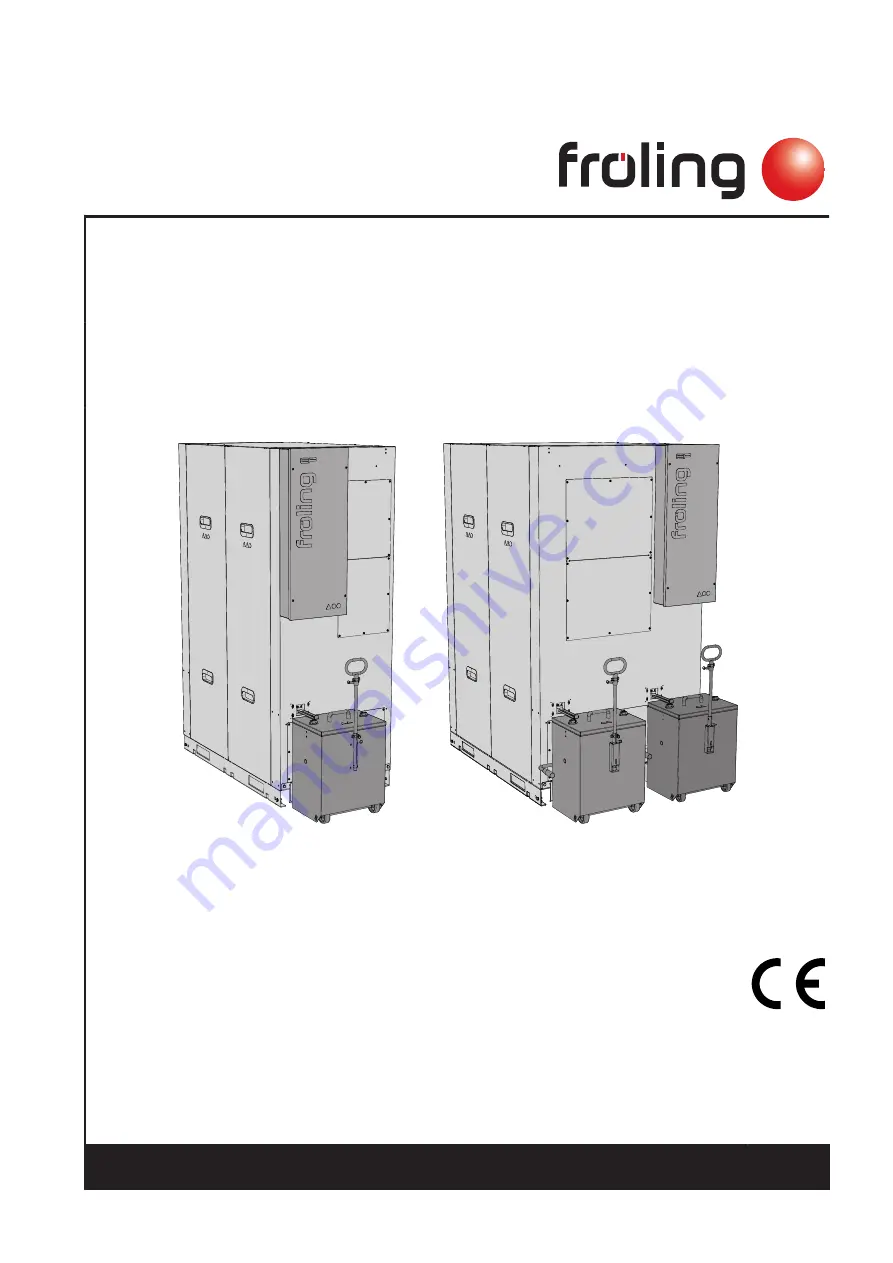
Installation and Operating Instructions
Modular electrostatic precipitator system EF 250-500
EF 250
EF 500
Translation of the original German operating and installation instructions for technicians and operators
Read and follow the instructions and safety information!
Technical changes, typographical errors and omissions reserved!
M2140120_en | Edition 08/09/2020
Fröling GesmbH | A-4710 Grieskirchen, Industriestraße 12 | www.froeling.com