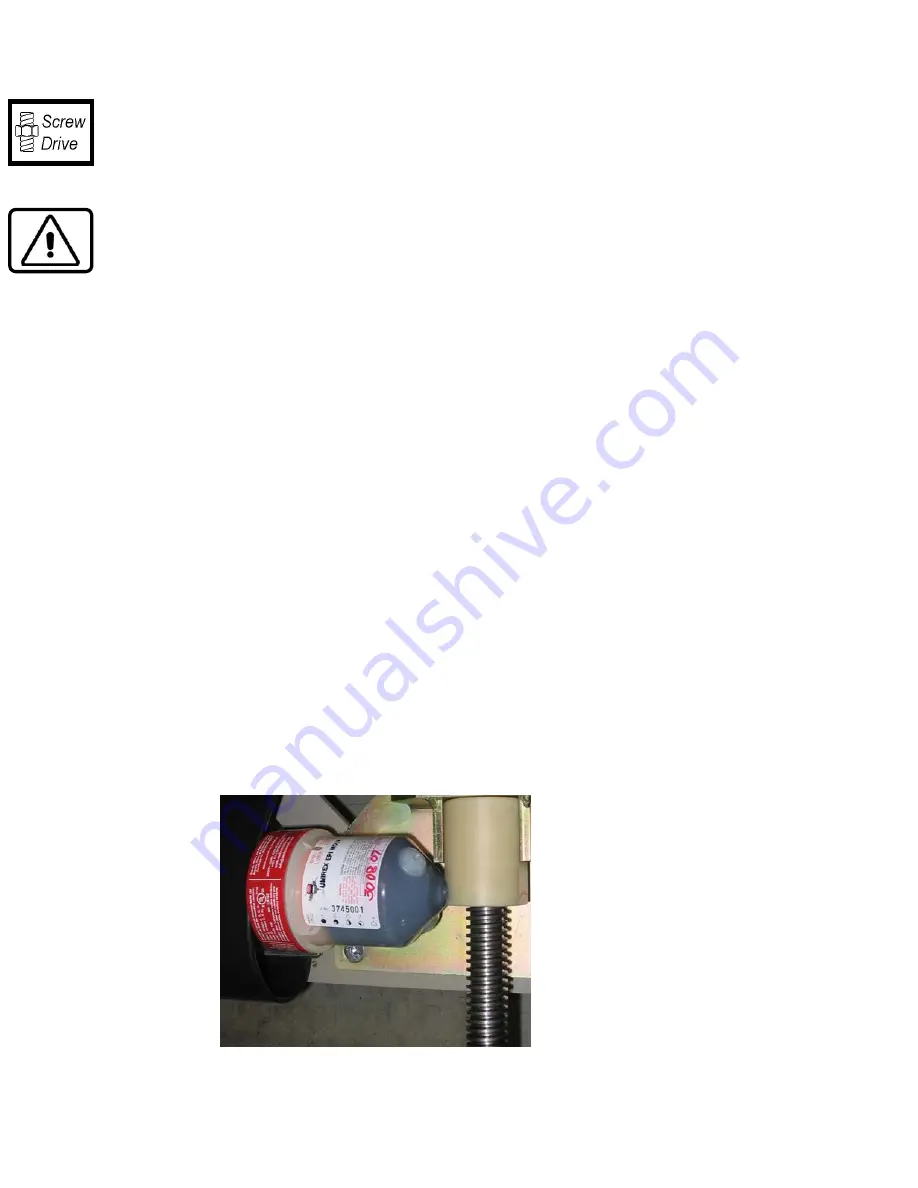
ITEM #05739 Rev B
6
Grease canister inspection and replacement:
The operation of the grease canister on the Genesis Leadscrew lift is vital for lift
operation. No lift may be operated unless the grease canister is operating as well.
Otherwise, the screw will run dry and the Drive and Safety Nuts will start to wear.
The only way to ensure appropriate lubrication of the leadscrew is to observe the
grease canister and to replace it on a regular basis. Do not leave a grease canister on a
lift unless it has enough grease to take it through until your next visit. Always replace the
canister if you are in doubt that it will last until the next maintenance visit.
It is easy to tell if a grease canister is operating. The canisters used on the Genesis
today are triggered by an electrical system. Every 20 to 30 seconds a green light
flashes in the top of the canister indicating that it is active. The canister also has level
indicators on the side showing when it is full, ¾, ½, and ¼.
When replacing a grease canister, remove the old one by unscrewing it from the piping.
Be ready to catch the grease that will come out once the threads are opened. Take this
grease and any grease around the Drive Nut, and apply it to the entire length of the
screw. Activate the new canister open the access window on the top and turn the dip
switch marked “LIGHT” over towards the “ON” position. Then set the greaser to the
appropriate dispensing period. You have a choice of 1, 2, 3, 6 and 12 months. The rate
you choose will depend on how much the lift is used. It is usually set to the 6 to 12
month setting. Whatever you choose, make sure y that you return for the next service
visit before it runs out. Often, updating the service log for the lift with the “Next Service
Is Due” date is the best way of keeping track of this. Replace the cap back onto the
canister.
The new canister may then be screwed onto the piping. Make sure you don’t cross
thread it. Once activated, the canister must be installed. It cannot be deactivated.
For older lifts using the “Simalub” greasing system, refer to technical Bulletin # 2001-
011-00 for information on an update kit.
The grease canister in
place. Note the level
indicators on the side.
This is the newer
“Electro-Lube” system.