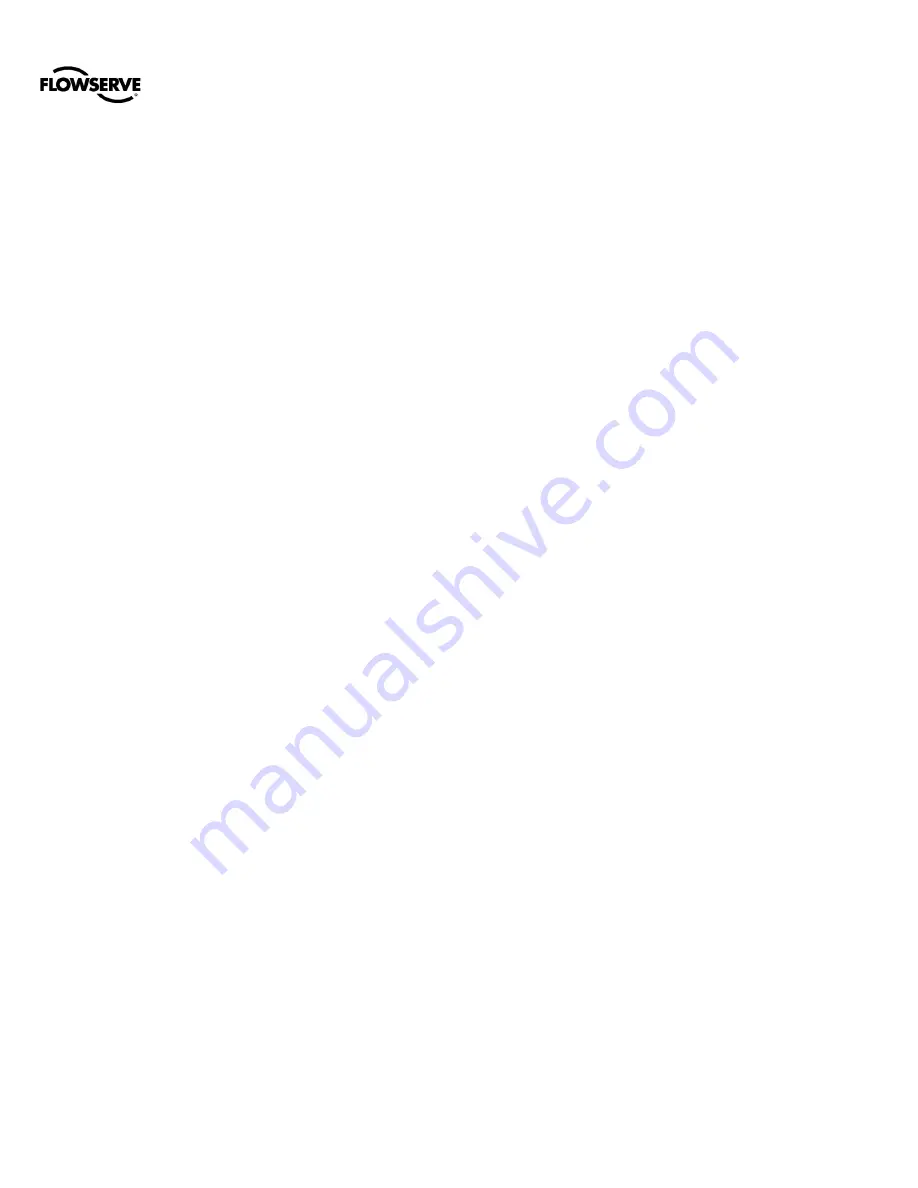
Logix
®
Digital Positioners FCD LGENIM0110-0 05/16
flowserve.com
46
checking linkages for wear, misalignment, and tightness.
Bellows inspection may include checking bellows for
cracking or leaking. Actuator inspection may include
checking the actuator seals and lubrication. Relay
inspection may include checking for high air consumption
and signs of wear on the spool. After maintenance, reset
the travel accumulator.
YGYY
●
●
●●
POSITION AMPLITUDE WARNING
POSITION FREQUENCY WARNING
Description: The amplitude or frequency of the position
signal is above the warning limit. The positioner is
controlling the position of the valve with large or rapid
corrections.
Possible Solutions: Verify the limits are set at an
appropriate level. Adjust the selectable Gain switch to a
lower setting or use the Hi Friction setting. Perform a
QUICK-CAL which sets the gains based on valve
response. Check for high friction. If the problem persists
replace the relay.
YGYR
●
●
●
●
COMMAND AMPLITUDE WARNING
COMMAND FREQUENCY WARNING
Description: The amplitude or frequency of the command
signal is above the warning limit. This could mean the
control loop has larger swings or is oscillating faster than
desirable.
Possible Solutions: Verify the limits are set at an
appropriate level. Review the control loop parameters and
equipment. Adjust as necessary.
YGRY
●
●
●
●
CONTINUOUS STROKE TEST FAILED WARNING
Description: During the continuous stroke test, the valve did
not move after 5 consecutive attempts. This could mean
the valve has increased friction, a change in process load
or inadequate supply pressure.
Possible Solutions: Check friction, supply pressure and
other alarms or warnings that would indicate difficulty in
moving the valve. Check packing, and air supply. The
warning will clear when the CST function is turned off or
when a successful attempt to move the valve occurs.
YGRR
●
●
●●
PARTIAL STROKE TEST FAILED WARNING
Description: Measured times or forces during the last
partial stroke test did not pass the criteria set by the user.
This may be an indication of corrosion build-up on the valve
stem or in the actuator, low or restricted supply pressure, or
a sticking positioner relay.
Possible Solutions: This warning will clear upon completion
of a successful partial stroke test.
YYGG
●●
●●
TEMPERATURE HIGH WARNING
TEMPERATURE LOW WARNING
Description: The temperature of the internal electronics has
exceeded the manufacturer set limits of -40°C (-40°F) to
85°C
(176°F).
Low
temperature
may
inhibit
responsiveness and accuracy. High temperature may
affect performance or limit the life of the positioner.
Possible Solutions: Regulate the temperature of the
positioner by shading or cooling supply gas. Heat the
positioner if needed. If the temperature reading is in error,
replace the main board.
YYGY
●●
●
●
VALVE CLOSED TOO FAR WARNING
VALVE OPENED TOO FAR WARNING
Description: While the valve was in use, it closed or opened
farther than it did at the last calibration by 0.5%.
Possible Solutions: Check the feedback arm linkage and
ensure the valve stem connection is tight. Recalibrate the
stroke. If the process cannot be interrupted a service
technician may be able to adjust the calibration.
YYGR
●●
●
●
SUPPLY PRESSURE HIGH WARNING
Description: The supply pressure is above the user set
warning limit. Supply pressure that exceeds the maximum
rating on the actuator can become a potential hazard.
Possible Solutions: Regulate the supply pressure at the
positioner below the maximum limit recommended for your
actuator. Recalibrate pressure sensors. Check the
pressure sensor board connections. Replace pressure
sensor board if necessary.
YYYG
●●●
●
SUPPLY PRESSURE LOW WARNING
Description: The supply pressure is below the user set
warning limit. Low supply pressure can cause poor valve
response
or
positioner
failure.
The
minimum
recommended supply pressure for proper operation is 1.3
bar (19 PSI).
Possible Solutions: Regulate the supply pressure at the
positioner above 1.3 bar (19 PSI). Ensure system air/gas
supply is adequate. Repair kinked or restricted supply
tubing. Check for pneumatic leaks in the actuator and
actuator tubing. Recalibrate pressure sensors. Check the
pressure sensor board connections and replace pressure
sensor board if necessary.