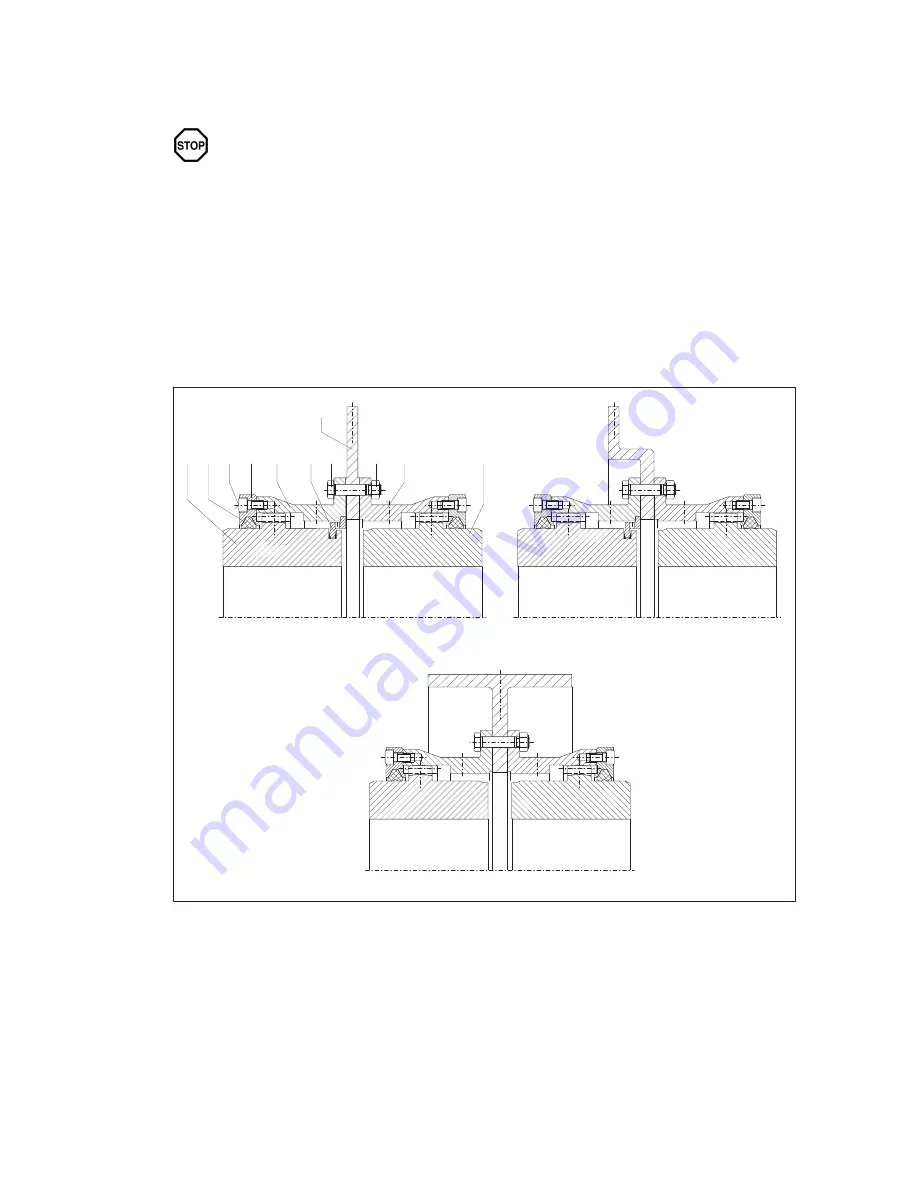
16
ZAPEX 3502 en
Operating instructions 10/2017
5.
Technical description
Observe the instructions in section 3, "Safety instructions"!
If a dimensioned drawing has been made out for the coupling, the data in this drawing
must be given priority.
5.1
General description
ZAPEX type ZWBT, ZWBG, ZWB, ZWH and ZWHD couplings are provided for connecting two shafts. The
shaft ends to be connected must be supported immediately upstream of and downstream of the coupling.
ZAPEX couplings are suitable for clockwise and anticlockwise rotation and reversing operation.
The coupling parts (1, 2) with external teeth engage with the internal teeth of the flanged sleeves (5) and/or
coupling sleeve (5).
For the types ZWBT, ZWB, ZWBG and ZWH, DUO sealing rings (12) are used on the outside for sealing
the oil chambers.
5.1.1
Types ZWBT, ZWBG, ZWB
1 12 11 10
5
8
9
6
2
ZWBG
52
13
ZWBT
ZWB
(7)
Torque transmission is effected from the shaft over parallel key, shrink fit or a comparable connection to
the coupling part (1), then over the tooth system to the sleeve (5) and then via the fitting-screw
connection (8, 9) to the second sleeve (5), over the tooth system to the coupling part (2) and then again
via the parallel key, shrink fit or a comparable connection to the shaft. The brake disk (13) is located
between the flanged sleeves (5).
In case of types ZWBT and ZWBG the axial backlash is restricted by the twopart retaining ring (52).
Summary of Contents for Zapex ZWB
Page 2: ......