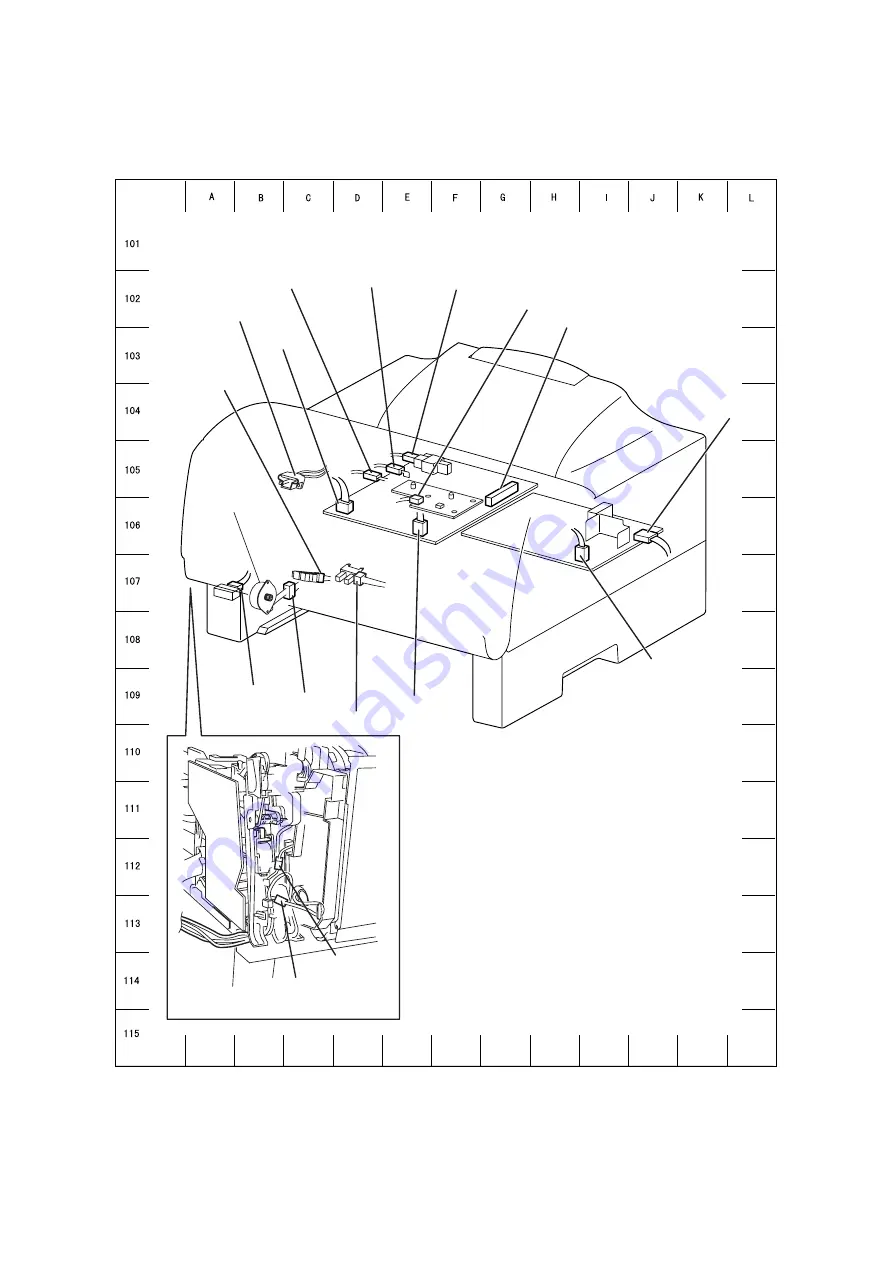
Chapter 7 Wiring Data
7.1 Connector [P (plug) / J (jack)]
7-3
7.1.2 IOT P/J layout diagram
AZS641CA
CN201
P/J301
CN203
P/J302
CN204(TR)
CN205(VG)
CN206(VD)
P/J303B
P/J1002
P/J1101
P/J500
CN202(DB)
P/J1003
P/J1001
P/J1102
P/J1110
(HVPS)
(LVPS)
SWITCH
P/SIZE
MOTOR ASSY
FEED
SENSOR PHOTO
(MSI)
SENSOR
PHOTO
(PWBA
SENSOR)
Summary of Contents for DocuPrint 2050
Page 1: ...DocuPrint 2050 Service Manual 1st Edition KON001CA ...
Page 3: ...Company Name Department Name Telephone No Full Name Employee No ...
Page 5: ...Preface ...
Page 11: ...Chapter 1 Service Call Procedure ...
Page 19: ...Chapter 2 Troubleshooting ...
Page 85: ...Chapter 3 Image Quality Troubleshooting ...
Page 114: ...Chapter 4 Disassembly Assembly and Adjustment ...
Page 193: ...Chapter 5 Parts List ...
Page 207: ...Chapter 6 General ...
Page 243: ...Chapter 7 Wiring Data ...
Page 247: ...Chapter 7 Wiring Data 7 1 Connector P plug J jack 7 4 ...
Page 252: ...Chapter 7 Wiring Data 7 3 Wiring Diagram between Parts 7 9 Continued from the preceding page ...
Page 264: ...Chapter 10 Machine Overview ...