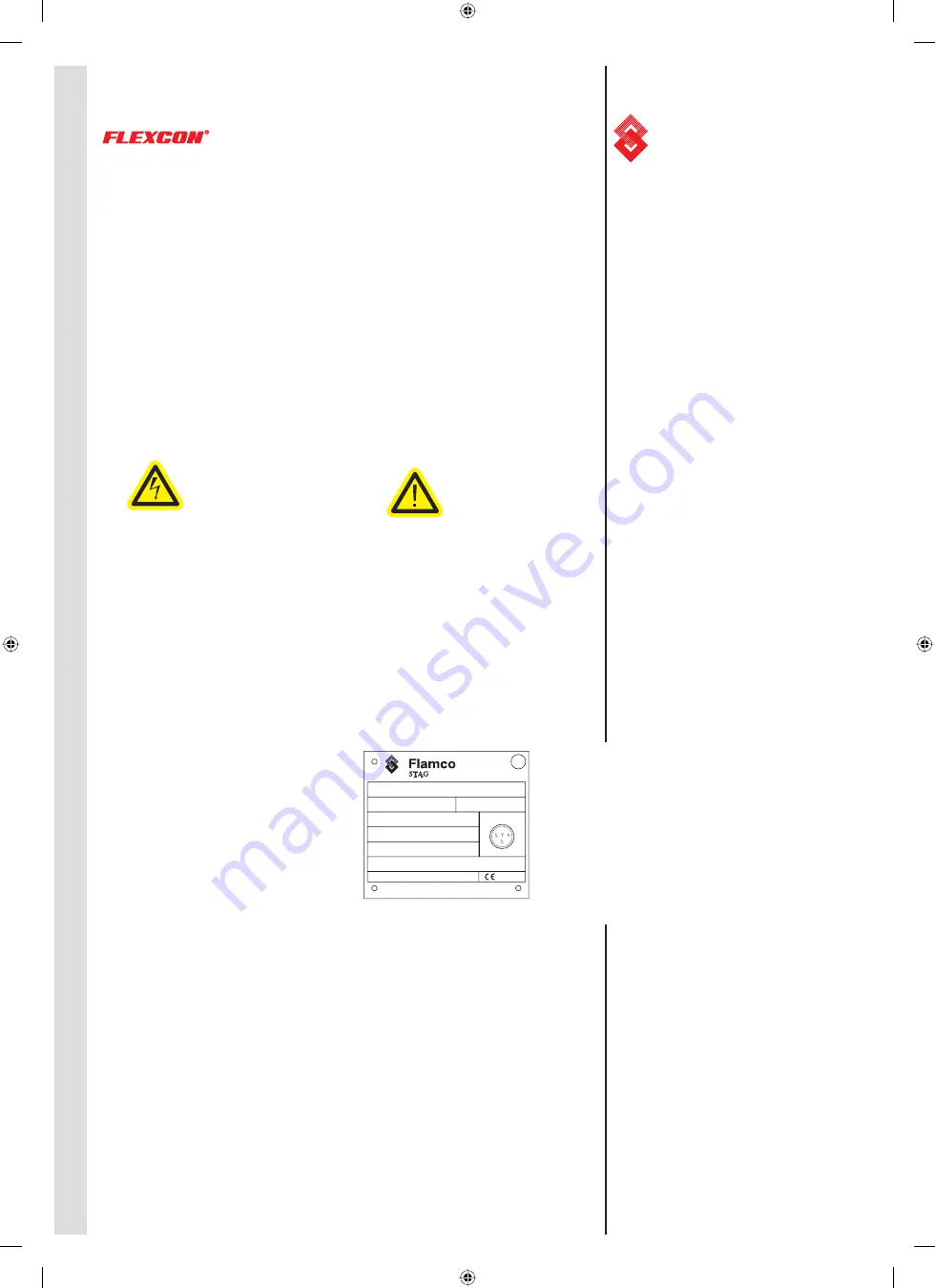
2
&LAMCO
M-K Compressor Expansion Automat
Installation and operating instructions
1. Exclusion of liability
All the technical information, data and instructions contained in these operating instructions for
operations that can and are to be performed, are up to date at the time of editing.
They contain our current knowledge and experience to the best of our understanding.
