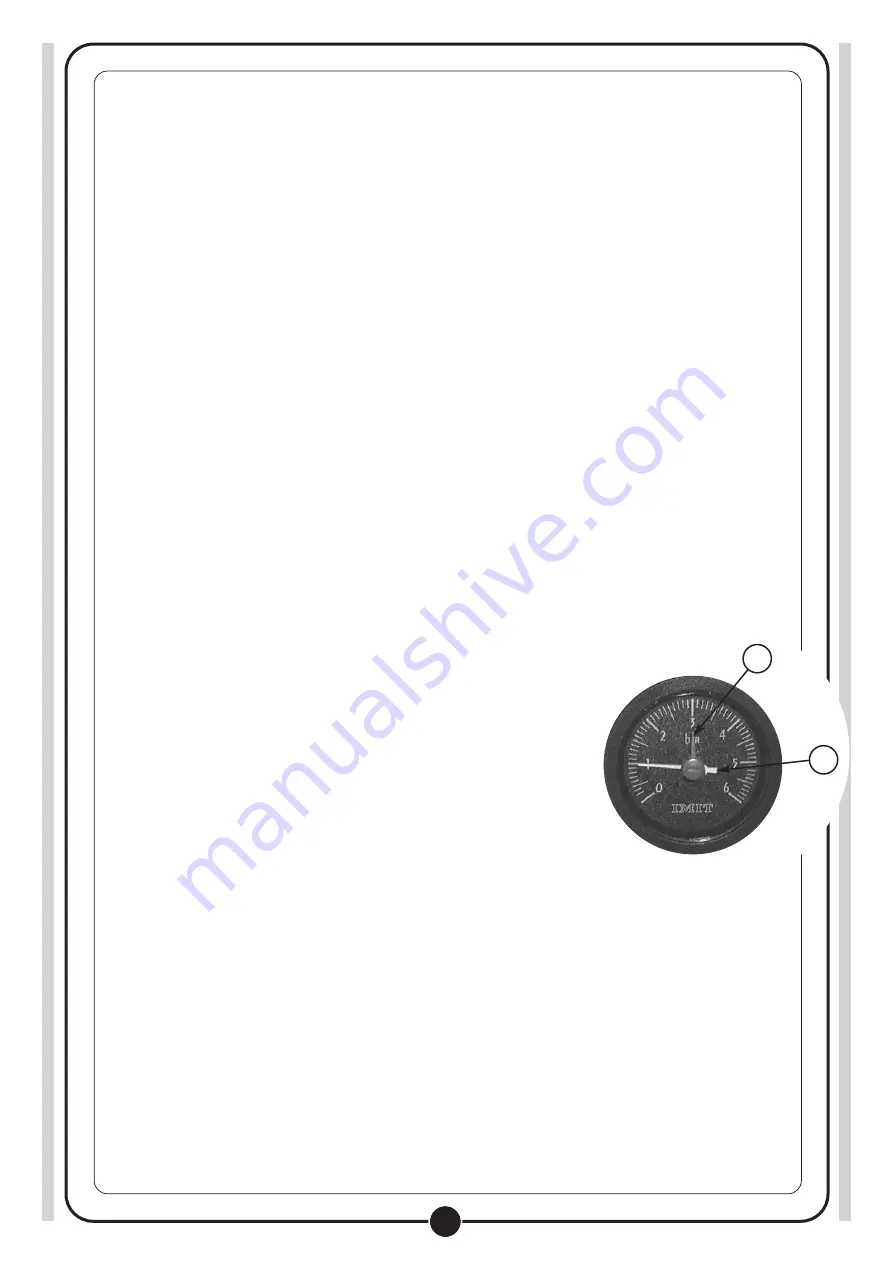
SYSTEM FILLING, TESTING AND COMMISSIONING
* Before proceeding to filling, ensure that electricity supply is switched off at mains
to avoid any possibility of time switch operating and passing power to appliance
prior to filling.
Filling and Testing
Check that
all
connections, especially compression joints, are fully tightened. Re-check and
ensure that pressure vessel air charge is correct, then fill system with water via filling system
used.
Turn off water supply before system pressure reaches safety valve operation point of
3 bar
. (Say 2 to 2.5 bar). Vent system via all manual air vents
including circulating pumps
,
boiler, radiators, system high points. etc. Check that dust caps are loosened on auto air vents,
keep constant check on system pressure gauge (fitted to control panel). If pressure has dropped
readmit water to above pressure. Ensure
all
appropriate boiler and system valves
are open
.
With water supply turned off,
thoroughly
flush out boiler and system to remove
all
foreign
matter before allowing boiler and pumps to operate. If in doubt drain system and repeat above
procedure. At this stage flushing-out water should be clean and clear of all foreign
matter.
Refill the system and again vent at all points as described above. Examine the complete system
for water leaks having pressurised it to 1.5 - 2.5 bar. Correct any leaks, then check operation of
safety valve by admitting further water until this valve operates. This should occur when system
pressure rises to between 2.7 and 3.3 bar. When satisfied with valve operation, and with mains
water still turned off, draw off sufficient water until initial system design fill pressure (Pi). (cold
fill) is established (0.5 - 1.5 bar - as calculated for system). The red pointer B
on pressure gauge should then be set at this initial system design pressure
(Pi), i.e. system static head +0.3
Remember that initial cold fill pressure can only be checked when
system water has properly cooled down. Check that
final
operating pressure
(Pf) is under 2.5 bar with
all
radiators turned
on and up to highest working temperature. Should system
operating pressure exceed this, check:
1.
That initial cold fill pressure is correct and , if additional
expansion vessel is fitted, that pressure is equal in each vessel,
2.
That expansion vessels are sized correctly.
Special attention should be given to existing heating systems where a Firebird boiler
has replaced an existing unit. Extra effort should be made to ensure that all original pipe
work and radiators are repeatedly flushed. If possible use a proprietary cleansing agent
suitable for system as loosened scale and foreign matter canseriously reduce domestic
hot water performance and pump efficiency.
Use corrosion inhibitor of suitable type.
36
B
A
Summary of Contents for HEAT PAC 120/150
Page 2: ......
Page 15: ...4 FLUE SYSTEMS 13...
Page 24: ...8 FAULT FINDING 22...
Page 25: ...8 FAULT FINDING 23 T Repair or Replace Oil Pump r No...
Page 30: ...9 TECHNICAL SPECIFICATION 28 9 D E Riello Burner Specification...
Page 33: ...System Oil Boiler PART 2 System Filling and Testing 31...
Page 39: ...37 System Oil Boiler PART 3 Spare Parts...
Page 54: ...NOTES...