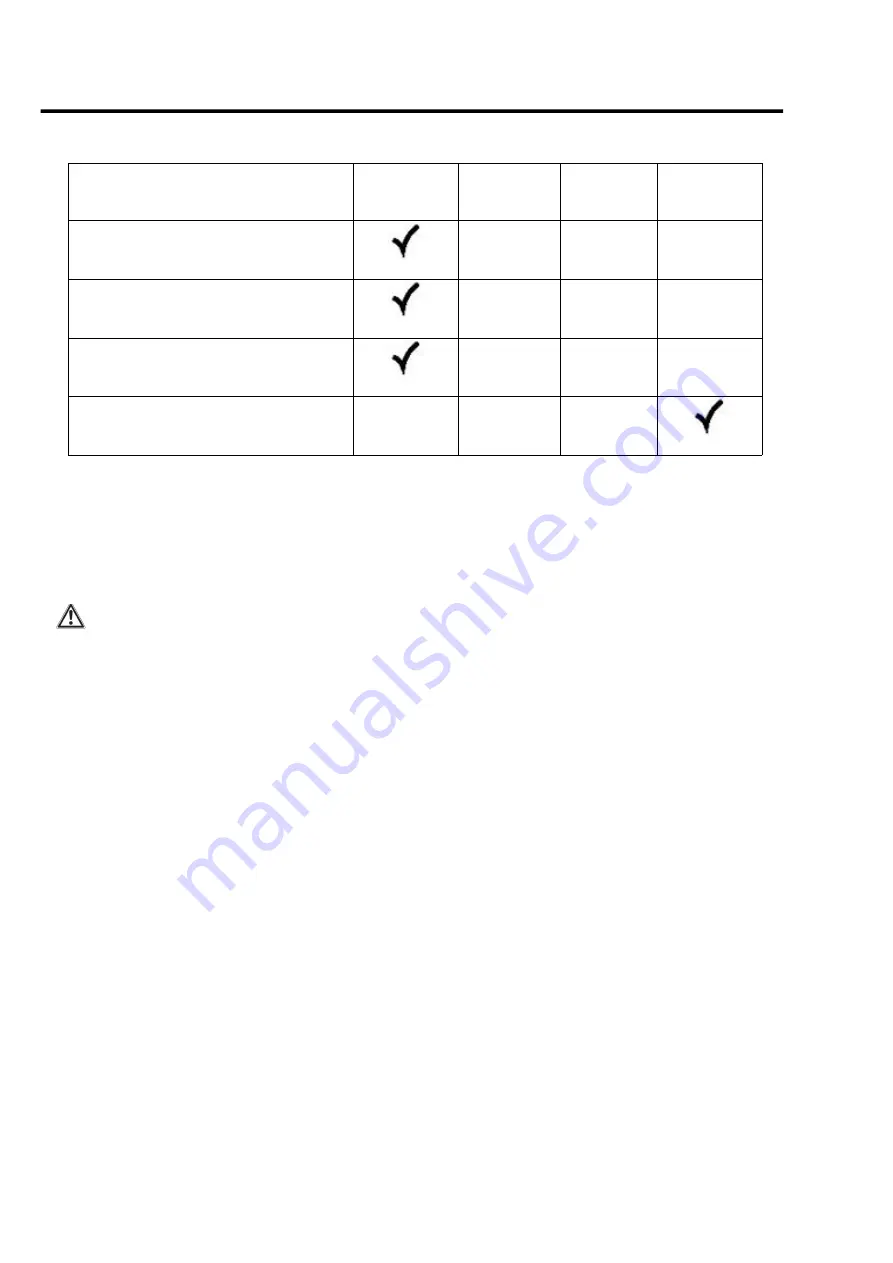
MAINTENANCE
MAINTENANCE SCHEDULE
PROCEDURES
BEFORE
EACH USE
25 HOURS
100
HOURS
AFTER
EACH USE
Hardware - Inspect & tighten
Engine & Air Filter - check & clean if
necessary
Oil, engine - check level
Wash Unit - Remove Grease & Debris
Maintenance
If you need to change the belts, please contact the distributor or local agent. Do not change them by yourself.
Residual risks
Even when the machine is used as prescribed it is not possible to eliminate all residual risk factors. The following
hazards may arise in connection with the power tool’s construction and design:
1.
Damage to lungs if an effective dust mask is not worn.
2.
Damage to hearing if effective hearing protection is not worn.
3.
Damages to health resulting from vibration emission if the power tool is being used over longer
period of time or not adequately managed and properly maintained.
WARNING
This machine produces an electromagnetic field during operation. This field may under some circumstances
interfere with active or passive medical implants. To reduce the risk of serious or fatal injury, we recommend
persons with medical implants to consult their physician and the medical implant manufacturer before operating
this machine.
19
Summary of Contents for FBAE200
Page 16: ...16 ...