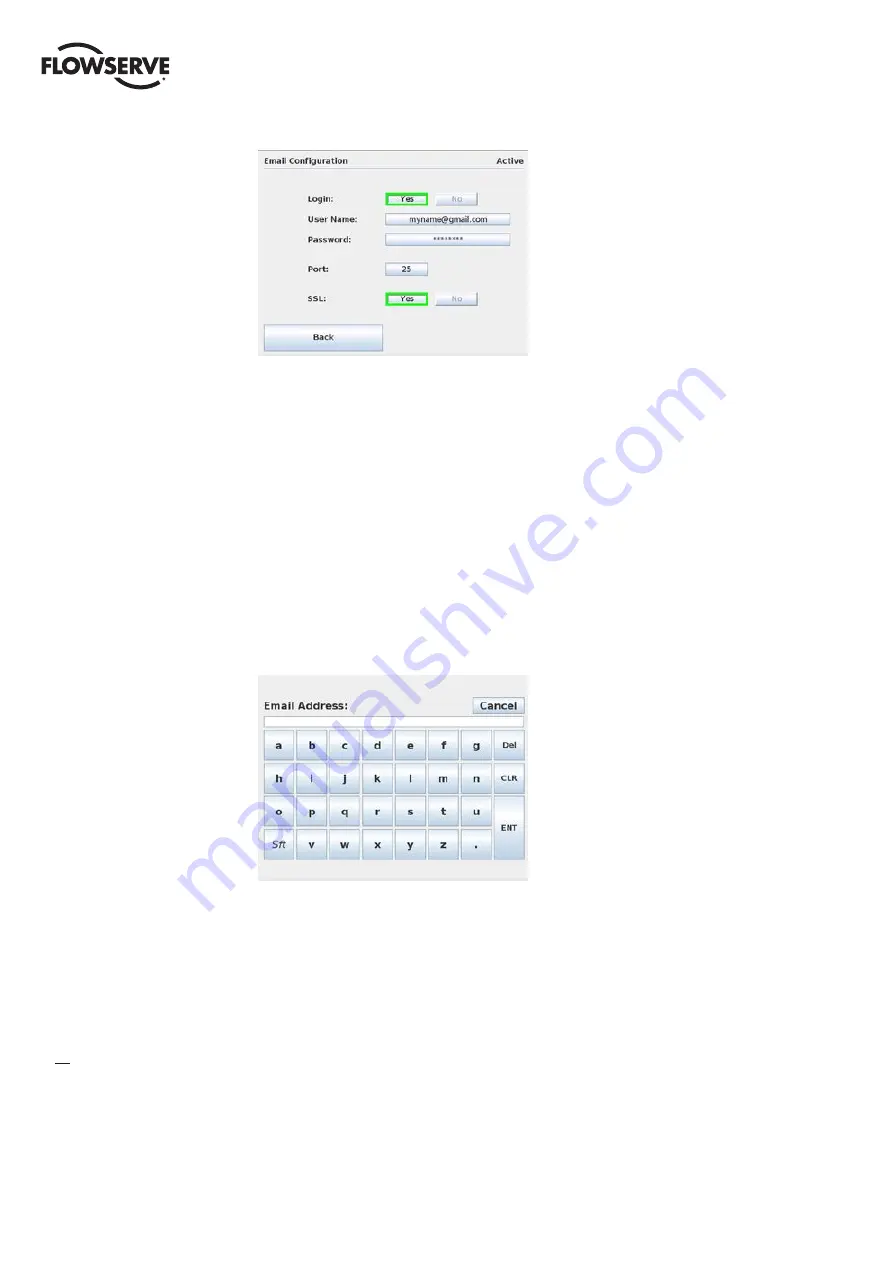
Limitorque Master Station III FCD LMENIM5001-02 – 12/13
28
Figure 7.5 - SMTP Configuration with Password
Once the SMTP Host Address and SMTP Email Account have been configured, the IP address of the
Master Station III must be set in the Email Notification Screen. Set the Primary and Secondary DNS
addresses by selecting the octet fields.
7.2.2 Alarm Listener Configuration
Once the SMTP configuration has been completed, alarm listeners can be added to the email notifica-
tion system so that email alerts are sent when any of the following network events occur: Network
Fault, DCS Port Fault, Emergency Shutdown, Hot Standby Change, or MOV Alerts. Any or all of the
Master Station III events can be selected for each individual listener.
To add an event listener, click the “Add” button on the Email Notification Screen and enter the desired
email address as shown in Figure 7.6.
Figure 7.6 - Add Email Listener