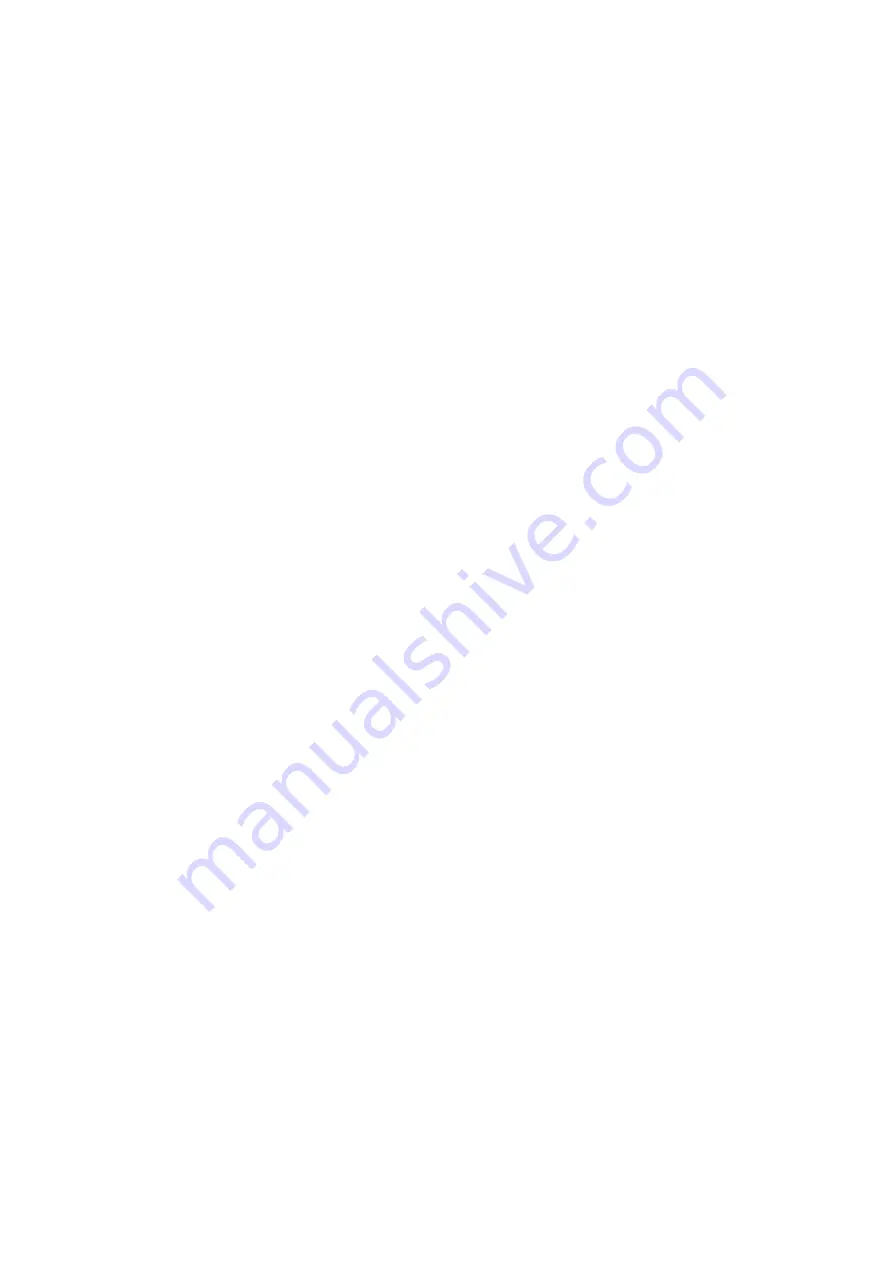
Bottling Learning System
10
© Festo Didactic
696690
3
Intended use
Festo Didactic systems and components must only be used:
•
For their intended use in teaching and training applications
•
When their safety functions are in perfect condition
Festo Didactic systems and components are designed in accordance with the latest technology and
recognized safety rules. However, life and limb of the user and third parties may be endangered and the
components may be impaired if they are used incorrectly.
The Festo Didactic learning system has been developed and produced exclusively for education and training
in the field of automation technology. The training company and/or trainers must ensure that all apprentices
observe the safety precautions described in this workbook.
Festo Didactic hereby excludes any and all liability for damages suffered by trainees, the training company
and/or any third parties, which occur during use of the device in situations that serve any purpose other
than training and/or vocational education, unless such damage has been caused by Festo Didactic due to
malicious intent or gross negligence.
Summary of Contents for MPS PA
Page 6: ...Bottling Learning System 6 Festo Didactic 696690...
Page 65: ......
Page 66: ......
Page 67: ......