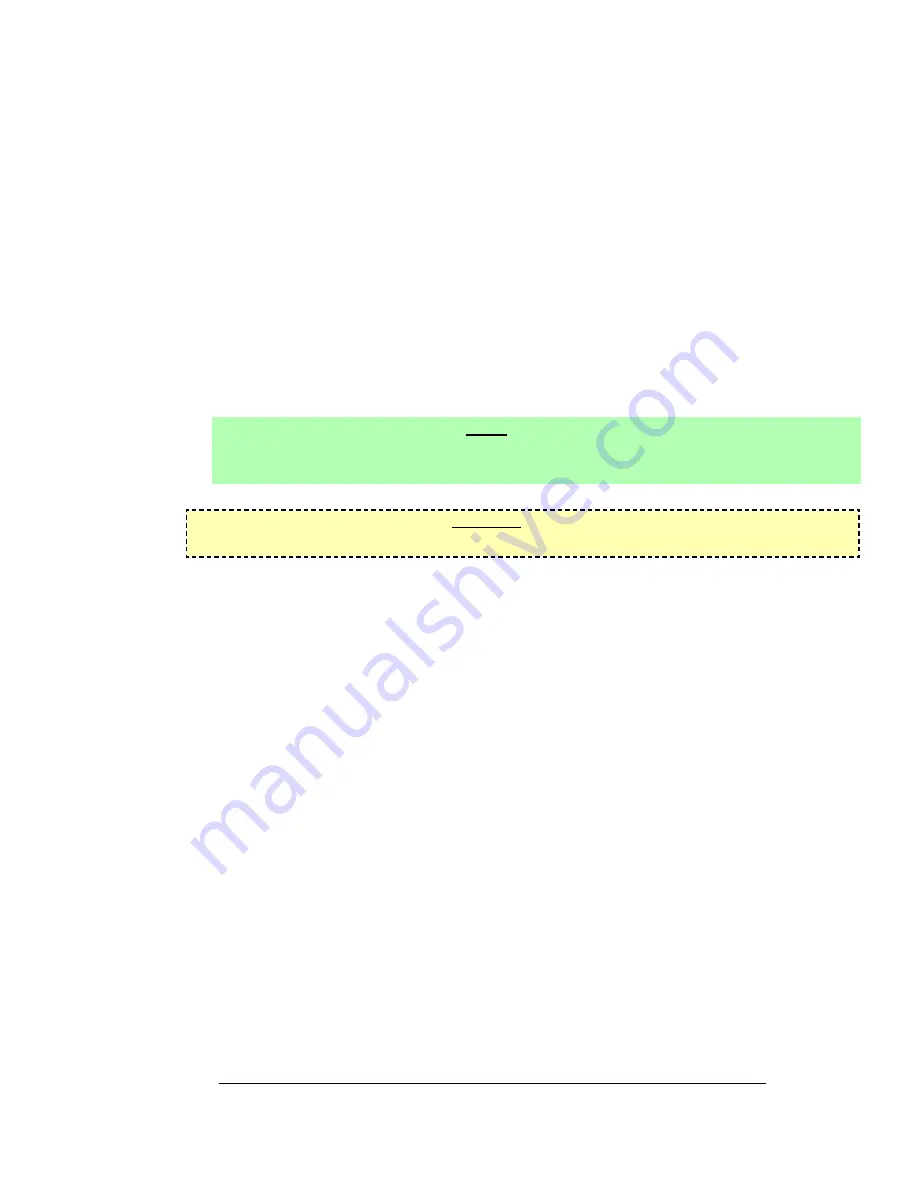
C. Water lines are not to be disconnected during the cleaning and sanitizing of syrup lines to avoid
contamination.
D. Do
NOT
use strong bleaches or detergents. They tend to discolor and corrode various
materials.
E. Do
NOT
use metal scrapers, sharp objects, steel wool, scouring pads, abrasives, solvents, etc.,
on the dispenser.
F.
Do
NOT
use hot water above 140°F (60°C). This may damage certain materials.
8.2
REQUIRED CLEANING EQUIPMENT
A. A mild soap solution (for example, Ivory Liquid, Calgon, etc.) mixed with clean, potable water at
a temperature of 90 to 110°F (32 to 44°C) should be used to clean the external components of
the equipment. Any equivalent mild soap solution may be used as long as it provides a caustic
based, non-perfumed, easily rinsed mixture containing at least two (2) percent sodium
hydroxide (NaOH). Rinsing must be thorough and use clean, potable water which is also at a
temperature of 90 to 110°F (32 to 44°C).
B. Sanitizing solutions should be prepared in accordance with the manufacturer's written
recommendations and safety guidelines. Any sanitizing solution may be used as long as it is
prepared in accordance with the manufacturer's written recommendations and safety guide-
lines, and provides 200 parts per million (PPM) available chlorine. Sanitizing solution is to be
purged from line(s) and equipment by flushing with product only until there is no after taste.
Do
not rinse with water.
NOTE
Please note that a fresh water rinse cannot follow sanitization of equipment. Purge only with
the end use product until there is no after taste in the product.
This is an NSF requirement.
8.3
DAILY CLEANING OF THE UNIT
CAUTION
DO NOT USE ABRASIVE TYPE CLEANERS.
A. On a daily basis, or more often if necessary, wash all exterior surfaces of unit with a mild soap
solution. Rinse with clean water. Wipe dry with a clean soft cloth.
B. Remove and wash drip tray in mild soap solution. Rinse with clean water. Reinstall drip tray on
unit.
8.4
SANITIZING THE SYRUP SYSTEMS
The unit should be sanitized every 90 days.
Prepare a chlorine solution (less than pH 7.0) containing
500 PPM available chlorine with clean, potable water at 90°F to 100°F (Note: 500 PPM is five (5) times
stronger than the usual recommended 100 PPM. This is required because the sanitizing solution will be
diluted with four (4) parts water when it enters the barrel). Any sanitizing solution may be used as long as
it is prepared in accordance with the manufactures safety guidelines and provides 500 PPM available
chlorine."
The following procedure takes about one (1) hour.
A. Press the "OFF" button, followed by the "DEF" button, for all three chambers. Remember, there
will be a two (2) minute delay before the unit begins defrosting.
B. After defrost, activate the left, center and right CO
2
solenoids by going to the "SERVICE
MENU/MANUAL ON/OFF" section of the menu.
C. Place a container under the valve and empty the barrels. Activate the beaters to facilitate the
removal of product.
D. Disconnect the BIB connectors from the syrup boxes and install BIB adapters (FBD
PN 05-0249) onto the BIB connectors. Activate the right, center, and left solution solenoids at
the "SERVICE MENU/MANUAL ON/OFF" section of the service menu until all syrup has been
evacuated from the lines. Purge barrel of product as necessary.
E. Turn off the solution solenoids and drain the barrels again.
F.
Turn off the CO
2
solenoids and beaters after the barrels are empty.
G. Relieve pressure by opening valves. Remove the faceplate to drain out excess product.
Replace the faceplates.
H. Prepare five (5) gallons of sanitizing solution
BUT ADD FIVE (5) TIMES THE AMOUNT OF
SANITIZER CONCENTRATE THAT THE SANITIZER MANUFACTURER RECOMMENDS
.
This is required because the solution will be diluted at about 4:1 in the barrel.
The water
temperature should be 110 to 115°F (44 to 46°C). If using a powder, stir the solution until
the sanitizing agent has completely dissolved.
14