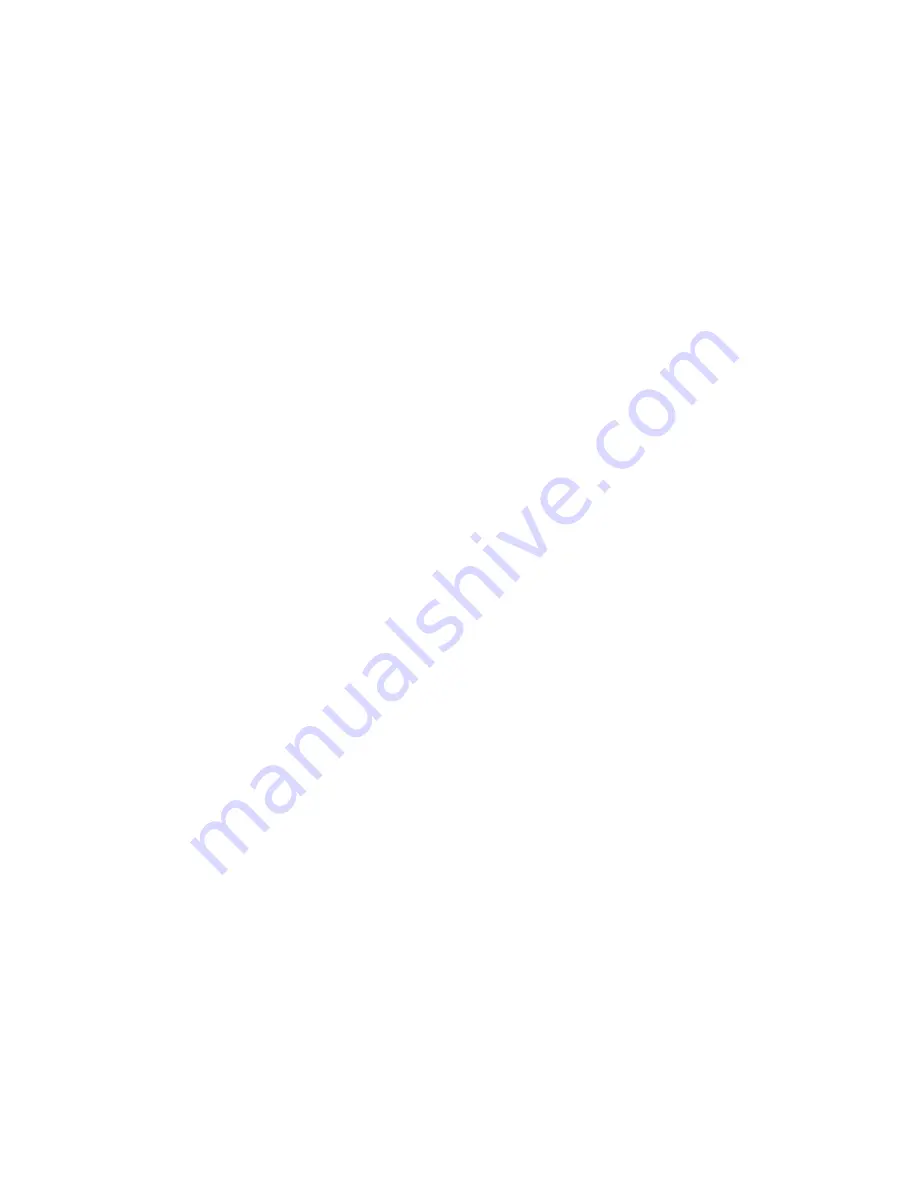
12
The airlock receives the material from the drag conveyor and pressurized air from the blower. Its primary
function is to convey the material from the atmospheric air to a sealed chamber where the blower air picks it
up and blows it out of the hose. To enable the Bark Blower to convey fibrous material, the airlock housing
is equipped with two sharp cutting knives, and the vanes on the rotor are angled and hardened. If any long
material should protrude above a vane, it will be sheared off before the vane enters the close tolerance of the
housing. The airlock rotor is direct-coupled to a bi-rotational hydraulic motor and gearbox.
