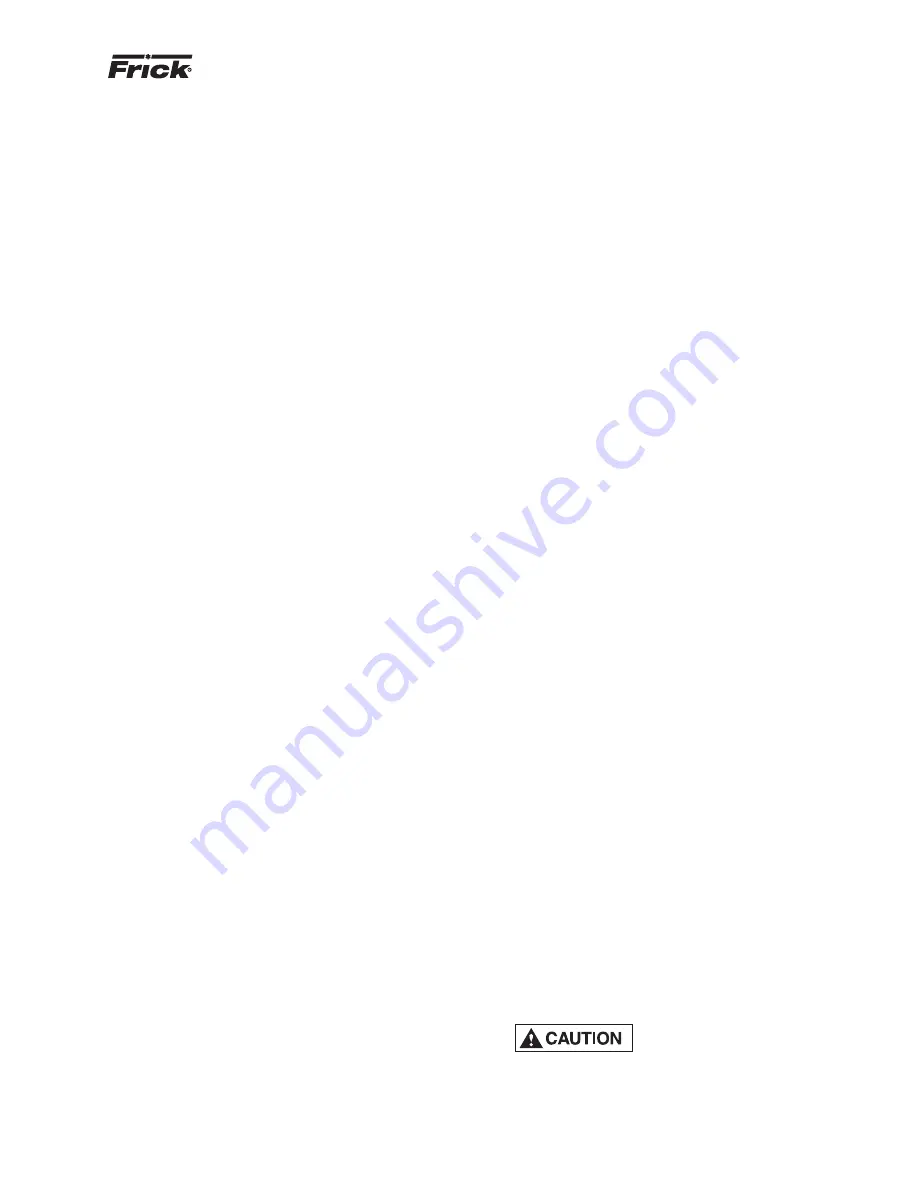
RWB II ROTARY SCREW COMPRESSOR UNITS
OPERATION
S70-200 IOM
Page 19
COMPRESSOR OIL COOLING SYSTEMS
The RWB II unit can be equipped with one of several sys-
tems for controlling the compressor oil temperature. They are
single or dual-port liquid injection, or thermosyphon and
water-cooled oil coolers. Each system is automatically con-
trolled, independent of compressor loading or unloading.