We reserve the right to make technical modifi cations arising from the further development of the
Flamco product presented in these operating instructions. For this reason, no claims may be
derived from technical data, descriptions and illustrations.
Required operations within the scope of Flamco delivery must be performed by trained
and certifi ed specialists. This includes such persons having knowledge of applicable safety
conditions. Consequently, Flamco shall not be liable for any losses, subsequential losses,
personal losses arising from the non-observance of safety conditions or as a consequence of the
disregard of standard precautionary measures when performing such services as transport,
installation, commissioning, re-starting, operation, maintenance, testing and repair, even in the
event that these are not expressly described in these instructions.
Technical illustrations, drawings and graphs may not necessarily represent the actual module,
individual components or spare parts supplied.
Drawings are not to scale and contain symbols for the purpose of simplifi cation.
-Reference symbols used in the instructions.
Hazardous voltage
Ignoring this can put your life in
jeopardy, cause fi res or accidents
destruction
For special consideration
Ignoring this may result in
reduced functioning ,overload
or destruction
2. Acceptance of goods
Inspection
The items supplied (equipment, documentation) are listed in the shipping papers.
The contents of the delivery must be immediately checked for completeness and transportation
damage upon arrival.
Incorrect or missing items must be immediately identifi ed. Please note the contents (e.g., for
handling goods, notifi cations of defects...) of the general terms and conditions contained in the
shipping papers.
Compare the specifi cations on the type plate of the expansion vessel with the specifi cations of
your order or the details of the relevant project.
If this expansion vessel is used regardless of any differences which have been ascertained (not
used in accordance with regulations), it will not be possible to exclude system faults or hazards to
people, animals or objects.
Type plate
- Gas pre-charge mark.
The expansion vessel (basic and ancillary vessel) is under pressure on delivery, which, in
standard situations, is an overpressure of 2.0 bar. This value may be smaller, depending on the
order. The information is at eye-level on the operating side (user position).
(Changes in ambient temperature can cause variations in the pre-charge.)
Transport
The basic and ancillary vessels of the unit are packed horizontally on disposable pallets and
delivered fully assembled. Accessories or add-on equipment (e.g. Compressor Unit K04) can be
packed separately or as a part of the automat unit packaging. The disposable pallets are suitable
for horizontal transport using permitted forklift devices (e.g. forklift trucks, forklift stackers...).
Always use the largest possible fork size for the pallet to prevent the load from tipping over.
Position the object to be moved as low as possible, at right angles to the forks.
Hoist fi ttings on the vessel (welded lifting lugs) are to be used for lifting of the empty, uninstalled
vessel that has been removed from its packaging.
Note:
The transport guard (Pos. 46, page 4) provides necessary protection against collision during
the setup of the expansion automat and must only be removed once this is complete!
(Installation surface, setup, page 9)
M
an
uf
ac
turer’s ma
rk
in
g
H
ers
tellerk
ennze
ich
en
M
a
rq
ue
d
ist
inct
ive du co
ns
tru
ct
eu
r
0045
:
:
:
Herstellungsjahr
Year of manufacture
Année de fabrication
:
:
:
:
:
:
:
:
:
:
:
:
:
:
:
:
:
:
°C
Flamco STAG GmbH
39307 Genthin
GERMANY
Liter
litre
Zulässige Betriebstemperatur min. / max.
Permissible working temperature min. / max.
Prüfüberdruck
Test overpressure
Zulässiger Betriebsüberdruck
Permissible working overpressure
Nenninhalt
Nominal volume
Serien-Nr.
Serial-No.
Typ
Type
bar
bar
litres
N° de série
Capacité nominale
Surpression d`essai
Surpression de service admissible
Température de service mini. / maxi. admissible
Type
Conformity mark
Manufacturer’s mark
Respective year of manufacture
Permitted operating temperature of the expansion vessel
Permitted test overpressure of the expansion vessel
Permitted operating overpressure of the expansion vessel
Nominal capacity of the expansion vessel
Serial (production) number of the expansion vessel
Type rating of the expansion vessel
Manufacturer’s logo
Manufacturer’s address
18502426 broch Flexcon M-K_UK.indd 2
18502426 broch Flexcon M-K_UK.indd 2
13-07-2006 08:55:24
13-07-2006 08:55:24