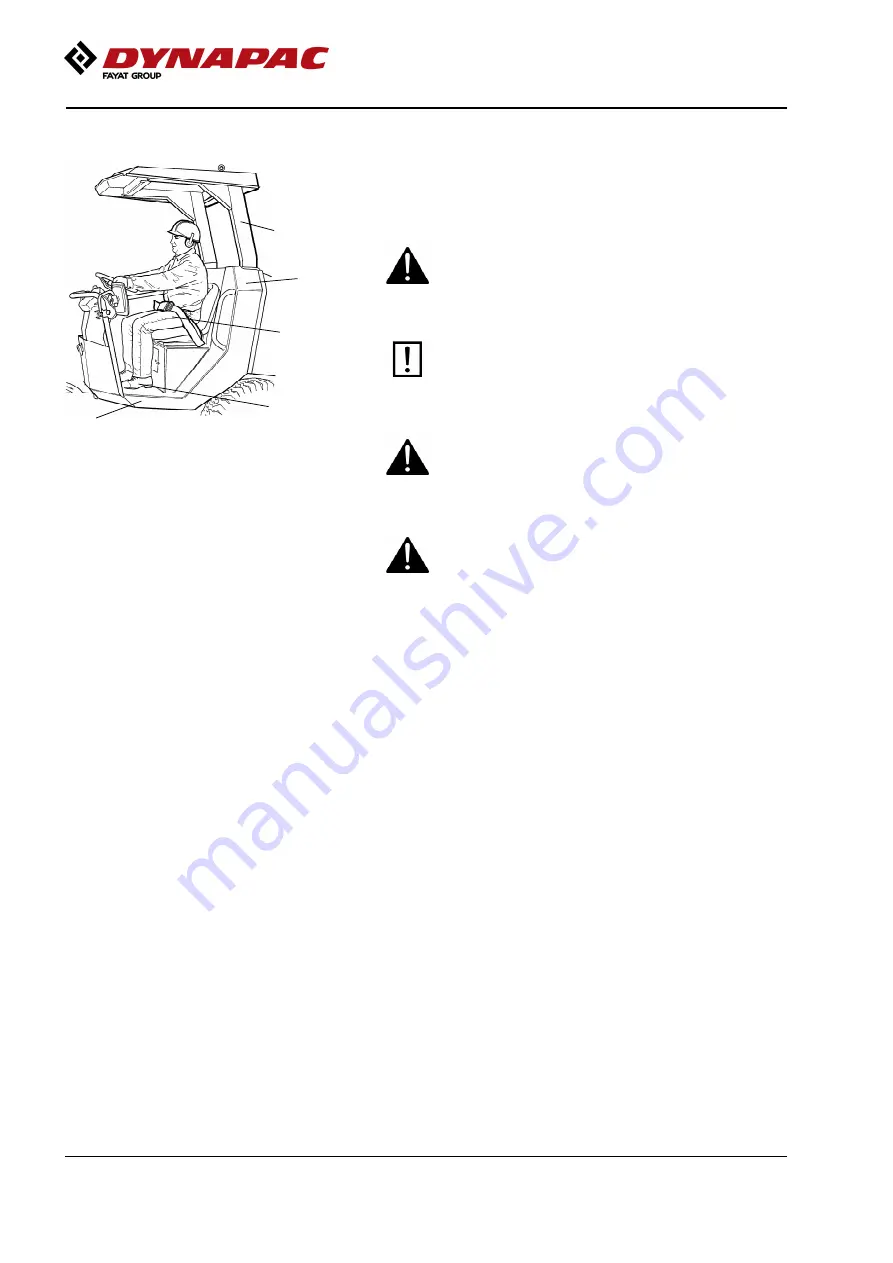
Operation
4812165001.pdf
2023-05-26
Operator position
3
1
3
2
4
Fig. Operator's station
1. Seat belt
2. ROPS structure
3. Rubber element
4. Anti-slip
If a ROPS (2) (Roll Over Protective Structure) or
a cab is fitted to the roller, always wear the seat belt
(1) provided and wear a protective helmet.
Replace the seat belt (1) if it shows signs of
wear or has been subjected to high levels
of force.
Replace the seat belt (1) if it shows signs of
wear or has been subjected to high levels
of force.
Check that rubber elements (3) on the platform
are intact. Worn elements will impair comfort.
Check that rubber elements (3) on the platform
are intact. Worn elements will impair comfort.
Ensure that the anti-slip (4) on the platform is in
good condition. Replace where anti-slip friction
is poor.
Ensure that the anti-slip (4) on the platform is in
good condition. Replace where anti-slip friction
is poor.
If the machine is fitted with a cab, make sure
that the door is closed when in motion.
If the machine is fitted with a cab, make sure
that the door is closed when in motion.
52
Summary of Contents for DYNAPAC CA1300 D
Page 2: ......
Page 22: ...Introduction 4812165001 pdf 2023 05 26 4 ...
Page 28: ...Safety Optional 4812165001 pdf 2023 05 26 10 ...
Page 49: ...Machine description 4812165001 pdf 2023 05 26 4812129673 Warning CALIFORNIA Proposition 65 31 ...
Page 57: ...Machine description 4812165001 pdf 2023 05 26 39 ...
Page 66: ...Machine description 4812165001 pdf 2023 05 26 48 ...
Page 96: ...Operating instructions Summary 4812165001 pdf 2023 05 26 78 ...
Page 98: ...Operating instructions Summary 4812165001 pdf 2023 05 26 80 ...
Page 104: ...Maintenance Lubricants and symbols 4812165001 pdf 2023 05 26 86 ...
Page 117: ...Maintenance Maintenance schedule 4812165001 pdf 2023 05 26 Service Checklist 99 ...
Page 118: ...Maintenance Maintenance schedule 4812165001 pdf 2023 05 26 100 ...
Page 140: ...Maintenance measures 250 h 4812165001 pdf 2023 05 26 122 ...
Page 194: ...Maintenance measures 1500 h 4812165001 pdf 2023 05 26 176 ...
Page 238: ...Maintenance 3000 5000 7000 h 4812165001 pdf 2023 05 26 220 ...
Page 284: ...Dynapac Compaction Equipment AB Box 504 SE 371 23 Karlskrona Sweden www dynapac com ...