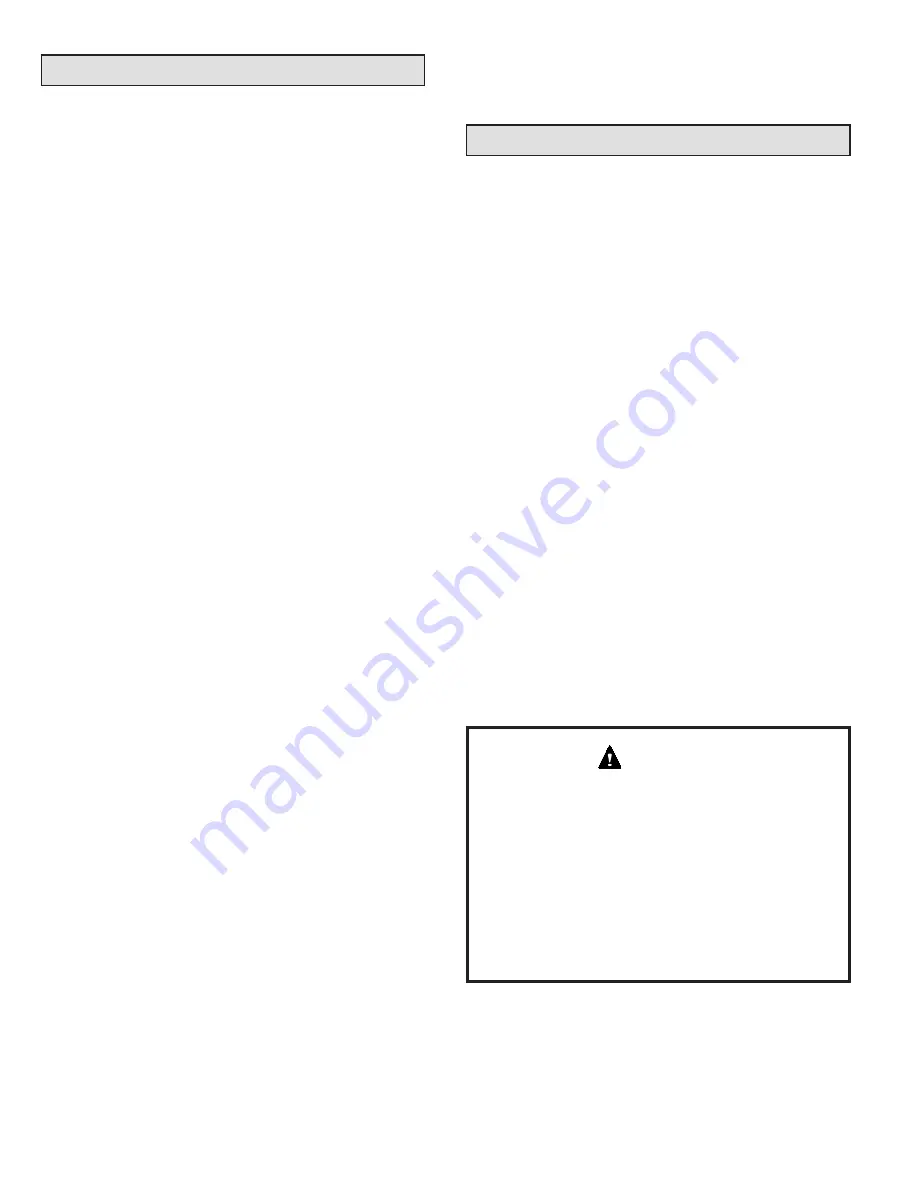
Page 2 of 25
508133G01 / 31-5000715
Issue 2140
General
Read this entire instruction manual, as well as the
instructions supplied in separate equipment, before
starting the installation. Observe and follow all warnings,
cautions, instructional labels, and tags. Failure to comply
with these instructions could result in an unsafe condition
and/or premature component failure.
These instructions are intended as a general guide only
for use by qualified personnel and do not supersede any
national or local codes in any way. The installation must
comply with all provincial, state, and local codes as well as
the National Electrical Code (U.S.) or Canadian Electrical
Code (Canada). Compliance should be determined prior
to installation.
This unit uses R-410A, which is an ozone-friendly HFC
refrigerant. The unit must be installed with a matching
indoor coil and line set. A filter drier approved for use with
R-410A is installed in the unit.
IMPORTANT
:
This product has been designed and
manufactured to meet ENERGY STAR criteria for energy
efficiency when matched with appropriate coil components.
However, proper refrigerant charge and proper air flow
are critical to achieve rated capacity and efficiency.
Installation of this product should follow the manufacturer’s
refrigerant charging and air flow instructions.
Failure to
confirm proper charge and airflow may reduce energy
efficiency and shorten equipment life.
Inspection of Shipment
Upon receipt of equipment, carefully inspect it for possible
shipping damage. If damage is found, it should be noted
on the carrier’s freight bill. Take special care to examine
the unit inside the carton if the carton is damaged. Any
concealed damage discovered should be reported to the
last carrier immediately, preferably in writing, and should
include a request for inspection by the carrier’s agent.
If any damages are discovered and reported to the carrier
DO NOT INSTALL THE UNIT
, as claim may be denied.
Check the unit rating plate to confirm specifications are as
ordered.
Safety Precautions
Follow all safety codes. Wear safety glasses and work
gloves. Use quenching cloth for brazing operations.
Have fire extinguisher available. Read these instructions
thoroughly and follow all warning or cautions attached to
the unit.
1. Always wear proper personal protection equipment.
2. Always disconnect electrical power before removing
panel or servicing equipment.
3. Keep hands and clothing away from moving parts.
4. Handle refrigerant with caution; refer to proper MSDS
from refrigerant supplier.
5. Use care when lifting, avoid contact with sharp edges.
Installation
NOTE:
In some cases, noise in the living area has been
traced to gas pulsations from improper installation of
equipment.
• Locate unit away from windows, patios, decks, etc.
where unit operation sounds may disturb customer.
• Leave some slack between structure and unit to
absorb vibration.
• Place a sound-absorbing material, such as Isomode,
under the unit if it will be installed in a location or
position that will transmit sound or vibration to the
living area or adjacent buildings.
• Install the unit high enough above the ground or roof to
allow adequate drainage of defrost water and prevent
ice buildup.
• In heavy snow areas, do not locate the unit where
drifting snow will occur. The unit base should be
elevated above the depth of average snows.
NOTE:
Elevation of the unit may be accomplished
by constructing a frame using suitable materials. If a
support frame is constructed, it must not block drain
holes in unit base.
• When installed in areas where low ambient
temperatures exist, locate unit so winter prevailing
winds do not blow directly into outdoor coil.
• Locate unit away from overhanging roof lines which
would allow water or ice to drop on, or in front of, coil
or into unit.
To prevent personal injury, as well as damage to panels,
unit or structure, observe the following:
While installing or servicing this unit, carefully stow all
removed panels so that the panels will not cause injury
to personnel, objects or nearby structures. Also, take
care to store panels where they will not be subject to
damage (e.g., being bent or scratched).
While handling or stowing the panels, consider any
weather conditions (especially wind) that may cause
panels to be blown around and damaged.
WARNING