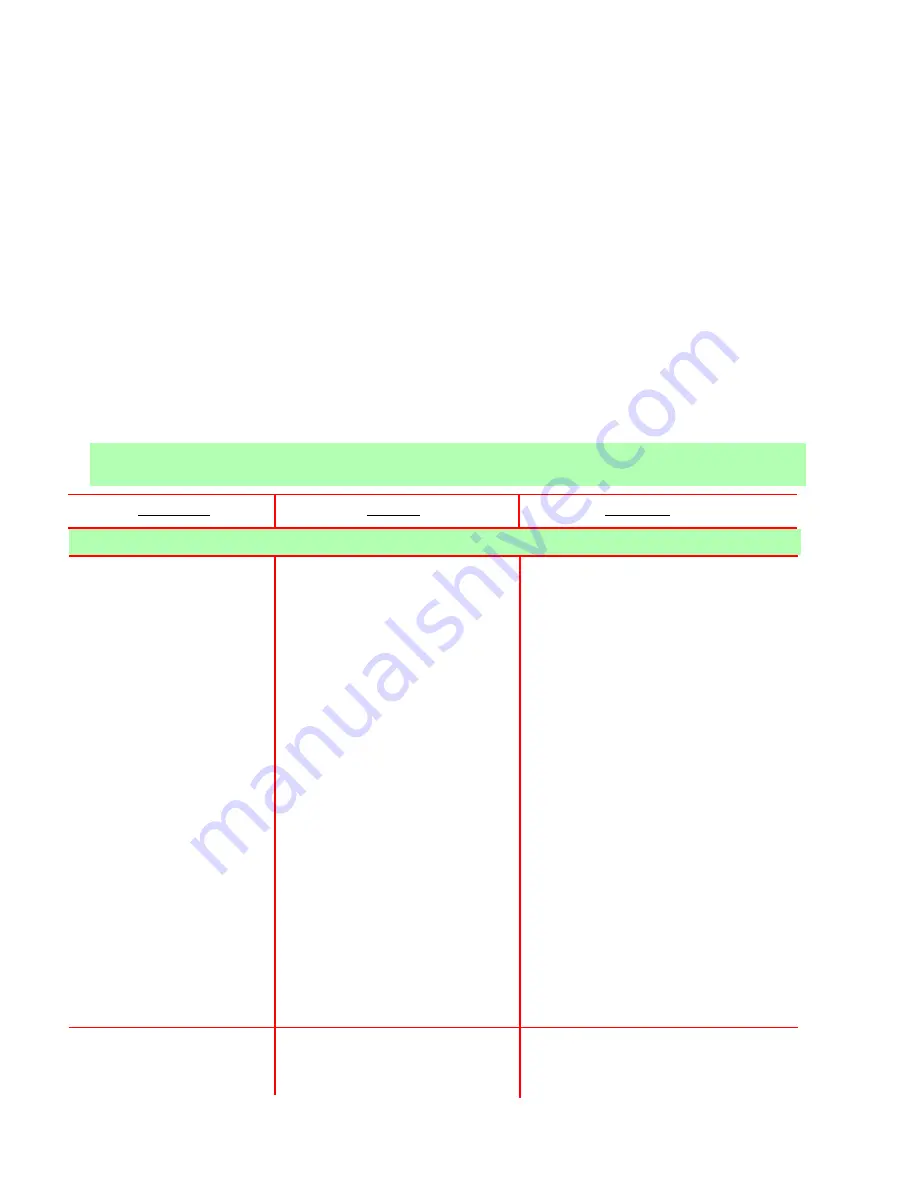
screen will display “Filling”.
Fill slowly and do NOT let the pressure drop more than three to four
(3-4) PSI.
13.3 LINE VOLTAGE DROP
The unit requires a separate electrical circuit complete with a 30 AMP breaker or fuse on a 30 AMP
service. The unit will not function properly if the line voltage drops more than 10 volts between the
power source and the machine.
13.4 LONG TUBING RUNS
A. Long runs of supply tubing can cause problems if the pressure drop (between the CO
2
tank or
syrup source and the unit) is too much. Runs longer than 25 feet (7.62 m) will require special
attention. The machine’s sensors may indicate that the machine is out of syrup, water, or CO
2
.
Consider the following solutions:
1.
Increase the tubing size from 3/8 inch diameter to 1/2 inch diameter.
2.
Install booster pumps in the supply lines. Use a vacuum regulating valve with syrup
booster pumps.
3.
Increase primary CO
2
regulator pressure from bulk or tank CO
2
to 105 - 120 PSIG (723.9
to 828.0 KPa). A secondary regulator will be necessary for pumps (syrup, water) to avoid
exceeding manufacturer’s recommended operating pressures.
14. TROUBLESHOOTING GUIDE
The following information is a listing of the most common problems that could keep the FBD553D
Dispenser from operating properly
.
Contact the factory for details, when necessary.
TROUBLE
CAUSE
REMEDY
MECHANICAL
14.1
Chamber will not fill.
A. “Fill“ off.
A. Press “Fill” button. “Filling” or
“Fill Hold” will appear on LCD
display.
B. Pressure in chamber above
B. Gently pull faceplate relief valve
“RFill” (refill) point.
ring to relieve pressure in chamber.
C. “Defrosting” or “Sleeping”.
C. Press “Def”. then “Run” Wait for
unit to freeze and red light to go
out.
D. Out of CO
2
, Syrup or Water.
D. Check LCD messages for
"Out of ……." condition.
E. Tank Pressure readout not
E. Observe "Tank Transducer" in
moving between 18 and
"Readouts". Check transducer and
40 psi or doesn’t lower when
replace if necessary.
chamber pressure is reduced.
F.
CO
2
solenoid valve won’t
F.
In “Manual On/Off, energize
open.
solenoid and check for 24VAC at
coil. Clean or replace solenoid if
necessary
G. Relay board not sending
G. Test solenoid relay on relay board
power to solenoid coils.
for 24VAC output and 5VDC input.
Replace Relay Board, if necessary.
H. Lower Board problem.
H. Test Lower Board for +5, +15, and
–15 outputs using test points (see
Figure 14.3). Replace Lower
Board, if necessary.
I.
353 VA Transformer problem.
I.
Test transformer for 220VAC input.
Also check for 24VAC and 12VAC
output (see Figure 14.3). Replace
transformer if necessary.
14.2
Chamber fills even
A. Solution solenoid plunger
A. In “Manual On/Off”, energize
when turned off
sticking.
solenoid and check for 24VAC at
coil. Clean or replace solenoid, if
necessary.
(Section 14.2 continued on next page.)
21