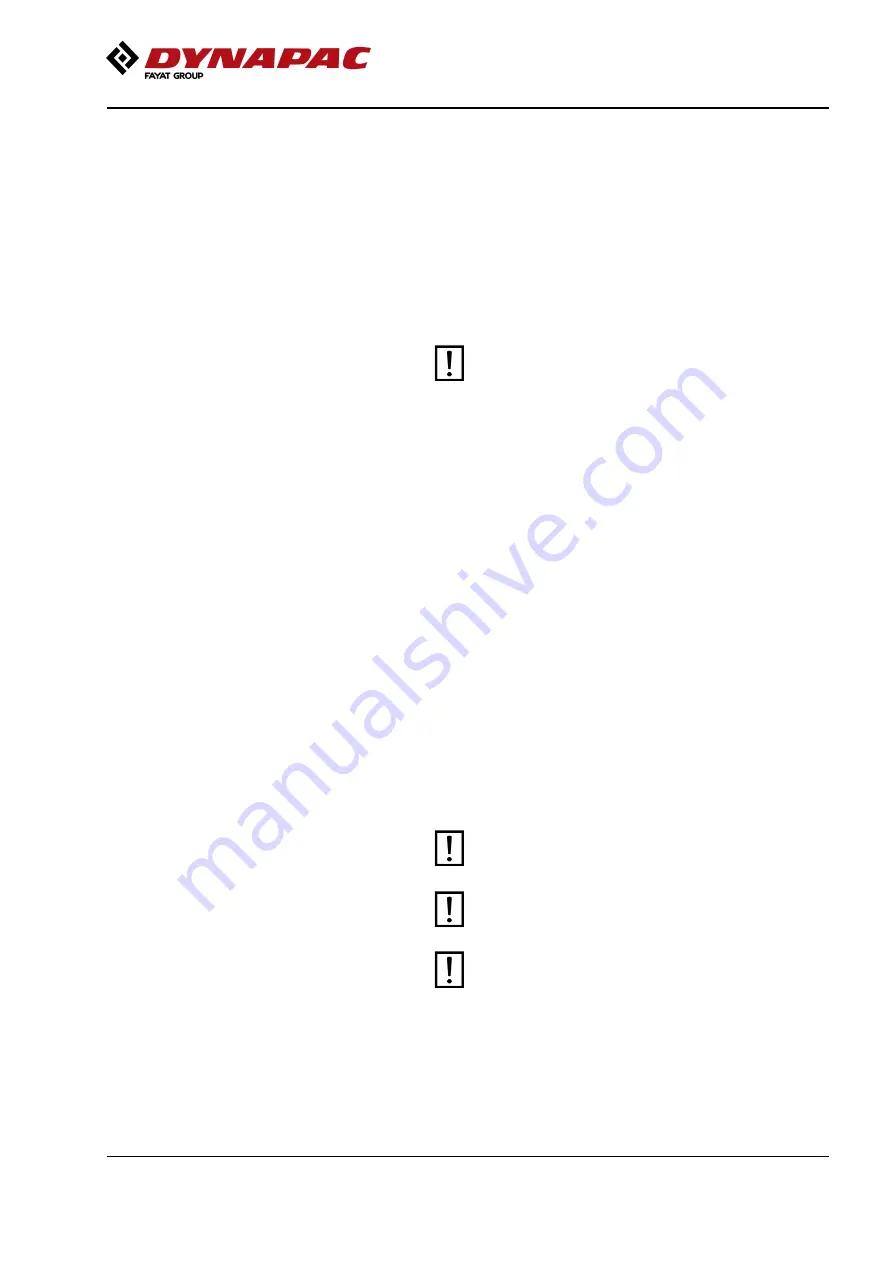
Special instructions
4812159001_I.pdf
2019-11-05
Special instructions
Standard lubricants and other recommended
oils and fluids
Before leaving the factory, the systems and
components are filled with the oils and fluids specified
in the lubricant specification. These are suitable for
ambient temperatures in the range -15°C to +40°C
(5°F - 105°F).
The maximum ambient temperature for
biological hydraulic fluid is +35°C (95°F).
The maximum ambient temperature for
biological hydraulic fluid is +35°C (95°F).
Higher ambient temperatures, above +40°C
(104°F)
For operation of the machine at higher ambient
temperatures, however m50°C (122°F), the
following recommendations apply:
The diesel engine and hydraulic system can be run at
this temperature using normal oil, but in other
components that use transmission oil, Shell Spirax S3
AX85W/140, API GL-5 or equivalent must be used.
Temperatures
The temperature limits apply to standard versions of
rollers.
Rollers equipped with additional equipment, such as
noise suppression, may need to be more carefully
monitored in the higher temperature ranges.
High pressure cleaning
Do not spray directly onto electrical components.
Do not use a high-pressure water jet on the
instrument panel/display.
Do not use a high-pressure water jet on the
instrument panel/display.
Detergent that can destroy electrical parts, or
which is conductive, must not be used.
Detergent that can destroy electrical parts, or
which is conductive, must not be used.
In certain cases there is an electrical control lever
and associated electronic control unit (ECU) in
the engine compartment, which must not be
washed with a high-pressure jet or with any water
at all. It is sufficient to wipe these off.
The same applies to the engine electronic control
unit (engine ECU).
In certain cases there is an electrical control lever
and associated electronic control unit (ECU) in
the engine compartment, which must not be
washed with a high-pressure jet or with any water
at all. It is sufficient to wipe these off.
The same applies to the engine electronic control
unit (engine ECU).
Place a plastic bag over the fuel filler cap and secure
11
Summary of Contents for DYNAPAC CA2800
Page 2: ......
Page 12: ...e 4812159001_I pdf 2019 11 05...
Page 16: ...Introduction 4812159001_I pdf 2019 11 05 4...
Page 22: ...Safety Optional 4812159001_I pdf 2019 11 05 10...
Page 26: ...Special instructions 4812159001_I pdf 2019 11 05 14...
Page 70: ...Machine description 4812159001_I pdf 2019 11 05 58...
Page 90: ...Operation 4812159001_I pdf 2019 11 05 78...
Page 102: ...Operating instructions Summary 4812159001_I pdf 2019 11 05 90...
Page 104: ...Preventive maintenance 4812159001_I pdf 2019 11 05 92...
Page 114: ...Maintenance Maintenance schedule 4812159001_I pdf 2019 11 05 Service Checklist 102...
Page 120: ...Maintenance 10h 4812159001_I pdf 2019 11 05 108...
Page 126: ...Maintenance first 50h 4812159001_I pdf 2019 11 05 114...
Page 128: ...Maintenance 50h 4812159001_I pdf 2019 11 05 116...
Page 169: ......
Page 170: ...Dynapac Compaction Equipment AB Box 504 SE 371 23 Karlskrona Sweden www dynapac com...