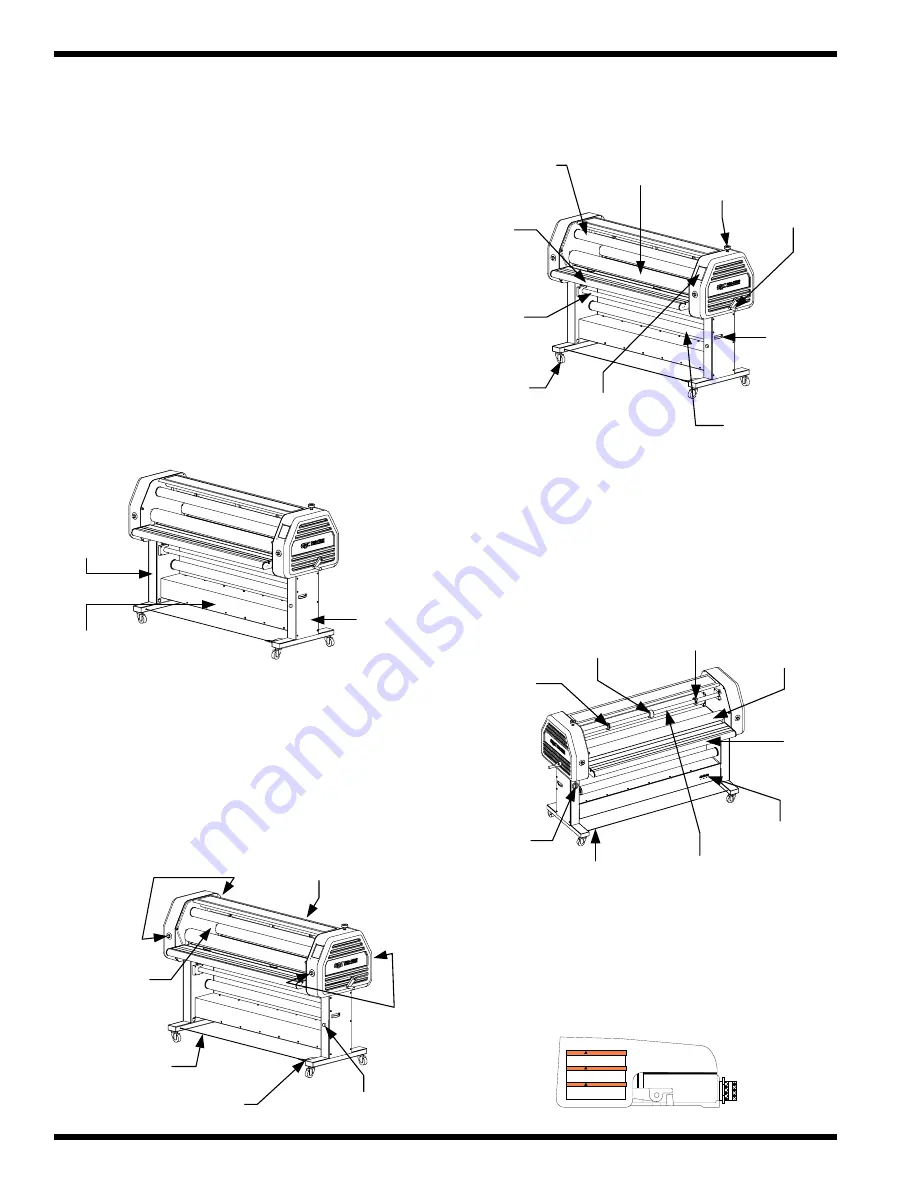
Page 4 - 4
Installation
F - 160 CE Operation and Maintenance Manual
© GBC Films Group April 2000
4.2 Know your machine
Before performing any procedure within this
manual, it is recommended that you take time to know
the parts of your new machine.
Figure 4.2.1 The laminator
Rear side
Electrical
bridge
Drive
side
Control
side
Control
side leg
Drive
side leg
Front side
Figure 4.2.2 Safety features
Rear safety shield
E-CABLE
E-STOP
E-STOP
Front safety
shield
E-CABLE reset
Machine reset
Figure 4.2.3 Front view
Lower
unwind
shaft
Lower
unwind
brake
Upper
unwind
brake
Upper
rewind
Lower
rewind
Castors
Pull roll
lift handle
Control
panel
Front
feed
table
Main
rollers
Figure 4.2.4 Rear view
E-CABLE
Circuit
breaker
Power
ON/OFF
Core
chuck
Core
chuck
Core
support
Pull rollers
Rear
feed
table
Upper
unwind
shaft
Figure 4.2.5 Footswitch
ATTUNG
WARNING
ADVERTENCIA