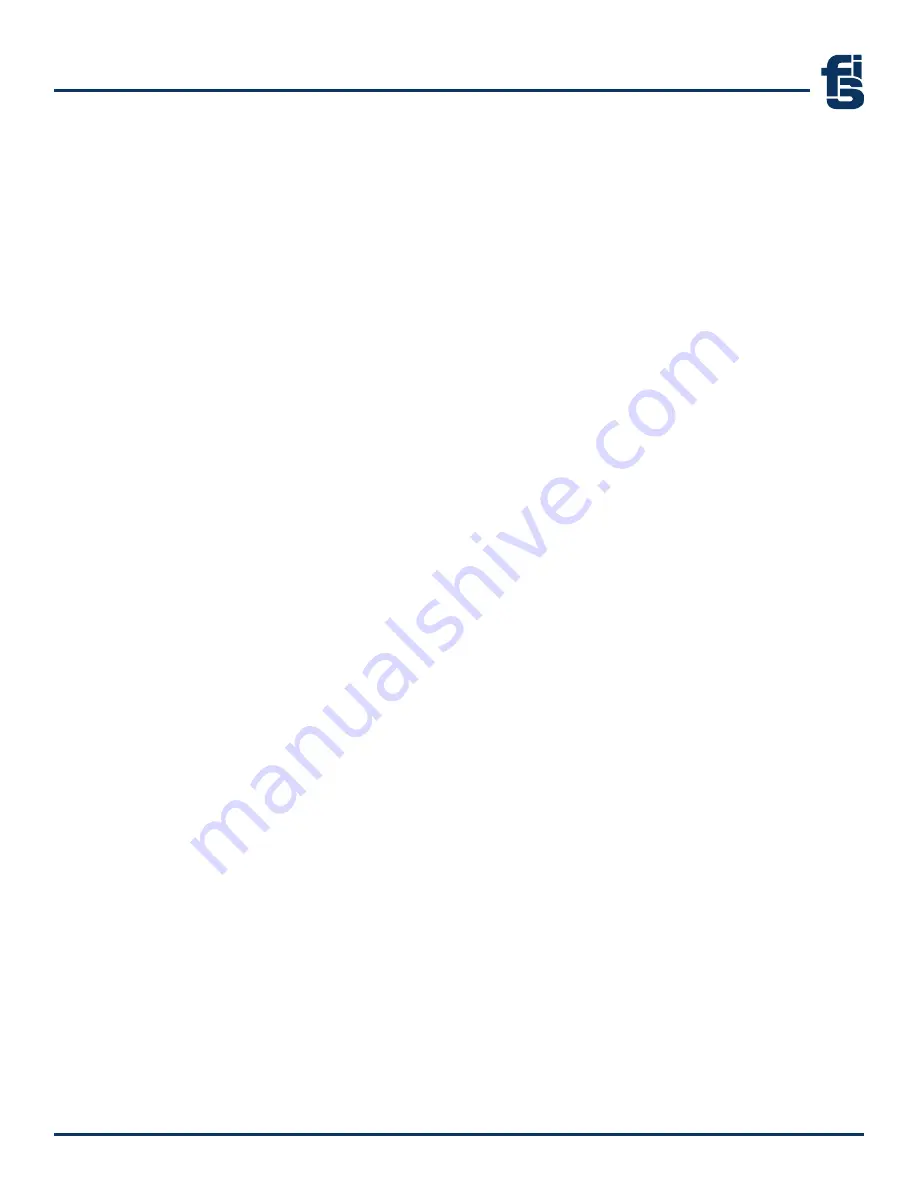
PROCESS DESCRIPTION
4
LIQUID-BLOWN AND FROTH SYSTEMS AND EQUIPMENT
FSI liquid-blown and froth chemicals are contained in pressurized cylinders with the isocyanate
component labeled A-component, or A-SIDE, and the polyol component labeled B-component, or
B-SIDE. The color code for the
A-SIDE is RED. The color code for the B-SIDE is BLUE. F-6000
(350-gallon) and F-5000 (303-gallon) cylinders are color coded on the top rings of the cylinder. Detailed
cylinder schematics and descriptions are given later in this manual.
Liquid-blown and froth systems are dispensed through specifically designed equipment and do not
require pumps or any mechanically driven parts. The chemicals are shipped at 25 p.s.i. or 75 p.s.i. For
safety, each cylinder is equipped with a pressure relief valve set at 275 p.s.i. The cylinders should be
placed in an area (typically a “conditioning room”) where the chemical can be maintained at proper
temperatures. Operating nitrogen pressure for the cylinders and equipment is 240 to 245 p.s.i.
IMPORTANT: CYLINDERS MUST BE BROUGHT TO RECOMMENDED TEMPERATURE BEFORE
ADDITIONAL PRESSURE IS ADDED!
The 240 to 245 p.s.i. blanket is maintained through a regulator unit(s) from bulk or bottled nitrogen. This
pressure drives the chemical through a cylinder-to-hose connection (Stratoflex fitting, filter assembly,
hoses, &
SLUG PRO gun body) on both the “A” and “B” side. (NOTE: FSI DOES NOT supply nitrogen.
Nitrogen must be secured from an outside supplier.)
The chemical streams impinge in the SLUG PRO Mix Cartridge at approximately 120 p.s.i. The
combined chemicals pass through an FSI
mix tube and into the desired part to be foamed.
FIXTURE DESIGN
When designing fixtures, extreme care should be taken to avoid creating a heat sink, a condition in
which the fixture and surrounding mass draws heat from the chemical reaction. Remember that excess
heat or cold is devastating to the chemical reaction and subsequently to production. Keep in mind the
differences in pressuresbetween pour systems and froth systems. Pressure differentials should be taken
into consideration when designing fixtures, molds, and parts for manufacturing. Historically, fixtures
have been designed to withstand 20-30 p.s.i.
www.foamsupplies.com
|
www.ecomatetechnology.com
|
1.800.325.4875
Summary of Contents for PROFESSIONAL Series
Page 2: ...www foamsupplies com www ecomatetechnology com 1 800 325 4875 ...
Page 7: ...PROCESS DESCRIPTION ...
Page 10: ...5 www foamsupplies com www ecomatetechnology com 1 800 325 4875 ...
Page 11: ...EQUIPMENT DESCRIPTION ...
Page 16: ...11 www foamsupplies com www ecomatetechnology com 1 800 325 4875 ...
Page 17: ...CHEMICAL PREPARATION STORAGE HANDLING ...
Page 21: ...INSTALLATION ASSEMBLY ...
Page 24: ...19 www foamsupplies com www ecomatetechnology com 1 800 325 4875 ...
Page 25: ...PRODUCTION AND QUALITY CONTROL ...
Page 32: ...27 www foamsupplies com www ecomatetechnology com 1 800 325 4875 ...
Page 34: ...29 www foamsupplies com www ecomatetechnology com 1 800 325 4875 ...
Page 35: ...CHANGING CHEMICAL CYLINDERS ...
Page 40: ...35 www foamsupplies com www ecomatetechnology com 1 800 325 4875 ...
Page 41: ...MAINTENANCE ...
Page 49: ...TROUBLESHOOTING ...
Page 57: ...SAFETY HANDLING ...
Page 62: ...57 www foamsupplies com www ecomatetechnology com 1 800 325 4875 ...
Page 63: ...EQUIPMENT DRAWINGS PARTS ...
Page 64: ...59 www foamsupplies com www ecomatetechnology com 1 800 325 4875 ...