Oil cooling systems should maintain oil temperature within
the following ranges for R-717 and R-22:
Liquid Injection
External*
Oil Cooling
Oil Cooling
130 - 150°F
120 - 140°F
* Thermosyphon oil cooling (TSOC) or Water-cooled oil cool-
ing (WCOC).
SINGLE-PORT LIQUID INJECTION
The single-port liquid injection system is designed to permit
liquid refrigerant injection into one port on the compressor at
any given moment and operates as outlined.
Solenoid valve SV5 is energized by the microprocessor when
the temperature sensor, installed in the oil manifold, exceeds
the LICO set point. High pressure liquid refrigerant is then
supplied to the temperature control valve (TCV). The tem-
perature control valve is equalized to a constant back pres-
sure by the differential pressure control valve (PDCV). The
differential pressure control valve uses discharge gas to
maintain downstream pressure. The gas downstream of the
differential pressure control valve is bled off to the compres-
sor suction to ensure steady and constant operation of the
valve.
RWB II BOOSTER OR SWING DUTY
APPLICATION
Discharge gas from the high stage compressor is required
to assist the differential pressure control valve (PDCV) in pro-
viding the temperature control valve (TCV) with a constant
back pressure.
A solenoid valve SV6 is installed before the differential pres-
sure control valve (PDCV) to prevent migration of high pres-
sure gas during shutdown. A Frick-installed timer limits the
high pressure gas to only thirty seconds duration, since in-
termediate gas pressure and spring tension are sufficient to
maintain closure on unit shutdown. A metering valve is also
provided for use as a service valve and to allow discharge
gas flow regulation to prevent excessive force and resulting
closure “hammering”.
A field-installed 1/4 inch OD tubing connection is required
between the high stage compressor discharge piping line
(or receiver) and the check valve.
DUAL-PORT LIQUID INJECTION
The dual-port liquid injection system is designed to obtain
the most efficient compressor performance at high and low
compression ratios by permitting injection of liquid refriger-
ant into one of two ports optimally located on the compressor.
This minimizes the performance penalty incurred with liquid
injection oil cooling.
The dual-port system contains all the components of the
single-port system with the addition of a double acting sole-
noid valve SV7 and operates as outlined.
Solenoid valve SV5 is energized by the microprocessor when
the temperature sensor, installed in the oil manifold, exceeds
the LICO set point. Liquid refrigerant is then passed through
the temperature control valve (TCV) to the double-acting
solenoid valve SV7. Depending on the compressor’s operat-
ing volume ratio (Vi), the microprocessor will select the flow
of the liquid refrigerant to either compressor port SL-1 or SL-2,
whichever is more efficient.
When the compressor operates BELOW 3.5 Vi, compressor
port SL-1 supplies the liquid cooling. When the (Vi) rises
ABOVE 3.5 Vi, port SL-2 supplies the liquid cooling.
The temperature control valve is equalized to a constant back
pressure by the differential pressure control valve (PDCV).
Both the differential pressure control valve (PDCV) and the
double-acting solenoid valve SV7 use discharge gas to main-
tain downstream pressure. The gas downstream of both
valves is bled off to the compressor suction to ensure steady
and constant operation of the valves.
LIQUID INJECTION ADJUSTMENT
PROCEDURE
1. Close back-pressure bleed valve (V4).
2. Set pressure regulator valve (PDCV) for approximately
100 to 110 psig.
3. Open back-pressure bleed valve (V4) approximately one
quarter turn.
4. Monitor the oil temperature of the compressor. If the oil
temperature rises above 150°F, open back-pressure bleed
valve (V4) a very small amount. This will reduce pressure on
the equalizer and allow more refrigerant to flow to the com-
pressor. If the oil temperature drops below 130°F, close back-
pressure bleed valve (V4) a very small amount. This will in-
crease pressure on the equalizer and allow less refrigerant
to flow to the compressor, thus raising the oil temperature.
The ideal condition is to maintain an oil temperature as stable
as possible. By keeping the liquid injection system correctly
tuned, extreme swings in the discharge temperature and the
oil temperature can be avoided.
Back-pressure bleed valve (V4) must always be cracked
open a small amount to prevent re-
frigerant from condensing in the
tubing.