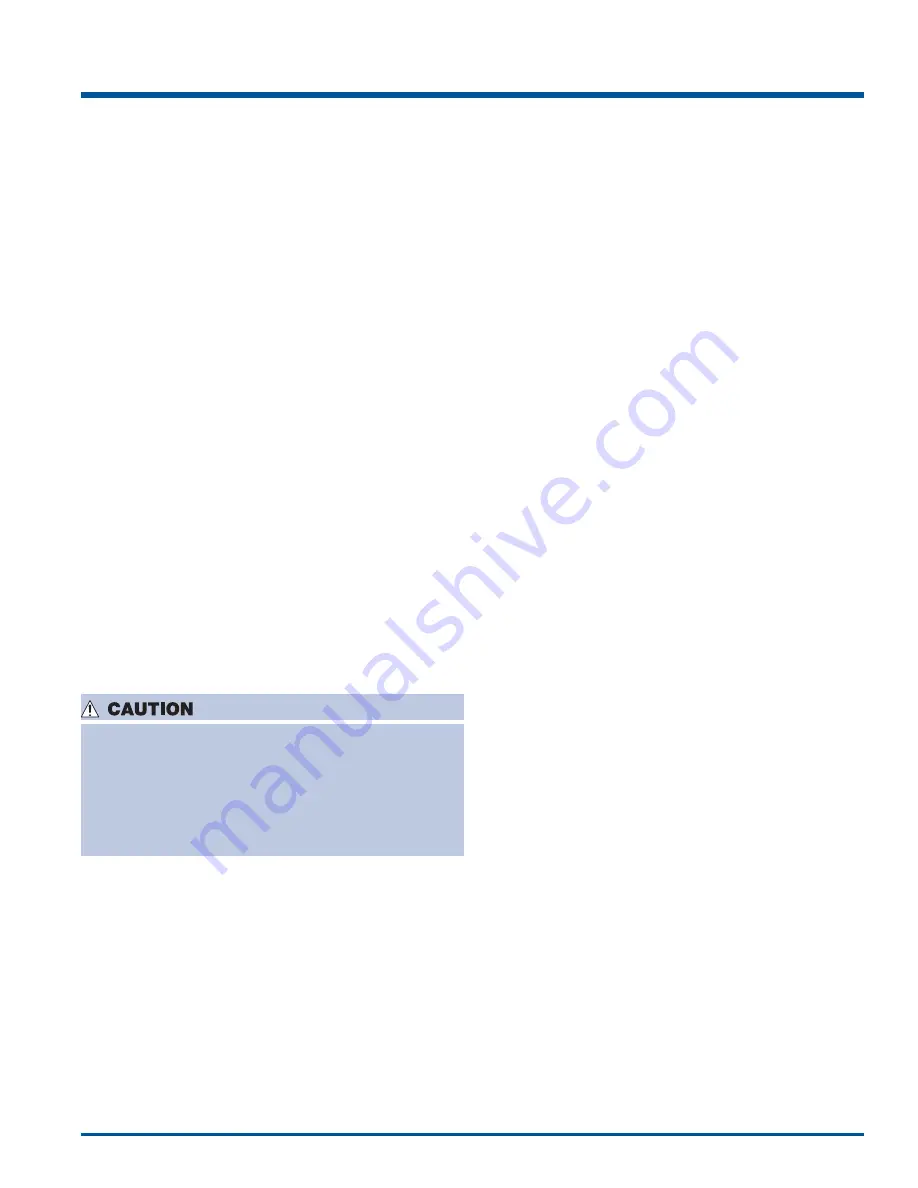
Sealed System
7-3
Introduction
This Service manual is intended as a guide for
introducing the service technician to R-134a refrigerant,
and the equipment needed to service R-134a systems.
The replacement of R-12 refrigerant involves changes
in materials, choice of lubricant, and processing
procedures, with an overall requirement of continuous
high quality system performance and reliability. The
following information provides a good practical
foundation for service needed to maintain long product
life.
Compressor
In a refrigerating system designed for R-134a refriger-
ant, only R-134a refrigerant is to be used. The current
design of hermetic compressors lead to the situation
that some oil (a small percentage) will follow with the
refrigerant through the whole system. R-134a
compressors require a new lubricant. At this time, only
synthetic ester oil is to be used. The R-12 compressors
used mineral oil. Mineral oil is not compatible with
R-134a and is not to be used in R-134a systems. Ester
oil must not be mixed nor replaced with any other
lubricant. Compressors used with R-134a systems
charged with oil, cannot have any tube fittings exposed
to ambient air for more than 15 minutes. Ester oil is
more hygroscopic (it will absorb water at a much faster
rate) than the mineral oil used with R-12 systems.
Refrigeration Systems
The sealed refrigeration system will consist of the same
basic components being utilized in the R-12 systems.
There is a 10% to 15% discharge pressure increase
using R-134a, with a 5% to 10% decrease in suction
pressure when compared to the same product with an
R-12 system operating at 90°F (32°C) ambient
temperature conditions. Lower suction pressures result
from the lower density of R-134a refrigerant which
effects refrigerant flow rate. R-134a systems commonly
operate in a 1”-2” vacuum on the suction side.
Products using R-134a refrigerant will have a different
heat exchanger than a R-12 product. The difference is
in the capillary tub, it will be longer to maintain a similar
flow rate. On some models, a larger condenser will be
used to reduce the discharge pressures and lower
start-up sound transmission. A different filter-drier will be
used on refrigerating systems with R-134a. The
molecules of R-134a are smaller than those of R-12,
therefore, a dryer with smaller pores is necessary.
Otherwise, R-134a could be trapped inside the filter-
drier along with the water. On some products you will
see some changes to the evaporator and suction line.
