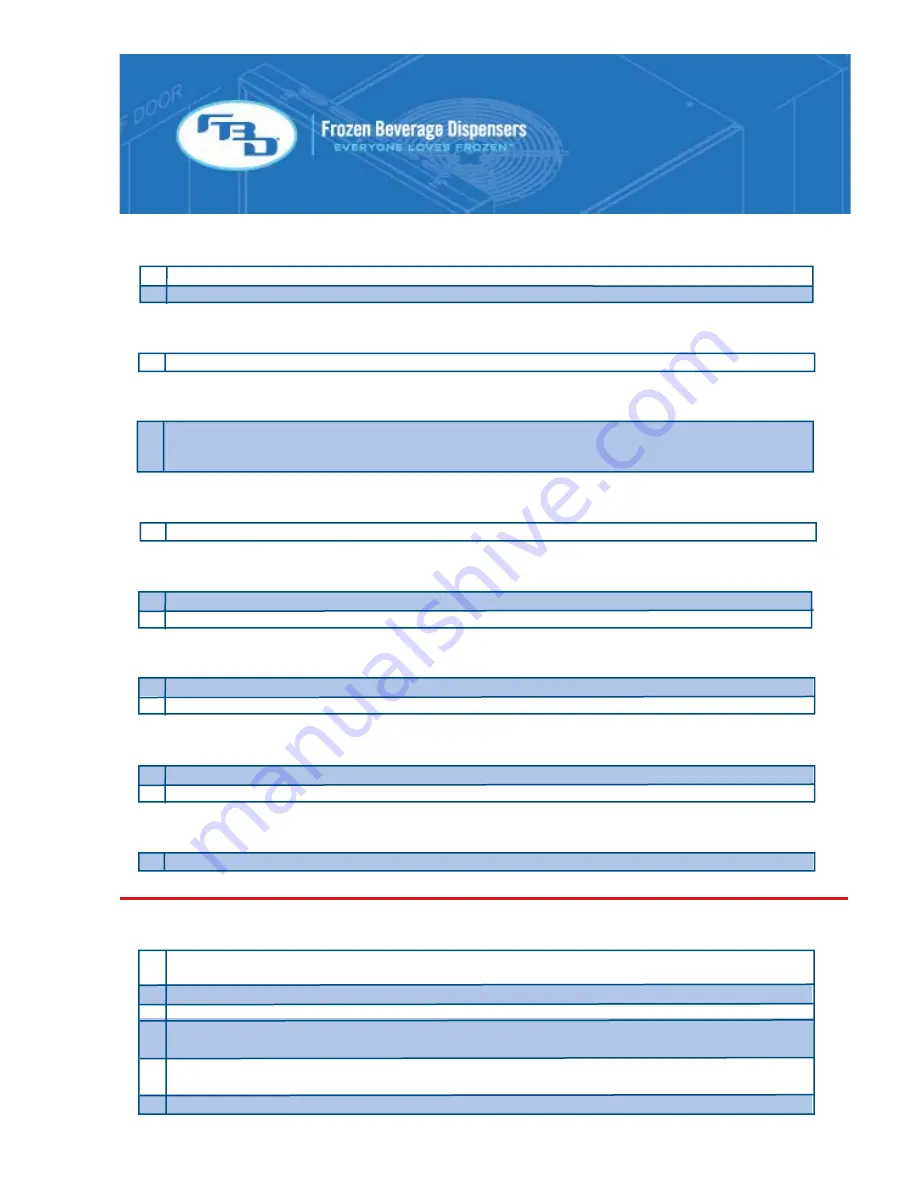
33
Error #140: Low regulated CO2 PSI
The regulated CO2 pressure dropped below 50 PSI.
1
Ensure the CO2 supply is not low.
2
Check the “carbonation” regulator on the header tray and ensure it is set to 60 PSI.
Error #150: High regulated CO2 PSI
The regulated CO2 pressure is above below 70 PSI.
1
Check the “carbonation” regulator on the header tray and ensure it is set to 60 PSI.
Error #160: Low Line Voltage
The voltage supply is below 200 volts
1
Install a boost transformer. Even if the voltage is slightly above 200 V a boost transformer may
be needed as fluctuations in power during the day or during unit operation may cause it to drop
below 200 volts and shut down the unit.
Error #170: High Line Voltage
The voltage supply is above 254 volts
1
Install a buck transformer.
Error #180: LPSI transducer
The low side refrigeration pressure is not reading correctly.
1
Ensure the pressure transducer is plugged in.
2
Replace the transducer if faulty.
Error #190: HPSI transducer
The high side refrigeration pressure is not reading correctly.
1
Ensure the pressure transducer is plugged in.
2
Replace the transducer if faulty.
Error #200: Return Temperature Sensor
The refrigeration return (suction) temperature sensor is not reading correctly.
1
Ensure the temperature sensor is plugged in.
2
Replace the sensor if faulty.
Error #210: Refrigeration Malfunction
The refrigeration pressures were not in the correct range.
1
Run the fill diagnostic sequence to determine the reason for the failure.
Diagnostic Fault Codes
The following codes are faults that can be displayed after running a diagnostic sequence.
Error #500: Fan not turning on
1
Remove control board and check for a blown fan fuse (F1 and F2). If a fuse is blown then a
fan or capacitor malfunction may be possible.
2
If fuses are OK, reinstall control board.
3
Disconnect wiring harnesses at fan capacitor.
4
Manually turn fan on and check for line voltage (230V) between the connectors removed from
the capacitor. If no voltage is present then replace control board.
5
If correct voltage is present then substitute a “known to be good” capacitor and try to operate
fan
again.
6
If fan fails to start with good capacitor then replace both fan and capacitor.
Summary of Contents for 77 Series
Page 1: ...772 773 774 24 2396 0001 Rev C 07 30 2013...
Page 38: ...38 772 Mounting Dimensions 773 Mounting Dimensions...
Page 40: ...40 WIRING SCHEMATIC DIAGRAM...
Page 41: ...41...