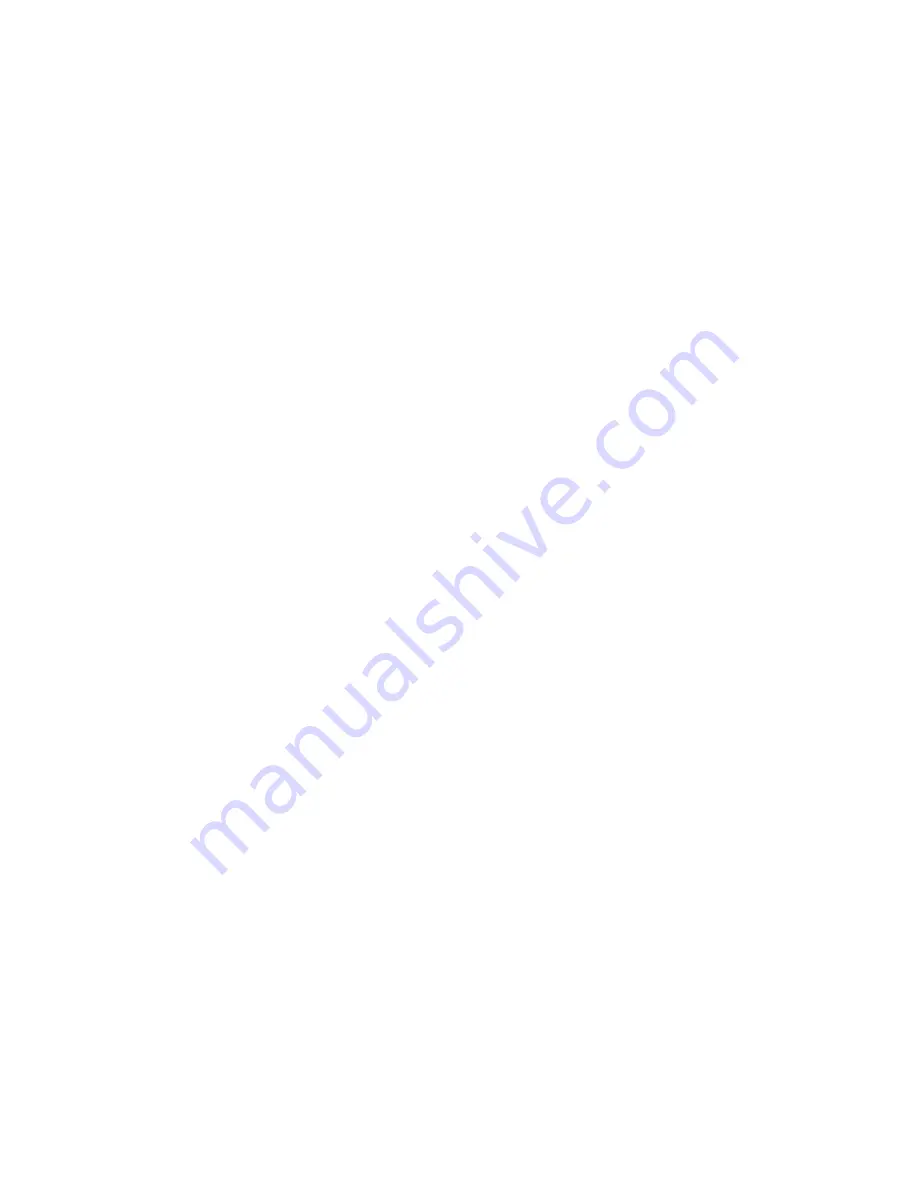
15
2.
Press and hold the small red button, located on top of the Radio Transmitter, until there are
no lights alit on the top of the Radio Transmitter.
3.
Start the engine and allow it to warm up as specified in the Starting Procedure on Page 11.
4.
Place the Radio Transmitter Switch located on the control box to the “ON” position
5.
Press and hold the small red button, located on top of the Radio Transmitter, until both lights
turn on then off.
To utilize the Material Feed Start/Stop feature on the Radio Remote, the initial start must occur at the Start/
Stop station on the Bark Blower. The hard-wired Start/Stop on the unit is the primary and overriding set of
controls. When either the “Stop” button is pushed or a loss of power to safety measures in the PLC system
(i.e. the folding door on the feed roll housing is opened or a circuit breaker trips), the Feed Start/Stop feature
on the Radio Remote is deactivated. This feature will remain inactive until the initial start is once again made
at the machine by pressing the “Start” button.
The Material Increase/Decrease function on the remote can be used to change the floor conveyor speed and
effectively adjust the output of mulch from the machine. Adjustments to the floor speed made from the remote
control will be shown on the control box “Main Menu” screen and the “Speed” screen.
The Engine Increase/Decrease function on the remote adjusts the throttle on the engine. For use of the engine
RPM function refer to “Mulching with the Bark Blower” below.
Pushing the large red “E-Stop” button on the Radio Transmitter activates the shutdown system. This will shut
off the engine, automatically return the engine throttle back to idle and cut power to all the hydraulic valve
solenoids. To reset the safety system:
1. Turn and release the “E-Stop” button on the Radio Transmitter
2. Re-start the engine
3. Start the engine and allow to warm up as specified in the "Starting Procedure" on (page 11).
MULCHING WITH THE BARK BLOWER:
1. Check all areas listed under “Pre-Start Equipment Check” (page 10).
2. Start the engine following all the steps listed under “Starting Procedure” (page 11).
3. Set the floor speed and airlock speed control to the desired operating speed or select one of the saved
programs.
4. Open the gate to the maximum opening.
5. Put the drag conveyor floor switch to the ON position.
6. To activate the dust control system, select the dust control setting on the Options screen. The dust
control system will only operate when the floor switch is in the ON position. The needle valve
above the airlock discharge pan can be adjusted for varying flow.
7. Press the "Start" button on the main control panel to activate the material start/stop feature on the
remote and at the same time press the material stop on the remote. Remote functions are now active
and the clear remote feed standby light should be on.
8. Increase the throttle to full.
9. With a firm grip on the end of the hose, press the material start button on the remote.
10. Floor speed can be adjusted for the desired flow. Watch for auto-reversing of the air lock as well as
shock waves through the hose. Listen for the relief on the blower. Partial plugging in the airlock
discharge or hose may cause it to open, causing a high pitched whine, indicating over-feeding of the
airlock.
11. Use the engine RPM button on the remote to decrease and increase air and material flow. A lower
engine RPM may require a lower floor speed to avoid auto-reversing or plugging.
12. At the end of the load, hit material stop and shut down the engine.
Summary of Contents for BARK BLOWER BB-1208
Page 2: ...NOTES...
Page 11: ...5 CURRENT SET OF SAFETY DECALS...
Page 12: ...6 NOTES...
Page 33: ...27 NOTES...
Page 34: ...28 Figure 7 17 16 15 13 12 11 8 7 6 5 4 2 18 8 12 3 14 1 13 1 17 10 9...
Page 36: ...30...
Page 37: ...31 NOTES 31 BARK BLOWER Model 1208 Parts Manual Model SR LBBB1208 SR...
Page 38: ...32 WHEN ORDERING PARTS BE SURE TO STATE SERIAL NUMBER OF MACHINE NOTES...
Page 54: ...48 WHEN ORDERING PARTS BE SURE TO STATE SERIAL NUMBER OF MACHINE 2 1 3 4 2 3 6 3 5 2 7...
Page 66: ...60 WHEN ORDERING PARTS BE SURE TO STATE SERIAL NUMBER OF MACHINE 2 3 5 4 7 7 8 9 6 10 1...