Ester oil and R-134a mix satisfactorily within the
compressor. Lower gas speed increases the risk of oil
accumulation in the evaporator. Some changes will be
required to ensure good oil returnability.
Sealed System Repair
To prevent any form of cross contamination of R-134a,
and R-12 refrigerant, or a cross contamination of ester
oil and mineral oil, you must have dedicated equipment.
The equipment consists of one set of gauges, manifold,
hoses, vacuum pump, charging cylinder, and
reprocessing or transfer pump. This means you must
have one complete set for CFC, (R-11, R-12) and HCFC,
(R-22) systems, and one complete set for HFC,
(R-134a) systems. You can not share the use of any of
the same equipment on both systems.
Since the R-134a molecule is smaller than the R-12
molecule, R-134a could pass more minor leaks than
R-12 and the flow through a certain leak would be larger
for R-134a than for R-12. As a consequence, it is critical
to maintain very good brazing processes and leak tests.
You must make sure you do not mix refrigeration oil or
refrigerant in your bulk storage area. Because moisture
infiltration is much higher in ester oil, you must keep it
stored in sealed containers and only allow exposure to
room air for a very short period of time when changing
or adding oil to a system. You must not mix refrigerant
in your storage containers for used refrigerant removed
from products for service. You must have dedicated
cylinders for each refrigerant R-12, R-22, and R-134a.
Ester oil can be an irritant to eyes and skin. Refer
to manufacture safety data sheets from lubricant
supplier for handling specifications. As with all
current refrigerants, you must have an adequately
ventilated work area at all times for sealed system
service and repairs.
Summary of Contents for LGUB2642LF2
Page 2: ......
Page 10: ...1 8 Basic Information Models with Freezer Ice Maker NOTE Features may vary according to model ...
Page 22: ...Installation Information 2 10 ...
Page 44: ...Electronic Control 3 22 Voltage Flow Chart Figure 3 20 ...
Page 50: ...4 6 Flow Chart 1 No Ice Ice Maker Flex Tray Fresh Food Compartment ...
Page 61: ...4 17 Flow Chart No Ice 1 Ice Maker Finger Evaporator Fresh Food Compartment ...
Page 62: ...4 18 Flow Chart No Ice 2 Ice Maker Finger Evaporator Fresh Food Compartment ...
Page 63: ...4 19 Flow Chart No Ice 3 Ice Maker Finger Evaporator Fresh Food Compartment ...
Page 64: ...4 20 Flow Chart No Ice 4 Ice Maker Finger Evaporator Fresh Food Compartment ...
Page 65: ...4 21 Flow Chart No Ice 5 Ice Maker Finger Evaporator Fresh Food Compartment ...
Page 66: ...4 22 Flow Chart No Ice 6 Ice Maker Finger Evaporator Fresh Food Compartment ...
Page 67: ...4 23 Flow Chart Test 48C Ice Maker Finger Evaporator Fresh Food Compartment ...
Page 68: ...4 24 Flow Chart Test 49C Ice Maker Finger Evaporator Fresh Food Compartment ...
Page 69: ...4 25 Flow Chart Test 50C Ice Maker Finger Evaporator Fresh Food Compartment ...
Page 70: ...4 26 Flow Chart 51C Ice Maker Finger Evaporator Fresh Food Compartment ...
Page 71: ...4 27 Flow Chart 52C Ice Maker Finger Evaporator Fresh Food Compartment ...
Page 72: ...4 28 Flow Chart 54C Ice Maker Finger Evaporator Fresh Food Compartment ...
Page 73: ...4 29 Flow Chart 55C Ice Maker Finger Evaporator Fresh Food Compartment ...
Page 74: ...4 30 Flow Chart 56C Ice Maker Finger Evaporator Fresh Food Compartment ...
Page 75: ...4 31 Flow Chart 57C Ice Maker Finger Evaporator Fresh Food Compartment ...
Page 76: ...4 32 Flow Chart 58C Ice Maker Finger Evaporator Fresh Food Compartment ...
Page 77: ...4 33 Flow Chart 59C Ice Maker Finger Evaporator Fresh Food Compartment ...
Page 78: ...4 34 Flow Chart 60C Ice Maker Finger Evaporator Fresh Food Compartment ...
Page 79: ...4 35 Flow Chart 61C Ice Maker Finger Evaporator Fresh Food Compartment ...
Page 80: ...4 36 Flow Chart 62C Ice Maker Finger Evaporator Fresh Food Compartment ...
Page 81: ...4 37 Flow Chart 63C Ice Maker Finger Evaporator Fresh Food Compartment ...
Page 82: ...4 38 Flow Chart ICE t3 Error Ice Maker Finger Evaporator Fresh Food Compartment ...
Page 97: ...4 53 Step 7 Step 8 Step 9 Step 10 Ice Maker Freezer Compartment ...
Page 99: ...4 55 4 55 Notes Ice Maker ...
Page 100: ...4 56 ...
Page 106: ...Water System 5 6 ...
Page 144: ...6 38 Component Teardown ...
Page 178: ...7 34 Sealed System ...
Page 180: ...Air Circulation 2 ...
Page 181: ...Wiring Schematics 9 1 Dispenser Models with Flex Tray Fresh Food Ice Maker ...
Page 182: ...Wiring Schematics Dispenser Models with Finger Evaporator Fresh Food Ice Maker 9 2 ...
Page 183: ...Wiring Schematics Non Dispenser Models 9 3 ...
Page 184: ...Wiring Schematics ...
Page 186: ...Wiring Schematics Dispenser Model with Finger Evaporator Fresh Food Ice Maker 242058901 9 5 ...