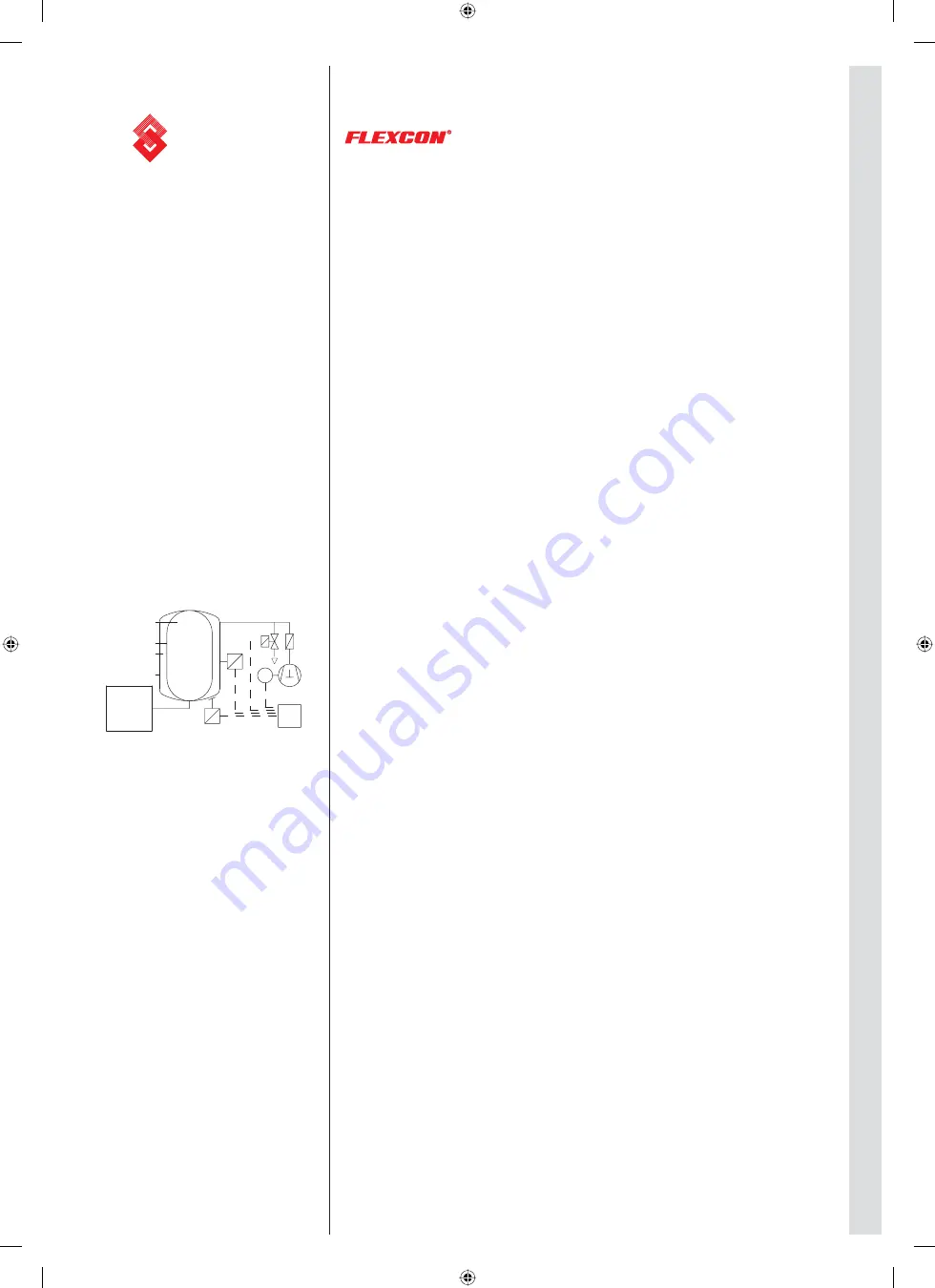
3
&LAMCO
M-K Compressor Expansion Automat
Installation and operating instructions
Transport
(continued)
Once the automat has been removed from its packaging, it must be set up under safety measures
to avoid being damaged, tipped or shaken. Only use permitted load lifting devices.
