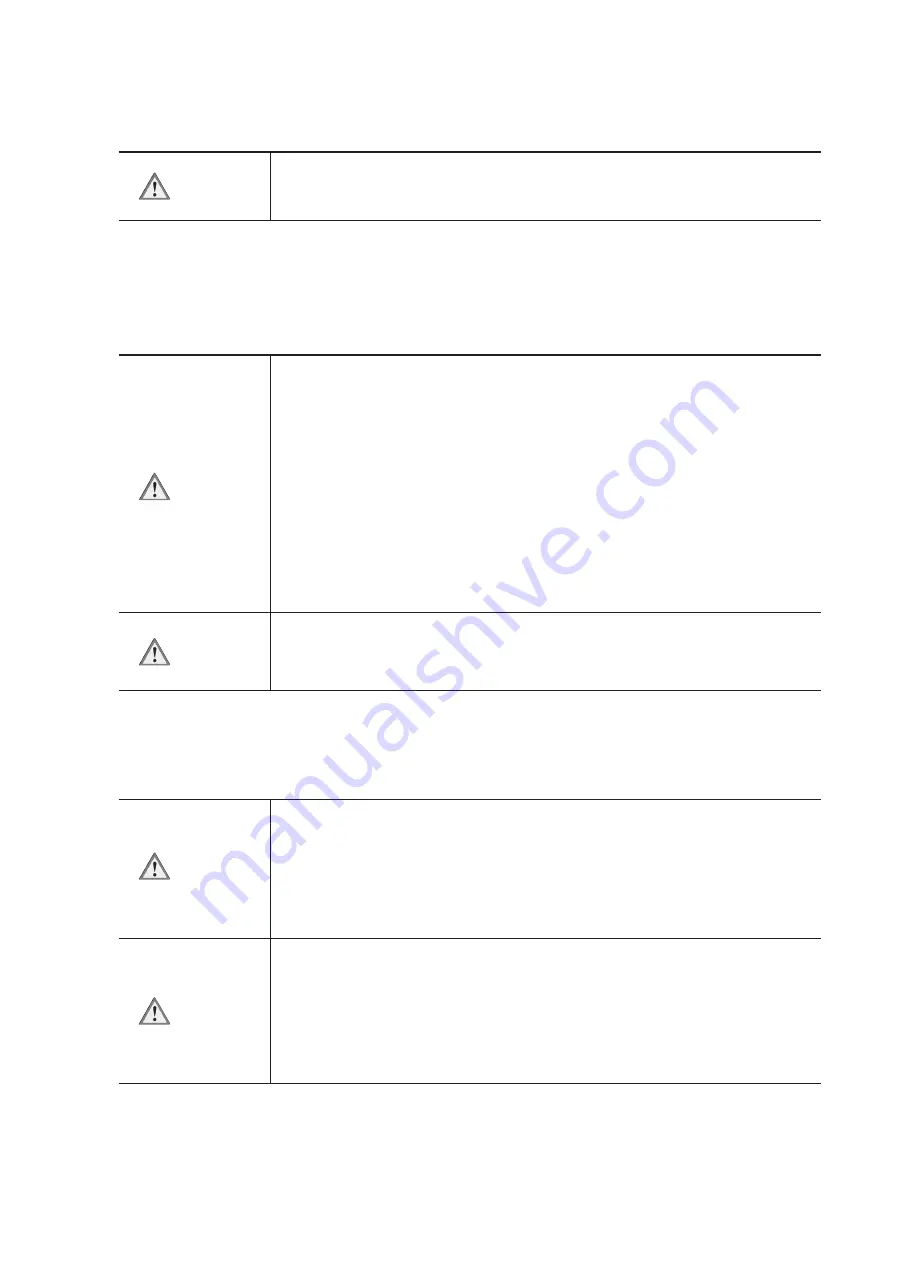
www.fastech.co.kr - 4
◆ Check the Product
Check the Product is damaged or parts are missing.
Otherwise, the machine may get damaged or the user may get injured.
Attention
◆ Installation
Carefully move the Ezi-SERVO MINI.
Otherwise the Product may get damaged or User's foot may get injured by dropping the
product.
Use non-flammable materials such as metal in the place where the Ezi-SERVO MINI is to
be installed.
Otherwise, a fire may occur.
When installing several Ezi-SERVO MINI in a sealed place, install a cooling fan to keep
the ambient temperature of the Ezi-SERVO MINI as 50℃ or lower.
Otherwise, a fire or other kinds of accidents may occur due to overheating.
The process of Installation, Connection, Operation, Checking and Repairing should be
done with qualified person.
Otherwise, a fire or other kinds of accidents may occur.
Attention
Warning
◆ Connect Cables
Keep the rated range of lnput Voltage for Ezi-SERVO MINI.
Otherwise, a fire or other kinds of accidents may occur.
Cable connection should follow the wiring diagram.
Otherwise, a fire or other kinds of accidents may occur.
Before connecting cables, check if input power is off.
Otherwise, an electric shock or a fire may occur.
The case of the Ezi-SERVO MINI is insulated from the ground of the internal circuit by
the condenser. Ground the Ezi-SERVO MINI.
Otherwise, an electric shock or a fire may occur.
Attention
Warning