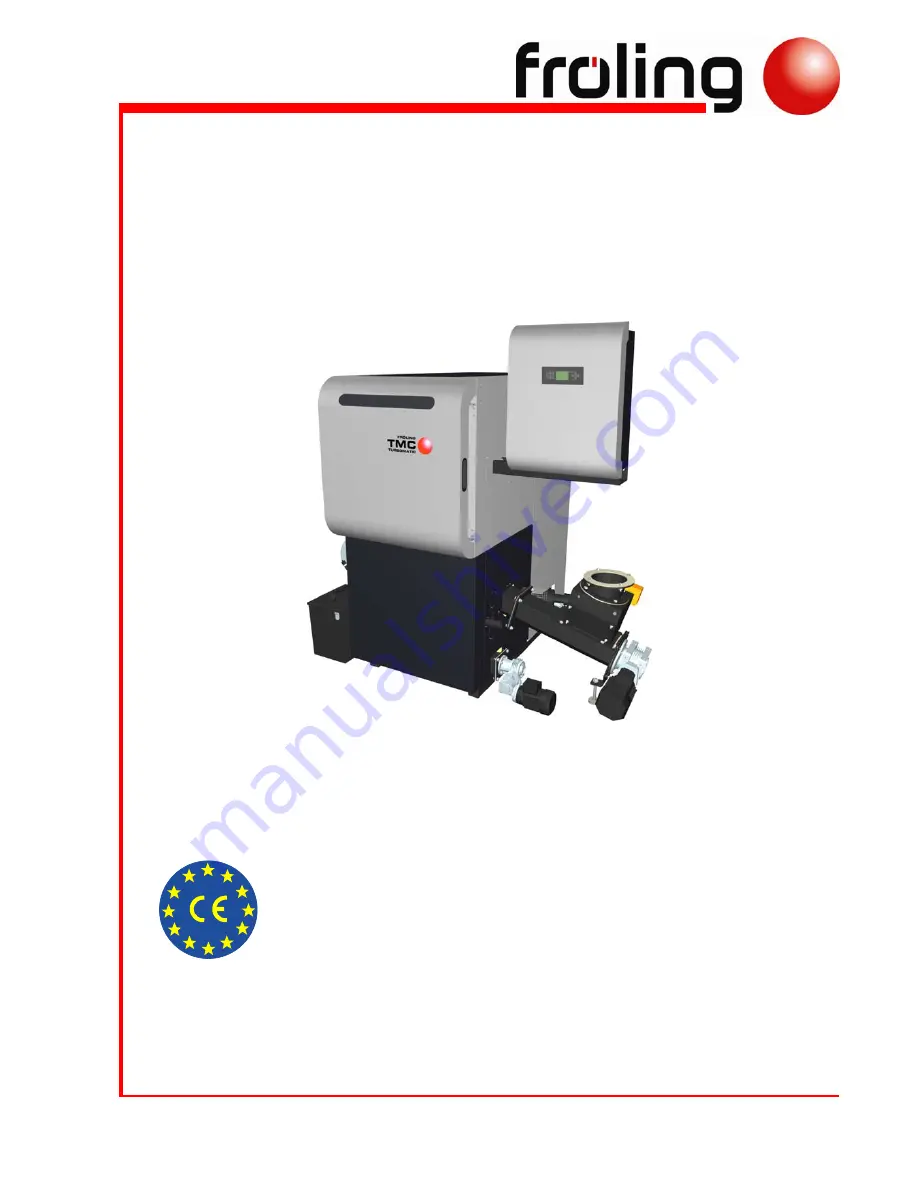
Fröling Heizkessel- und Behälterbau Ges.m.b.H, Industriestrasse 12, A-4710 Grieskirchen
Tel +43 (0) 7248 606-0 Fax +43 (0) 7248 606-600 [email protected] www.froeling.com
Installation Instructions
Turbomatic TMC 70-100
Be sure to read and comply with the operating instructions and safety
instructions.
Subject to technical change.
Summary of Contents for Turbomatic TMC 100
Page 2: ......