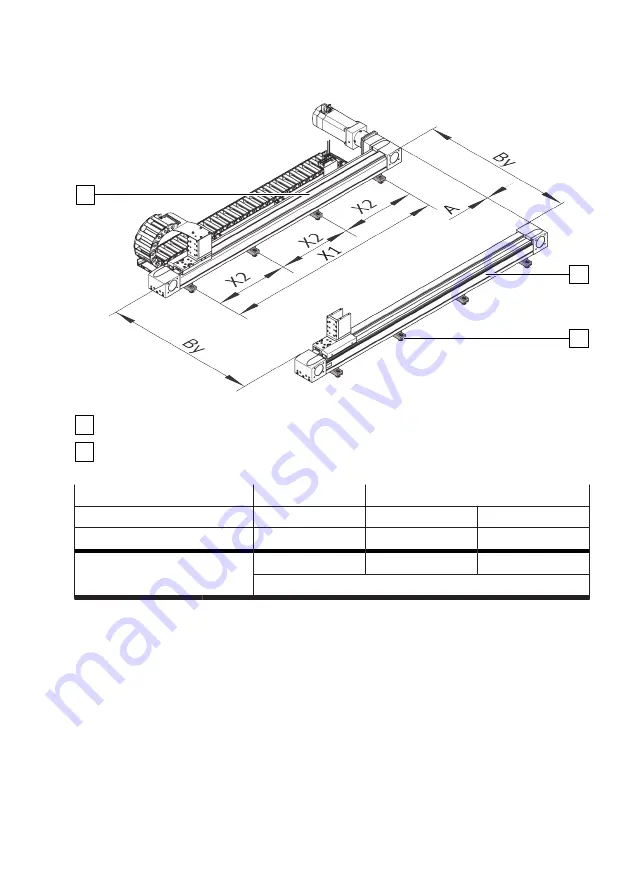
Festo — YXCF — 2021-07b
Assembly
33
1
2
1
Fig. 31: Position of adjusting kits
1
X-axis
2
Adjusting kit
A
Length offset A of the X-axes on the drive
side
Product version
With EGC axes
With ELGC axes
Size
YXCF-1 … 4
YXCF-1-B
YXCF-2-B
X-module
EHMX-EGC-…
EHMX-ELGC-60
EHMX-ELGC-80
Length offset A
[mm]
0
40
46.5
Tolerance ± 0.4 × (By/1000)
Tab. 13: Dimension of length offset A of the X-axes on the drive side