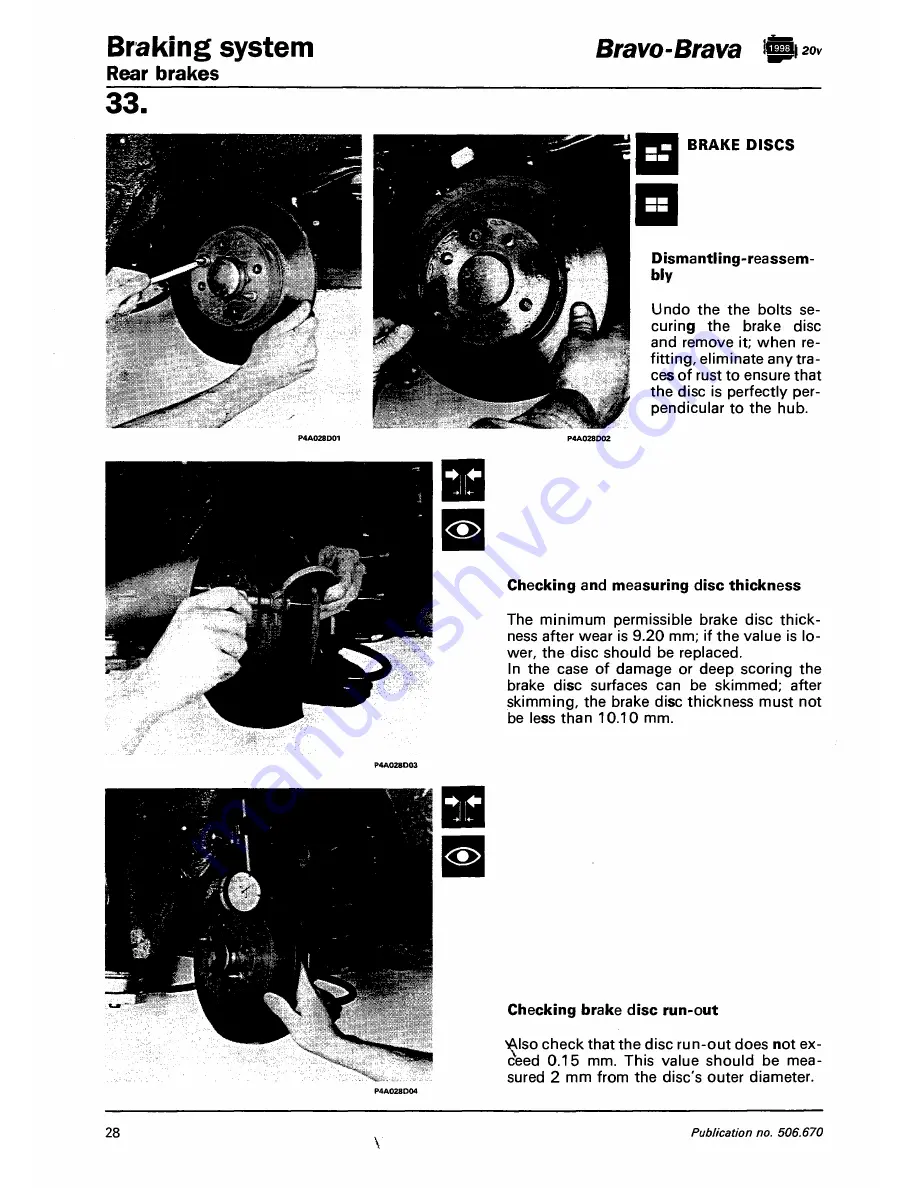
B r a k i n g s y s t e m
Rear brakes
Bravo-Brava
ft**
33-
BRAKE DISCS
Dismantling-reassem-
bly
Undo the the bolts se-
curing the brake disc
and remove it; when re-
fitting, eliminate any tra-
ces of rust to ensure that
the disc is perfectly per-
pendicular to the hub.
Checking and measuring disc thickness
The minimum permissible brake disc thick-
ness after wear is 9.20 mm; if the value is lo-
wer, the disc should be replaced.
In the case of damage or deep scoring the
brake disc surfaces can be skimmed; after
skimming, the brake disc thickness must not
be less than 10.10 mm.
Checking brake disc run-out
'Also check that the disc run-out does not ex-
ceed 0.15 mm. This value should be mea-
sured 2 mm from the disc's outer diameter.
28
\
Publication no. 506.670
Summary of Contents for 1995 Brava
Page 20: ......
Page 56: ...Technical data Gearbox and differential 00 21 27 Bravo Brava 48 Print no 506 670 70...
Page 58: ...Technical data Gearbox and differential 00 21 27 Bravo Brava 50 Print no 506 670...
Page 100: ......
Page 101: ...Untitled Document Removing Refitting file D Volume 201 engine htm08 07 2006 16 06 14...
Page 232: ...2 CQ 5 C Q E E c L U i f 2 a Z 5 ui o 1 o...
Page 281: ......
Page 350: ......
Page 397: ......
Page 418: ...t...
Page 441: ...Braking system Bravo i g j j u o v...
Page 455: ......
Page 461: ...Bravo Brava Braking system Anti lock braking system 33 P4A05AD02 Copyright Fiat Auto 5...
Page 517: ...Bravo Brava Suspension and wheels Front suspension 44 P4A003G02 Copyright Fiat Auto 3...
Page 523: ...Bravo Brava Suspension and wheels Front suspension P4A009G05 Copyright Fiat Auto 9...
Page 532: ...Suspension and wheels Bravo Brava Rear suspension 44 1 8 Publication no 506 670...