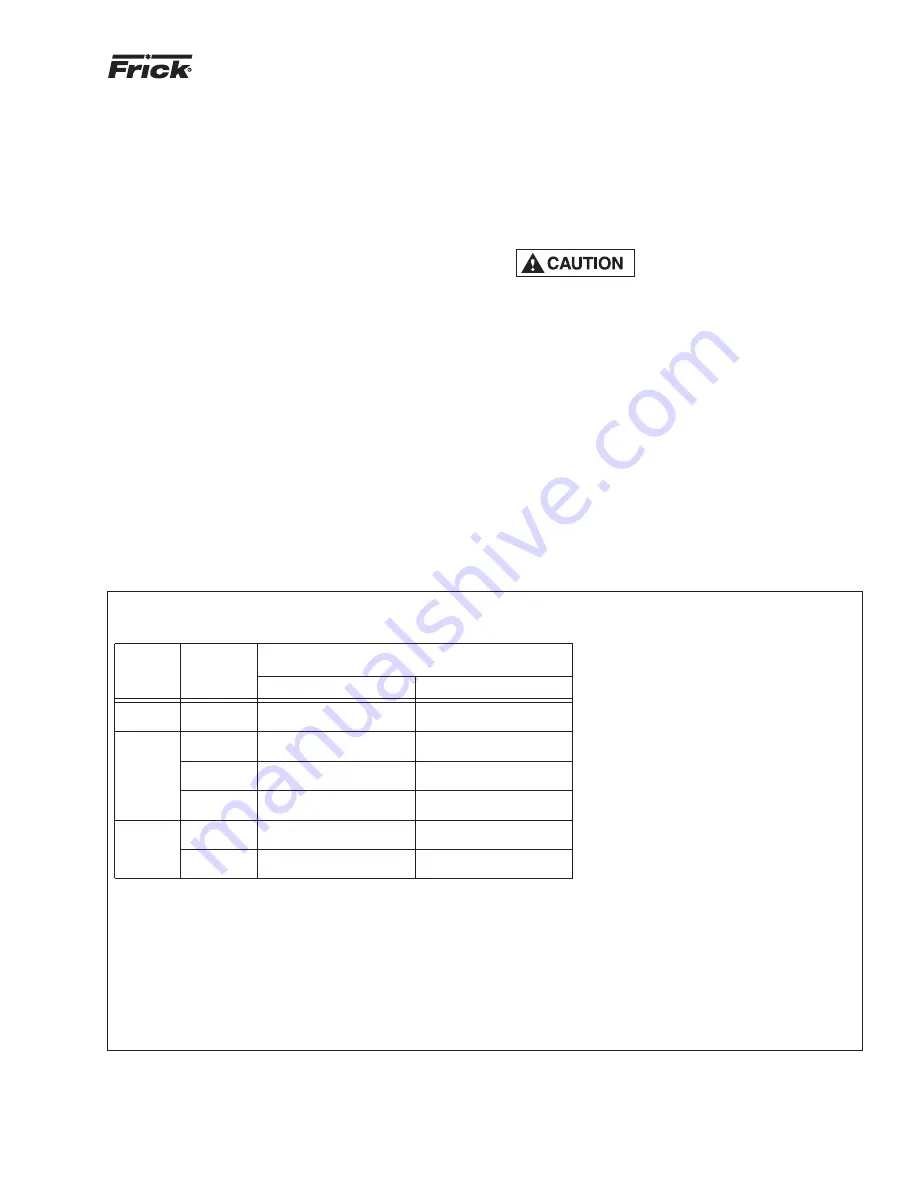
RWB II ROTARY SCREW COMPRESSOR UNITS
MAINTENANCE
S70-200 IOM
Page 29
THE FACTORY INSTALLED, RECOMMENDED LUBRICANT IS LISTED ON THE MOTOR DATA PLATE. THE FOLLOWING PRODUCTS ARE DEEMED
SUITABLE LUBRICANTS UNDER NORMAL SERVICE CONDITIONS BUT MAY NOT BE CHEMICALLY COMPATIBLE OR INTERCHANGEABLE ONE
EXXON CORP. - UNIREX#2
MOBIL OIL CO. - MOBILUX#2
INTRODUCING ALTERNATES - WHEN DOUBT EXISTS, PURGE THE BEARINGS AS DESCRIBED IN THE INSTRUCTION MANUAL.
