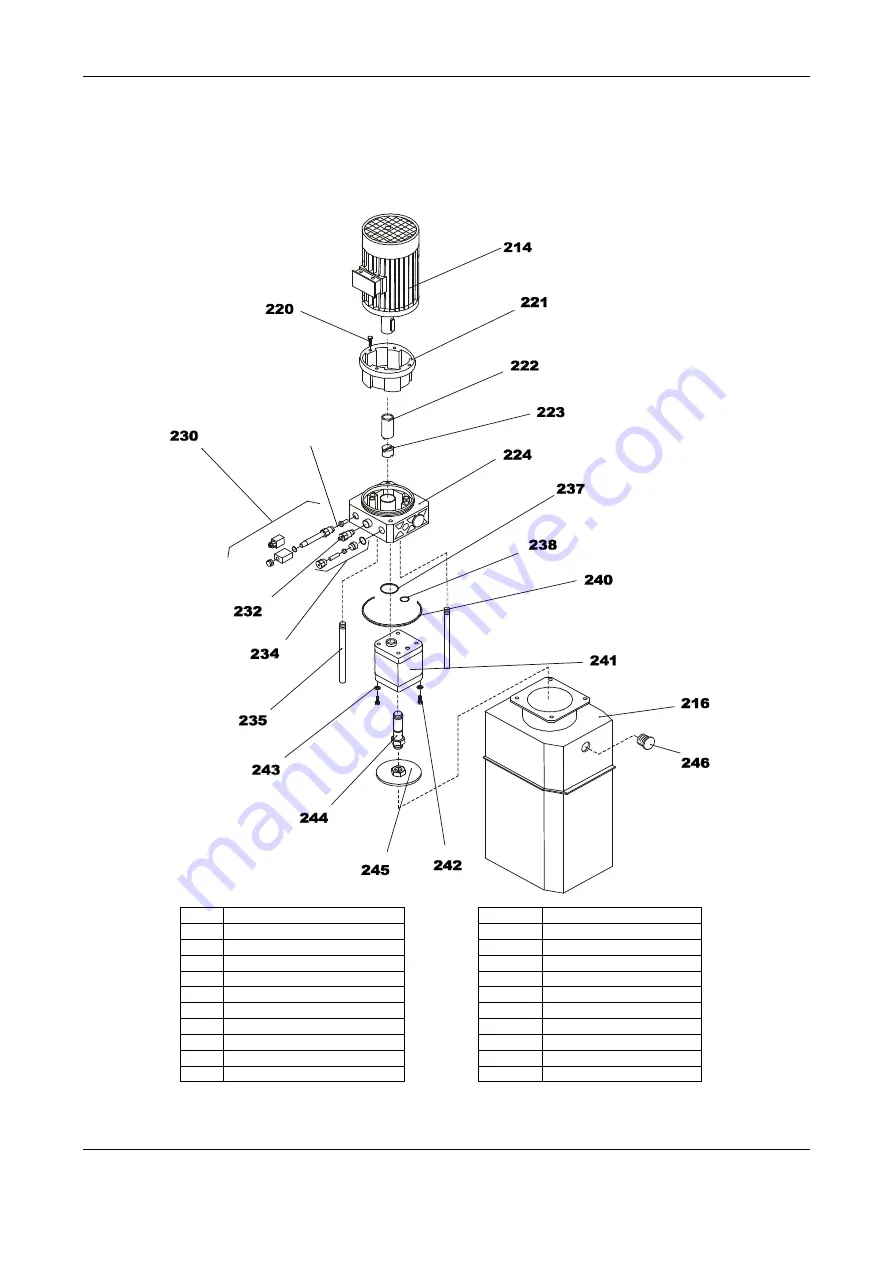
Use and Maintenance Manual
– Spare Parts
Page 29
TAB.6
– HYDRAULIC CONTROL UNIT
247
214
THREE PHASE MOTOR
214
SINGLE PHASE MOTOR
216
TANK
220
SCREW
221
FLANGE
222
JOINT
223
JOINT
224
COLLECTOR
230
OIL SOLENOID VALVE
232
RELIEF VALVE
234
CHECK VALVE
235
DISCHARGE TUBE
237
O RING
238
O RING
240
O RING
241
PUMP
242
SCREW
243
WASHER
244
SUCTION TUBE
245
FILTER
246
LOADING PLUG
247
CHOKE
Summary of Contents for FZ63/3S
Page 2: ......
Page 32: ...Page 32 Use and Maintenance Manual Spare Parts THREE PHASE ELECTRIC DIAGRAM...
Page 33: ...Use and Maintenance Manual Spare Parts Page 33...
Page 35: ...Use and Maintenance Manual Spare Parts Page 35 SINGLE PHASE ELECTRIC DIAGRAM...
Page 36: ...Page 36 Use and Maintenance Manual Spare Parts...