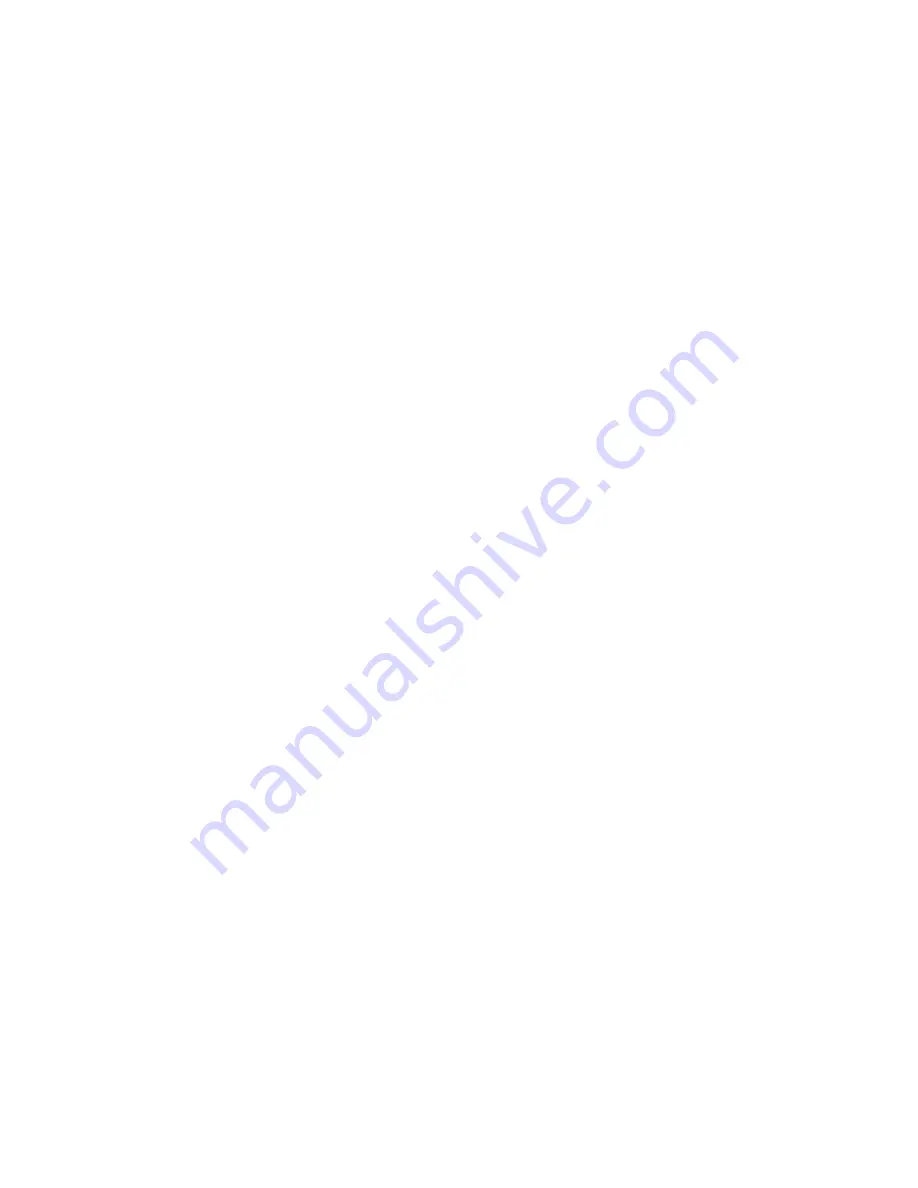
17
PLUGGING
- Slow down is accomplished when reversing by providing a small amount of retarding
torque for deceleration. If the vehicle is moving and the directional lever is moved from one direction
to the other, the motor field is reversed. The plug signal is initiated by the fact that the directional
switch has moved from one direction to the other. The motor armature, driven by the inertia of the
vehicle, acts as generator. This generated current passes through 4REC and the sensor. The oscilla-
tor circuit regulates at a plug current limit level as set by the Handset this controls the pulse rate of
lREC to regulate the generated motor current and bring the truck to a smooth stop and reversal. With
the accelerator potentiometer at minimum resistance, function 5 will enable adjustment of plugging
current from max to min. current level for plug current limit.
PEDAL POSITION PLUG
- This feature will allow for plugging distance based on pedal position.
Pedal position will reduce the plugging current to the current value set by this function as the accel-
erator is returned to the creep speed position. Maximum plug current is obtained with the accelerator
in the top speed position. This feature is adjustable by using function 16 on the handset.
RAMP START
- This feature provides full SCR torque to restart a vehicle on an incline. The
memory for this function is the directional switch. When stopping on an incline, the directional
switch must be left in its original or neutral position to allow the control to assure full power when
restarted. The accelerator potentiometer input will modulate ramp start current.
FULL POWER TRANSITION
- this built-in feature provides smooth transition from SCR to lA
bypass. This is accomplished by the SCR continuing to pulse until the lA contactor power tips close.
CONTROL ACCELERATION AND 1A TIME
- This feature allows for adjustment of the rate of
time it takes for the control to accelerate to 96% applied battery voltage to the motor on hard accel-
eration. The 1A contactor will automatically close .2 seconds after the controlled acceleration stops
and the accelerator input is less than .5 volts or less than 50 ohms. C/A is adjusted by function 3 from
.1 to 22 seconds.
1A CURRENT DROP OUT
- This adjustable feature can be set to open the 1A contactor if the
traction motor is subject to excessive currents. The dropout is adjustable with function 6 of the
handset. Once the control has dropped out the 1A contactor due to excess current, the directional or
accelerator switch must be returned to neutral to unlock the dropout circuit to allow the control to
pick up the 1A contactor again. Using this feature will reduce the 1A contactor tip life, thus it should
be used only where needed to protect the motor.
STATIC RETURN TO OFF
- This built-in feature of the control is set up to make the driver return
the directional lever to neutral anytime he leaves the vehicle and returns. If the seat switch or key
switch is opened, the control will shut off and cannot be restarted until directional lever is returned to
neutral. A time delay of approximately .75 seconds is built into the seat switch input to allow mo-
mentary opening of the seat switch if a bump is encountered.
ACCELERATOR VOLTS HOLD-OFF
This feature checks the voltage level at the accelerator
input when ever the key switch or seat switch is activated. If the voltage is less than 2.5 volts the
control will not start. This is to assure that the control is calling for low speed operation at start-up.
Summary of Contents for EV100 LX
Page 3: ...3 EV100LX COMPONENT LOCATIONS ...
Page 4: ...4 EV100LX OUTLINE DRAWING ...
Page 5: ...5 EV100LX WITH SPEED LIMIT AND FW 9 ...
Page 6: ...6 EV100LX WITH REGEN AND FW 9 ...
Page 7: ...7 EV100LX DUAL MOTOR CONTROL 9 ...
Page 8: ...8 EV100LX PUMP CONTROL 9 ...
Page 10: ...10 EV100LX PART NUMBER IDENTIFICATION ...
Page 60: ...6 0 ...
Page 80: ...g GE Industrial Systems EV200LX SUPPLEMENT Page 4 of 5 REV 11 2002 Wiring Diagram ...