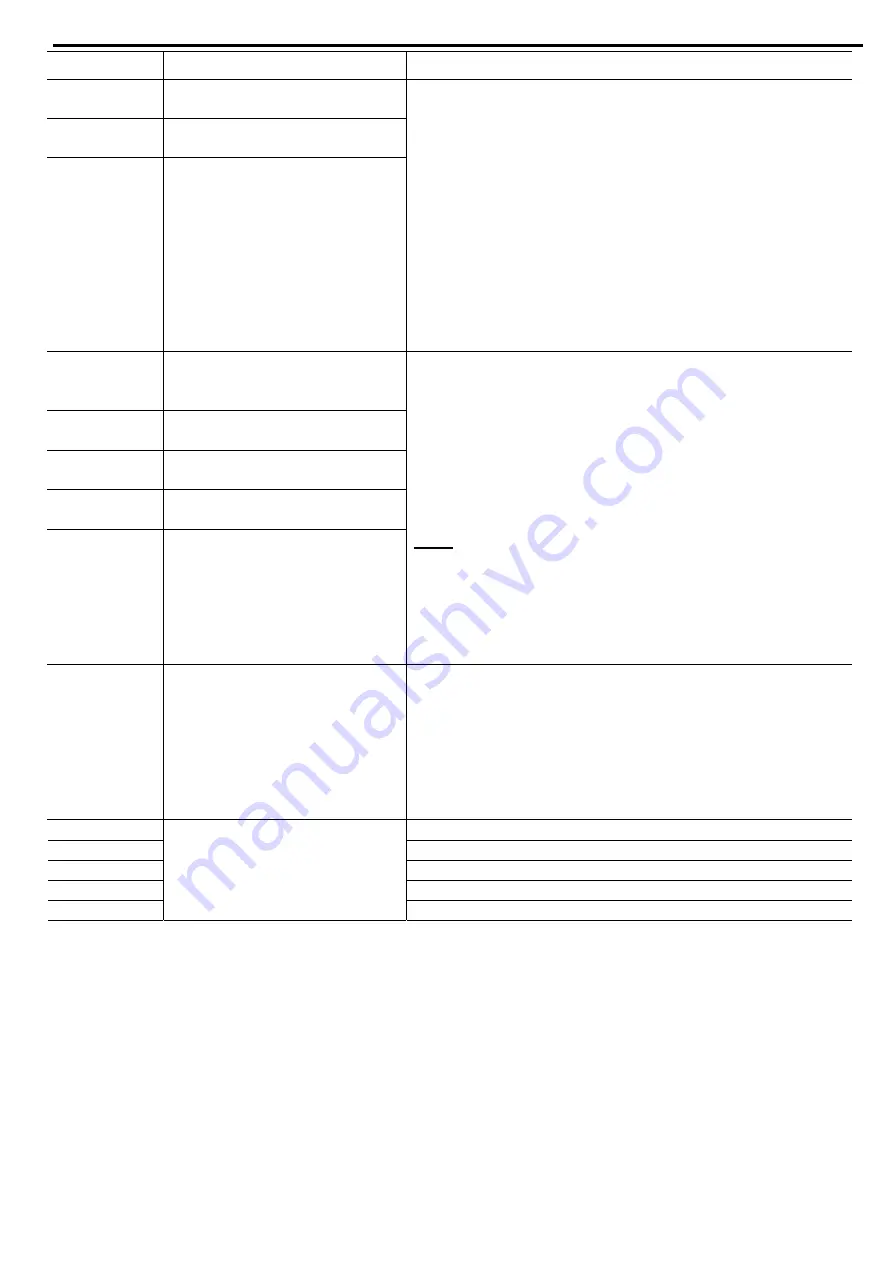
16
• Technical Specifications
Terminal Function
Description
Terminal SG
No connection
•
Standard RS485, half duplex with Modbus protocol, baud
rate 1200, 2400, 4800, 9600 BPS.
Terminal D-
RS-485 communication (-)
•
Twisted shielded pair should be used.
Connect shield to ground on the PLC/Computer side.
Terminal D+
RS-485 communication (+)
•
Terminals 4 & 5 must be wired to Control Supply for
operation in communication mode (refer to section
page 70 for wiring diagram).
•
Up 32 units can be connected for Modbus RS485
communication. For reliable communication, units should
be installed in the vicinity of 200m maximum, from the first
to the last unit.
•
Refer to section
4.7.9 page 42 for programming.
•
Refer to Appendix A of this manual for Modbus protocol
manual.
Terminal 28
Thermistor input (T1)
Thermistor input is programmable as a PTC or NTC type
thermistor. The trip value is adjustable between 1-10Kohm,
preset delay of 2 Sec.
Terminal 29
Thermistor input (T2)
Connect thermistor and/or Analog output shield to ground
terminal.
Terminal 30
Ground
Analog output (0-10VDC or 0-20mA or 4-20mA)
Terminal 31
Analog output (-)
Reflects motor current and is related to 2xIm. i.e., Full scale
(10VDC or 20mA) is related to 2xIm.
Terminal 32
Analog output (+)
Note:
Refer to section
5.7 page 51 for analog output PCB dip switch
setting.
•
Refer to section
Analog Output
programming.
•
Refer to section
Thermistor Type
and
Thermistor Trip
programming.
D-9 connector Profibus communication
(optional)
•
Profibus DPV0 and DPV1, up to 12 MBPS.
•
D type 9 pin connector is applied.
•
Control, monitoring and setting parameters can be achieved
via the Profibus connection.
•
Setting is possible only when DPV1 is implemented.
•
Refer to section
4.7.10 page 42 for programming.
•
Refer to Appendix B of this manual for Profibus protocol
manual.
Terminal V-
0 Volt external power supply
Terminal CL
Negative data line
Terminal Dr
Cable shield
Terminal CH
Positive data line
Terminal V+
DeviceNet communication
(optional)
+24V external power supply