TO THE OTHER OR CORRECT FOR ALL AMBIENT OR SERVICE CONDITIONS. FOLLOW ALL MANUFACTURER'S GUIDELINES WHEN
CHEVRON OIL CO. - SRI#2
EXXON CORP. - POLYREX
SHELL OIL CO. - DOLIUM R
LUBRICATION SCHEDULE / INSTRUCTIONS
ENVIRONMENTAL EXTREME) = 1/3 OF THE ABOVE INTERVALS.
* LUBRICATION SCHEDULE FOR SEVERE SERVICE (VIBRATION, SHOCK AND/OR
** LUBRICATION SCHEDULE FOR ROLLER BEARINGS = 1/3 OF THE ABOVE INTERVALS.
3600
1200
360-440
5000-5800
1800
5000-5800
400-440
360
360-5800
SYNC.
RPM
FRAME
SERIES
150 DAYS (1200 HRS)
50 DAYS (1200 HRS)
390 DAYS (3120 HRS)
270 DAYS (2160 HRS)
390 DAYS (3120 HRS)
210 DAYS (1680 HRS)
270 DAYS (2160 HRS)
90 DAYS (2160 HRS)
130 DAYS (3120 HRS)
70 DAYS (1680 HRS)
90 DAYS (2160 HRS)
130 DAYS (3120 HRS)
SERVICE CYCLE* - BALL BEARING**
8 HR/DAY OPERATION
24 HR/DAY OPERATION
• REMOVE THE PIPE PLUG FROM THE
VENTING PORT OPPOSITE THE GREASE
APPLY 2 OZS. (60 GRAMS) OF GREASE
• USING A LOW PRESSURE GREASE GUN
AT EACH FITTING. DO NOT OVER GREASE.
15 MINUTES AND UNTIL ANY GREASE FLOW
THE MOTOR FOR A MINIMUM OF
• WITH THE VENT PORTS OPEN, OPERATE
HAS CEASED AT THE VENTING PORTS.
• REPLACE THE VENT PIPE PLUGS.
COVERS THAT MAY HAVE BEEN REMOVED
• REPLACE ANY AND ALL GUARDS AND
• REMOVE POWER.
TO ACCESS THE MOTOR.
FITTING.
• LUBRICATE BEARINGS WITH POWER IN
• CLEAR AND CLEAN THE GREASE FITTINGS
AND SURROUNDING AREA.
THE OFF CONDITION.
RECOMMENDED
MAINTENANCE PROGRAM
In order to obtain maximum compressor unit performance
and ensure reliable operation, a regular maintenance pro-
gram should be followed.
The compressor unit should be checked daily for leaks, ab-
normal vibration, noise, and proper operation. A log should
also be maintained. There should be continued monitoring
of oil quality and oil analysis testing. In addition, an analysis
of the unit’s vibration should be periodically made.
VIBRATION ANALYSIS
Periodic vibration analysis can be useful in detecting bear-
ing wear and other mechanical failures. If vibration analysis
is used as a part of your preventive maintenance program,
take the following guidelines into consideration.
1. Always take vibration readings from exactly the same
places and at exactly the same percentage of load.
2. Use vibration readings taken from the new unit at start-up
as the base line reference.
3. Evaluate vibration readings carefully as the instrument
range and function used can vary. Findings can be easily
misinterpreted.
4. Vibration readings can be influenced by other equipment
operating in the vicinity or connected to the same piping as
the unit.
MOTOR BEARINGS
Follow the motor manufacturer’s maintenance recommenda-
tions. See Figure 26.
Make sure the motor bearings are
properly lubricated before start-up
as required by the motor manufac-
turer.
OIL QUALITY and ANALYSIS
High quality refrigeration oil is necessary to ensure com-
pressor longevity and reliability. Oil quality will rapidly dete-
riorate in refrigeration systems containing moisture, air, or
other contaminants. In order to ensure the quality of the re-
frigeration oil in the compressor unit:
1. Only use Frick refrigeration oil or high quality refrigeration
oil approved by Frick for your application.
2. Only use Frick oil filters or those approved by Frick for your
application.
3. Participate in a regular, periodic oil analysis program to
maintain oil and system integrity.
Figure 26