SUBSYSTEM 2: HYDRAULIC SYSTEM
Hydraulic power for the Bark Blower is generated by a flow and pressure compensated, load-sensing pump
driven off of the engine auxiliary drive. This means the pump can measure how much load is on the hydrau-
lic circuit and will only pump the oil needed to satisfy the demands of the circuit. The pump receives DTE-
13m hydraulic fluid from the 36 gallon (136 liter) reservoir through a service valve and suction hose, and
delivers it to the valve manifold. The manifold is one block of machined aluminum, equipped with valve
cartridges and solenoids that control all the functions of the Bark Blower.
Two pressure gauges at the valve manifold read the valve inlet pressure (left/rear gauge) and the load-sense
pressure (right/front gauge). The L/R gauge should always read about 300 PSI more than the F/R gauge.
This 300 PSI is called the "margin pressure" and is a measure of the pump's ability to respond to changes
in the hydraulic circuit. If the margin pressure is set too high (over 500 PSI), the pump will be too sensi-
tive and can become unstable. If the marging pressure is too low (below 200 PSI), the pump can become
"lazy" and not provide enough oil flow for the demand. The margin pressure can be adjusted using the
lower compensator adjustment screw in-line with the load sense hose on the back of the hydraulic pump.
The only time the gauges will not show the margin pressure is when one of the hydraulic circuits is stalled,
such as if the floor conveyor somehow became jammed. In this case, both gauges will show the high pres-
sure standby of 2800 PSI until the blockage is removed. High pressure standby is the maximum pressure the
pump will produce. A system relief valve is set for 3500 PSI to protect the system if there is a failure in the
pump compensator.
DESCRIPTION OF VALVE SECTIONS
Figure 3 shows the valve block and the different hydraulic circuits. Each circuit, except for the Hose Reel
(HR) circuit, is controlled by two valves. On the Floor (F) and Air Lock (AL) circuits, the flow rate is con-
trolled by the proportional valves which can be manually stroked by inserting a small rod or screw driver into
the hole in the bottom of the solenoid. The Floor and Air Lock circuits also have a directional valve which
can be manually stroked by pressing the red knob on the bottom of the solenoid. The Agitator (A) and Seed
Injection (S) circuits are controlled by a three position valve that is actuated by one of two solenoids. These
valves can be stroked manually be pressing or pulling on the red knob on the bottom of the solenoid. The
Hose Reel (HR) circuit is controlled by a two position on/off valve and its solenoid can only be actuated in
one direction by pressing on the red knob on the bottom. The flow rates for the Hose Reel, Seed Injection
and Agitator circuits are adjusted using the flow control valves located directly behind the solenoids for their
respective circuits.
Summary of Contents for BARK BLOWER BB-1208
Page 2: ...NOTES...
Page 11: ...5 CURRENT SET OF SAFETY DECALS...
Page 12: ...6 NOTES...
Page 33: ...27 NOTES...
Page 34: ...28 Figure 7 17 16 15 13 12 11 8 7 6 5 4 2 18 8 12 3 14 1 13 1 17 10 9...
Page 36: ...30...
Page 37: ...31 NOTES 31 BARK BLOWER Model 1208 Parts Manual Model SR LBBB1208 SR...
Page 38: ...32 WHEN ORDERING PARTS BE SURE TO STATE SERIAL NUMBER OF MACHINE NOTES...
Page 54: ...48 WHEN ORDERING PARTS BE SURE TO STATE SERIAL NUMBER OF MACHINE 2 1 3 4 2 3 6 3 5 2 7...
Page 66: ...60 WHEN ORDERING PARTS BE SURE TO STATE SERIAL NUMBER OF MACHINE 2 3 5 4 7 7 8 9 6 10 1...