Depending on the transport method and the size of the expansion automat, various types of
packaging may be used.
Unless otherwise contractually agreed, the packaging meets the packaging guidelines of
Flamco STAG GmbH.
Storage
Interim storage can also take place while packed. Conditions for this are: a closed, frost free room
(dry..60...70 % relative humidity), free of vibrations, protected against heat and direct sunlight.
Vessels or equipment parts that have been removed from the packaging must be placed in their
fi nal position.
The stability is to be ensured and the stacking of equipment should be avoided.
3. Product description
Methodology
(Symbol)
Changes in the volume of the operating water
)a*
caused by temperature changes in closed
heating or climate control systems generate different levels in the water compartment of the
expansion automat. The pressure in the gas compartment of the automat caused by this is a
measurable value that is continuously recorded by a pressure sensor and transmitted via a signal
cable to a control unit.
In the event of any difference, a comparison of these actual values with the programmable
nominal values leads to the control of a compressor or pressure relief valve, which is linked with
the gas compartment by a common pressure control tube.
In this way, the valve is opened as the level increases during system heating to relieve pressure
(pressure reduction) and the compressor is switched on as the system cools and the level falls
(pressure increase).
A hystereses
)b*
may be set for controlling the valve or compressor, which ensures the
maintenance of the set system pressure of a heating or climate control system with a modifi able,
small tolerance.
The levels recorded by a level sensor and assessed by the controller result, as in the case of the
system pressure, to display values and once limit values have been reached, to control signals
that enable an additional evaluation or the actuation of other units.
By choosing different nominal sizes of vessel, the option to connect several vessels, the selection
of different compressor capacities or operating modes and by changing the nominal values, the
M-K compressor- expansion automats can be adjusted to the operating behaviour of a heating or
climate control system.
)a*
Water types whose constituent materials do not pose any hazard to the operational readiness
and do not damage or improperly infl uence (e.g. heating water) water-keeping parts of the
Automat (e.g. pressure-bearing components, diaphragm, vessel connection,...)
)b*
Switch difference to the nominal value, only changes to the nominal value can be assessed.
Small hystereses: the advantage is a small deviation from the nominal value, the disadvantage
is a high switch frequency.
Large hystereses: the advantage is a low switch frequency, the disadvantage is a large deviation
from the nominal value.
The programmable setting range on the M-K expansion automat, this switch difference,
is 0.1 – 0.5 bar for as well the compressor (pressure increase), as for the pressure relief valve
(pressure reduction). Standard models have a preset of 0.2 bar (total lag of 0.4 bar).
Equipment
The equipment components of the M-K expansion automat meet the safety requirements of the
relevant EC directives and the specialist standards to be applied.
Compliance is confi rmed by means of conformity declarations.
The construction of the pressure vessels is designed in accordance with Directive 97/23/EC
)c*
and under consideration of the German AD Information Sheets
)d*
.
Examination and cleaning openings for inspections are provided on the basis of practical
experience (taking German standards into consideration).
The conformity label CE0045 (on the type plate) identifi es the Notifying Body at which the conformity
evaluation process according to Article 10 of this Directive has been tested and confi rmed.
In line with the scope of use according to regulations, the corrosion allowance is 0 mm.
This allowance may be higher , depending on the order.
)c*
Directive of the European Parliament and Council for the harmonisation of legal provision of
member states on pressure devices. Offi cial Journal of the European Communities L181.
)d*
Technical safety requirements for normal operation conditions, prepared by the
associations that cooperate in the Arbeitsgemeinschaft Druckbehälter (AD).
Published by: Verband der technischen Überwachungs- Vereine e.V., 45038 Essen.
Pressure vessel
Diaphragm
(Gas pressure)
Gas compartment
Symbol
Heating
Water compartment
(Water pressure)
sensor
Pressure
or climate
control
system
Compressor
Controller
M
sensor
Level
Valve
18502426 broch Flexcon M-K_UK.indd 3
18502426 broch Flexcon M-K_UK.indd 3
13-07-2006 08:55:25
13-07-2006 08:55:25