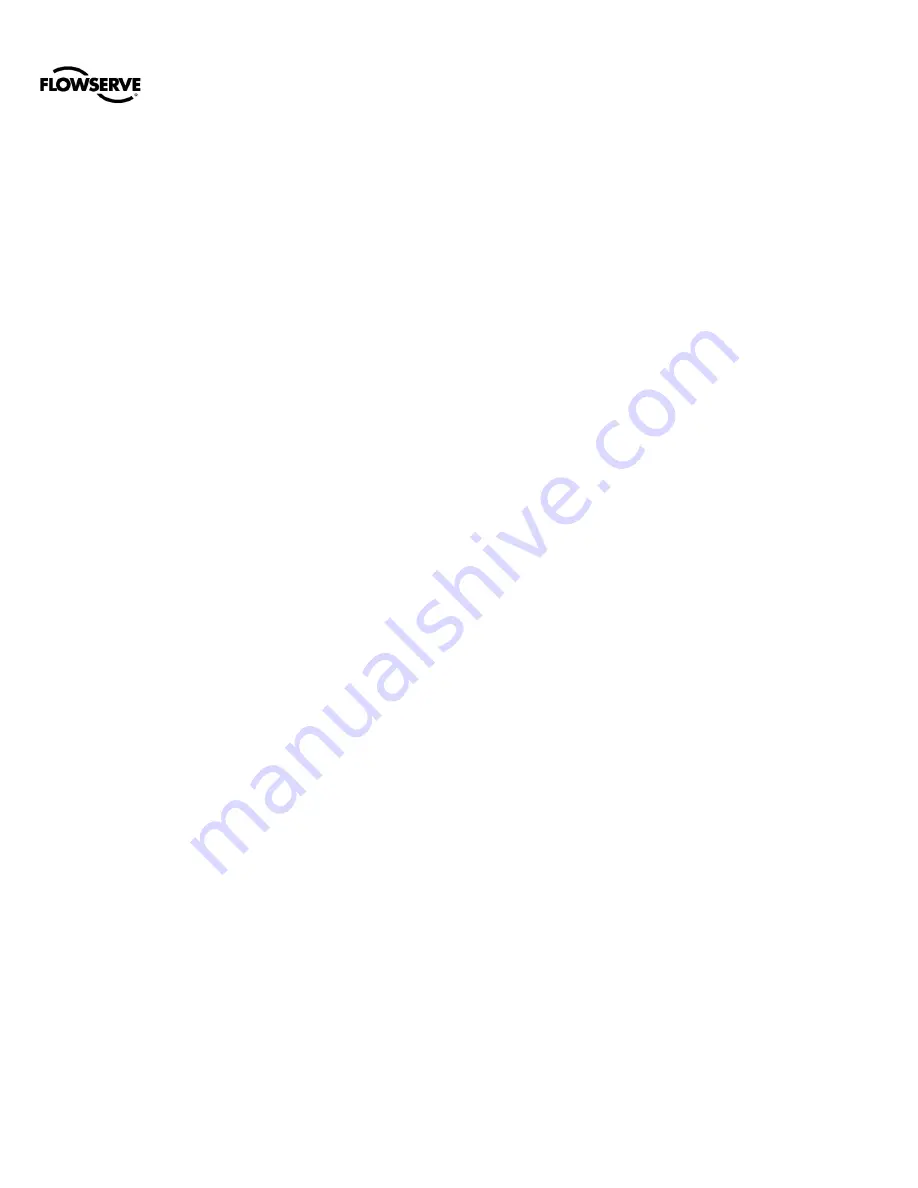
Logix
®
Digital Positioners FCD LGENIM0110-0 05/16
flowserve.com
48
Possible Solutions: Check the stem and actuator for loose
components.
YRYR
●
●
●
●
PNEUMATIC LEAK WARNING
Description: The positioner has detected a leak in the
actuation assembly. Leakage from the actuator can cause
decreased
responsiveness
and
excessive
air/gas
consumption.
Possible Solutions: Repair pneumatic leaks at the tubing
junctions and actuator seals. Check spool valve for
excessive wear.
YRRG
●
●●
●
LOW BATTERY WARNING
Description: The battery for the real time clock is low. The
battery is designed for a 15+ year life with the positioner
unpowered. The battery is not required for the positioner to
control properly, but is used only to maintain the time and
date upon loss of power. The time and date affect the time
stamps of alarms, warnings and other events. This
warning could be caused by rapidly power cycling the
positioner.
Possible Solutions: The battery is not replaceable. Verify
or reset the time and date. Replace the main board if the
problem persists for several days.
YRRY
●
●●
●
PIEZO VOLTAGE HIGH WARNING
PIEZO VOLTAGE LOW WARNING
Description: If the voltage to the piezo is too high, this could
indicate an error with the relay or the main board. This
may result from an extended period of inactivity, but in this
case should not persist for more than 30 minutes when the
valve is controlling. The positioner may still be functioning,
but have reduced performance under some circumstances.
If the voltage to the piezo is too low, the piezo may be
damaged. This may prevent the proper failure position
upon loss of signal/power. This condition may occur briefly
on an air-to-close valve that is held for long periods of time
in the closed position, or an air-to-open valve held in the
open position.
Possible Solutions: Ensure the supply pressure is not low.
If alarm persists for more than 30 minutes, the Piezo
assembly is damaged. Replace the pilot relay.
YRRR
●
●●●
SPRING UNABLE TO FAIL SAFE WARNING
Description: Upon loss of air supply, the valve may not
move to the fail-safe position. The spring alone is not
adequate to overcome the friction and process load in the
system. The system is relying on pneumatic force to
actuate in the direction the spring is pushing. The failsafe
spring may have failed, or it was not sized properly for the
application. Friction or process load may have increased.
Possible Solutions: Repair or replace actuator spring.
Check for high friction. Reduce process load.
RGGG
●
●●●
COMMAND INPUT BELOW ADC RANGE
COMMAND INPUT ABOVE ADC RANGE
COMMAND INPUT RANGE TOO SMALL
Description: During Command Loop Calibration, the signal
was out of the Analog to Digital Converter (ADC) range, or
difference between the signal at 0% and the signal at 100%
was too small. The system is designed to accept a
difference greater than 5 mA and between 10 and 4085
ADC.
Possible Solutions: Recalibrate making sure to use valid
command signal values.
RGGY
●
●●
●
POSITION RANGE TOO SMALL
POSITION SENSOR ABOVE ADC RANGE
POSITION SENSOR BELOW ADC RANGE
Description: During calibration, the range of motion of the
position feedback arm was too small for optimum
performance or the feedback sensor moved beyond its
range of operation.
Possible Solutions: Check for loose linkages. Adjust the
positioner mounting. Adjust the feedback pin back into
range. Adjust the feedback pin to a position closer to the
follower arm pivot to create a larger angle of rotation and
recalibrate. The minimum angle of rotation should be
greater than 15 degrees. Briefly pressing the QUICK-
CAL/ACCEPT button acknowledges a small range and the
positioner will operate using the short stroke calibration if
otherwise a good calibration.
RGGR
●
●●
●
INNER LOOP OFFSET TIME OUT
Description: During calibration the Inner Loop Offset (ILO)
value did not settle. This could result in less accurate
positioning.
Possible Solutions: Repeat the stroke calibration to get a
more accurate ILO value. To proceed using the less
accurate ILO value, this error may be cleared by briefly
pushing the QUICK-CAL/ACCEPT button. Lowering the
setting on the gain selection switch may help if the actuator
is unstable during the calibration.