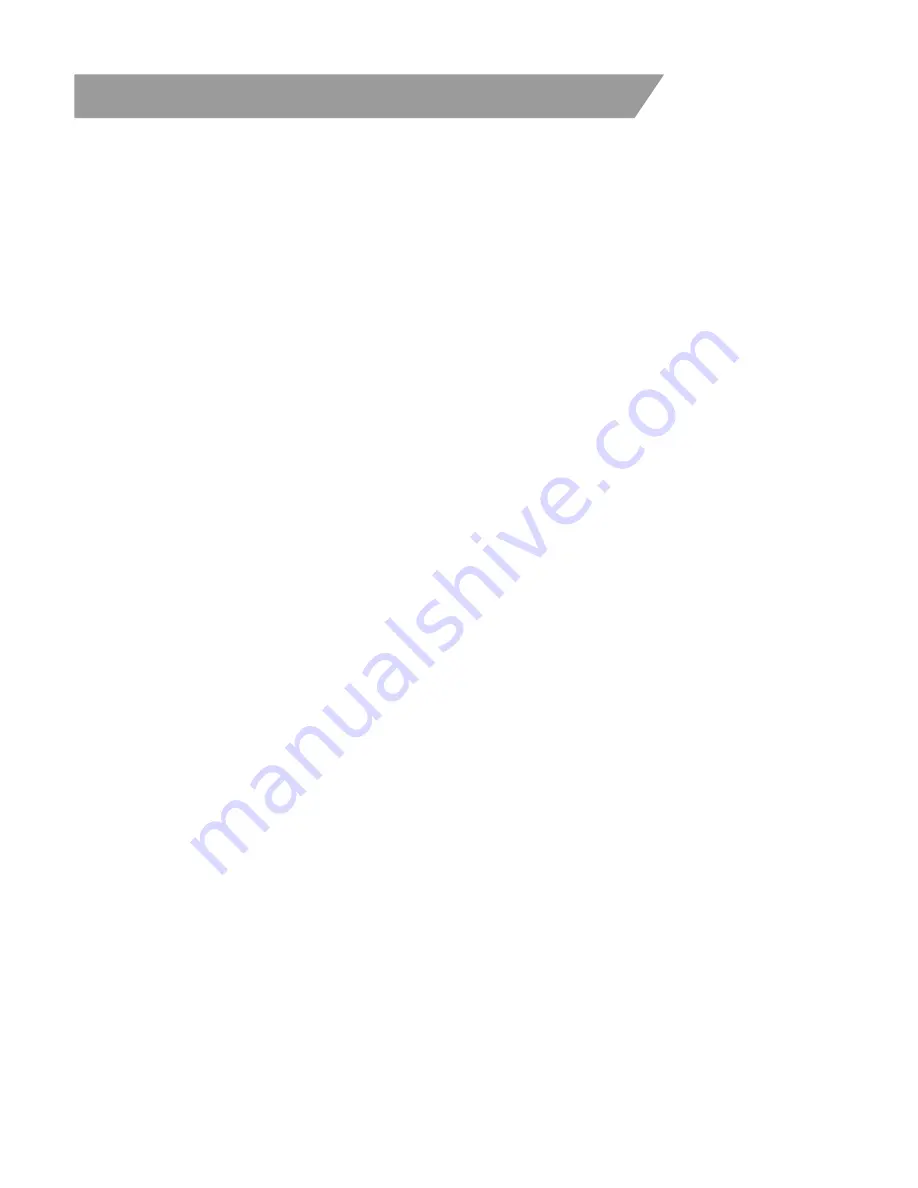
2
SPECIAL TOOLS
MACHINERY AND TOOLS
The minimum basic manual tools and the equipment needed to assemble submersible pumps are:
A. Vernier Caliper type Height Gage, 0-150mm for verifying the height of the arrow
B. Ratchet for 11/16” fastening screws
C. Ratchet for 3/4” fastening tension screws
D. Allen wrench - 5mm (for 6”, 8”, and 10” motor coupling), SAE or standard (T handle preferred)
E. Adhesive Loctite® 302-43
F. Rubber hammer
G. 19 mm and 24 mm sockets, 3/8 drive
Additional machinery and equipment would be required if the assembler wants to cut and remove the rough edges of the
motor and cable guards
• Ridged Assembly Fixture
• Assembly Fixture Bolts
• 6” & 8” Motor Shaft Tool
• Torque Wrenches (20-100Nm, 40-200 Nm)
• Brace for Strap Assembly
• Collet Nut Sockets
TOOL KIT 305472639