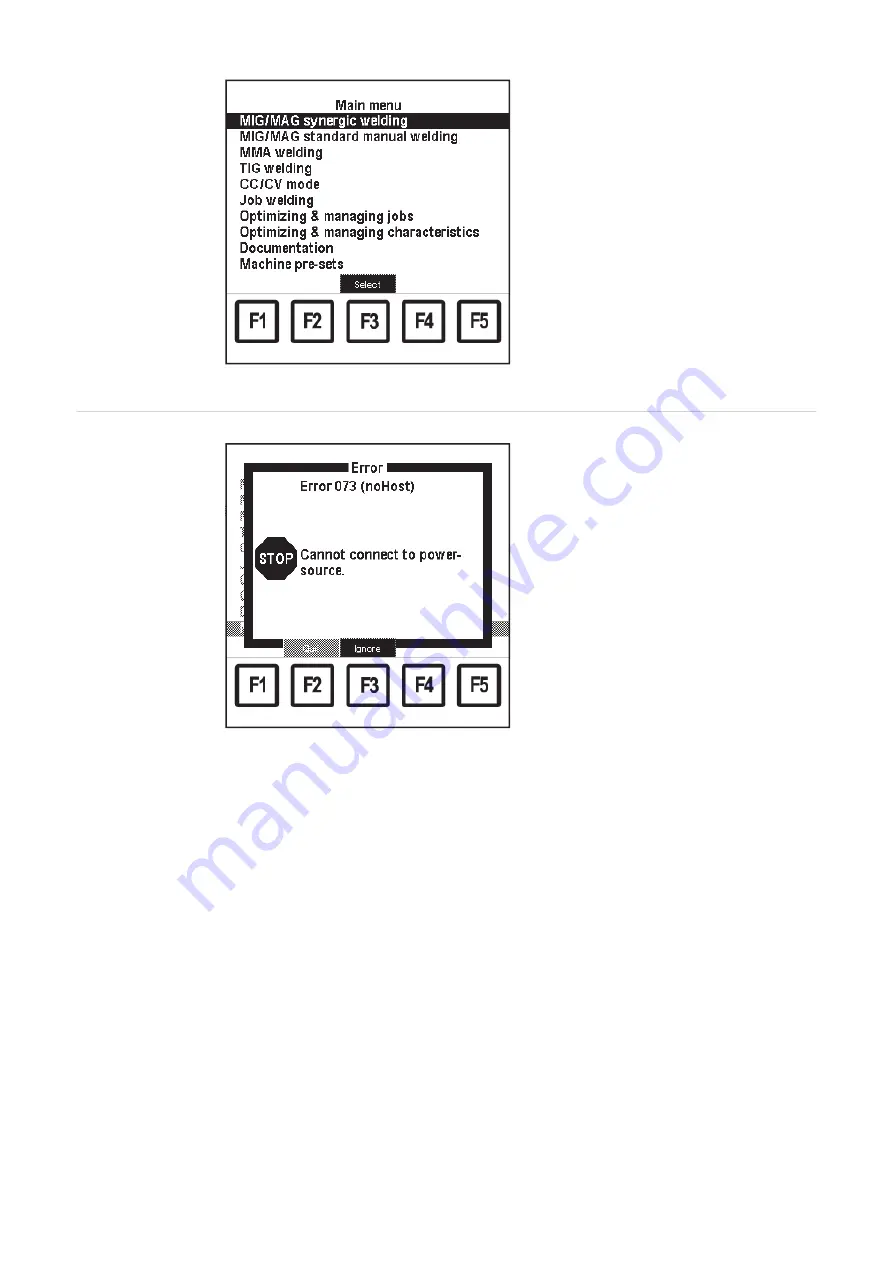
30
Main menu in the selected language
Main menu appears in the selected langua-
ge
Error "073 (no
Host)" - No con-
nection to the
power source
"Error 073 (no Host)" screen
The non-resettable error "073 (no Host)"
appears if the remote control cannot
connect to the power source during com-
missioning.
Possible causes are, for example, poor
contact with the power source or incorrect
LocalNet distributor.
Once an active link is established, error
"073 (no Host)" disappears.
The error "073 (no Host)" can be ignored.
Summary of Contents for RCU 5000i
Page 2: ...2 ...
Page 4: ...4 ...
Page 200: ...200 Backup screen All data from the remote control unit are sa ved onto the memory card ...
Page 202: ...202 Restore screen The last Data screen called up appears ...
Page 207: ...207 EN Machine pre sets MIG MAG screen MIG MAG screen appears ...
Page 210: ...210 Machine pre sets e g MIG MAG screen The last Data screen called up appears ...
Page 242: ...242 ...
Page 243: ...Appendix ...
Page 244: ...244 Spare parts list RCU 5000i ...
Page 245: ...245 ...
Page 246: ...246 ...
Page 247: ...247 ...