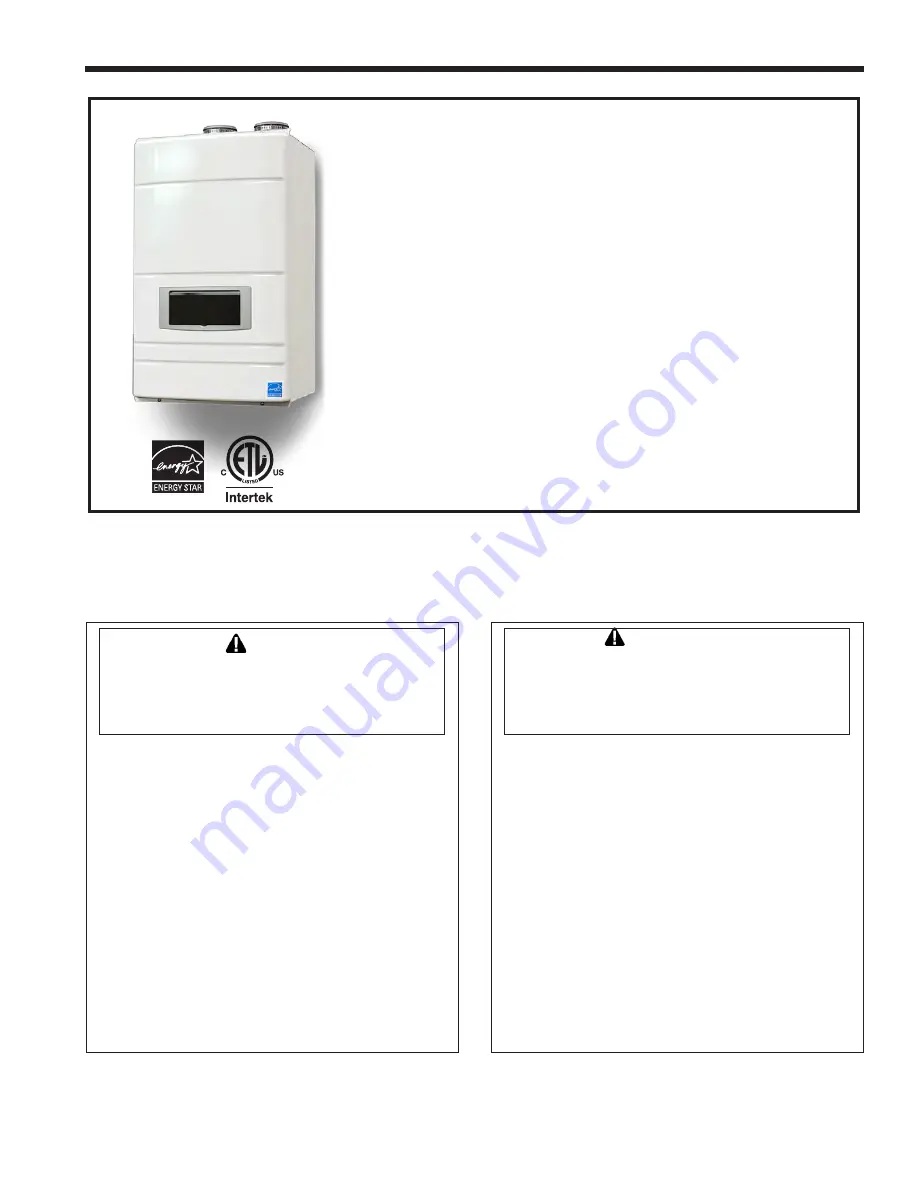
Installation and Operation Instructions
Document 1318G
H2372800G
WARNING
If the information in this manual is not
followed exactly, a fire or explosion may
result causing property damage, personal
injury or loss of life.
Do not store or use gasoline or other
flammable vapors and liquids in the vicinity of
this or any other appliance.
WHAT TO DO IF YOU SMELL GAS
• Do not try to light any appliance.
• Do not touch any electrical switch; do not
use any phone in your building.
• Immediately call your gas supplier from a
nearby phone. Follow the gas supplier's
instructions.
• If you cannot reach your gas supplier, call
the fire department.
Installation and service must be performed
by a qualified installer, service agency, or gas
supplier.
FOR YOUR SAFETY:
This product must be installed and serviced by a professional service technician,
qualified in hot water boiler and heater installation and maintenance. Improper installation and/or operation
could create carbon monoxide gas in flue gases which could cause serious injury, property damage, or
death. Improper installation and/or operation will void the warranty.
AVERTISSEMENT
Assurez-vous de bien suivres les instructions
données dans cette notice pour réduire au
minimum le risque d’incendie ou d’explosion
ou pour éviter tout dommage matériel, toute
blessure ou la mort.
Ne pas entreposer ni utiliser d’essence ou ni
d’autres vapeurs ou liquides inflammables dans
le à proximité de cet appareil ou de tout autre
appareil.
QUE FAIRE SI VOUS SENTEZ UNE ODEUR DE
GAZ:
• Ne pas tenter d’allumer d’appareils.
• Ne touchez à aucun interrupteur. Ne pas vous servir
des téléphones dans le bâtiment où vous vous
trovez.
• Appelez immédiatement votre fournisseur de
gaz depuis un voisin. Suivez les instructions
du fournisseur.
• Si vous ne pouvez rejoindre le fournisseur de
gaz, appelez le sservice des incendies.
L’installation et l’entretien doivent être assurés par
un installateur ou un service d’entretien qualifié
ou par le fournisseur de gaz.
Installation and Operation
Instructions for
Wall-Mounted, Modulating
Gas, Condensing, Combination Boiler
Model FTCW
140,000 BTU/hr
199,000 BTU/hr
•
Natural Gas (NG) - Factory Configuration
•
Propane Gas (LP) - Field-Convertible
THE
FT
SERIES
Summary of Contents for FT Series
Page 50: ...Page 50 4 22 Ladder Diagram F B level Air Pressure Sensor...
Page 66: ...Page 66 6 2 Fault Tree Analysis 1 Flame detection...
Page 81: ...Mascot FT Combination Boiler Page 81 Heat Exchanger Tank _ Feature Heat Exchanger Tank FTCW140...
Page 83: ...Mascot FT Combination Boiler Page 83 Fan Gas Valve _ Feature Blower and Gas Valve FTCW140...
Page 85: ...The FT Series Wall Mounted Combination Boiler Page 85 FTCW199...